Sphalerite is a significant zinc ore widely used in zinc smelting and related product manufacturing. It often contains associated minerals such as pyrite and magnetite, making the choice of mineral processing technology dependent on the physical and chemical properties of the ore. As mineral resources deplete, improving sphalerite recovery and processing efficiency has become a focal point in the industry. Currently, three main processing methods are used: flotation, combined flotation and magnetic separation, and bioleaching-induced flotation. Selecting the appropriate method based on ore complexity and processing requirements directly affects the quality of the final concentrate. The following sections will introduce these three methods to provide insights for the development and utilization of zinc ore resources.
Use the table of contents below to navigate through the guide:
01Sphalerite flotation method
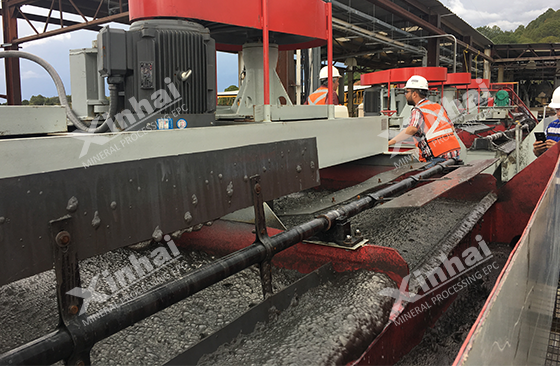
At present, the flotation method is often used in the ore dressing plant to treat sphalerite. Its main principle is to achieve the separation of minerals based on the difference in the physical and chemical properties of the mineral surface. The flotation process is applied to the treatment of fine-grained sphalerite, which can effectively separate zinc sulfide and associated minerals. Collectors, regulators and frothers are used in the flotation process to improve the recovery rate and concentrate grade of zinc ore.
The flotation process has the following steps:
1. Ore crushing and grinding: Use a crusher, ball mill or rod mill to crush the ore particle size to a suitable particle size (-74 μm particle size accounts for 70-90%) to increase the degree of monomer dissociation of the mineral.
2. Slurry adjustment: Regulate the pH value of the slurry, add lime to adjust the pH value of the slurry to 9-11, in order to inhibit the flotation of sulfide minerals such as pyrite.
3. Reagent addition:
- Activator: such as CuSO₄, used to improve the floatability of sphalerite.
- Collectors: such as butyl xanthate, to improve the flotation recovery rate of ZnS.
- Depressants: such as NaCN or ZnSO₄, used to suppress pyrite and improve the selectivity of mineral processing.
- Frothing agents: pine oil, cresol, etc., to enhance the stability of bubbles and improve the adhesion effect of mineral particles.
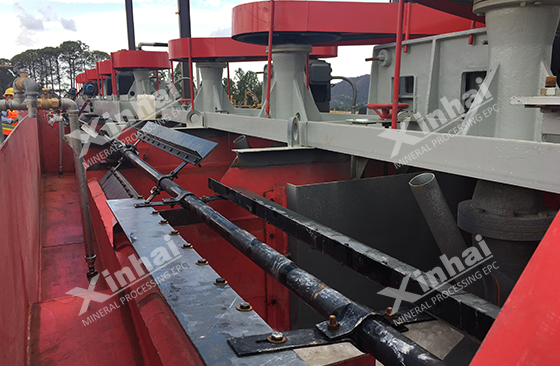
4. Flotation: Bubbles are introduced into the flotation equipment, sphalerite adheres to the bubbles, floats to the surface of the pulp, and then scraped.
5. Dehydration of concentrate: thickeners and filters are used for dehydration to improve the grade of concentrate.
In order to further optimize the flotation process and improve the recovery rate, multi-stage grinding and multi-stage flotation processes can be used to avoid over-grinding. In order to further improve the grade of zinc concentrate, multiple concentration processes can be used.
02Sphalerite flotation + magnetic separation method
When there are more magnetic minerals such as magnetite and hematite in sphalerite, flotation + magnetic separation can be used to improve the purity of zinc concentrate.
The process flow is as follows:
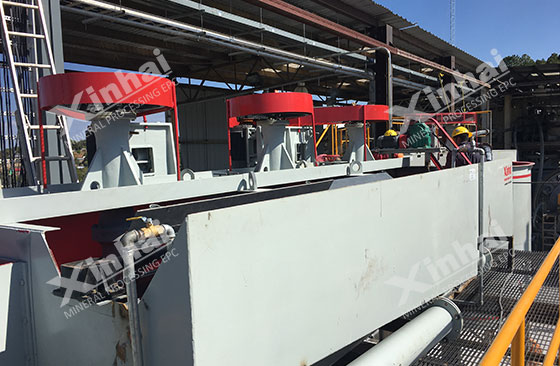
1. Preliminary flotation: Use copper sulfate to activate sphalerite, and use xanthate collectors to float out zinc sulfide concentrate.
2. Magnetic separation treatment: The flotation tailings enter the high-gradient magnetic separation equipment for treatment, which can effectively remove magnetic iron minerals and improve the grade of zinc concentrate.
3. Re-floatation: Re-floatation of magnetic tailings can improve the utilization rate of mineral resources. Whether re-floatation is needed needs to be selected according to the characteristics of the ore.
In order to improve the mineral processing indicators of flotation + magnetic separation process, it is generally necessary to control the magnetic field strength, pulp concentration, desludging process, etc. The magnetic field strength is generally controlled at 0.8-1.5T, which can effectively separate iron minerals. The pulp concentration needs to be guaranteed at 25-35% to avoid the pulp being too thin or too concentrated to affect the mineral processing effect. The desludging process can remove fine particles in advance and improve the sorting efficiency.
03Microbial induced flotation method of sphalerite
This flotation method is emerging and eco-friendly. The principle of the microbial induced flotation method is that uses biosurfactants produced by microbial metabolism to change the hydrophilicity or hydrophobicity of the mineral surface to achieve mineral separation.
The followings are the core steps
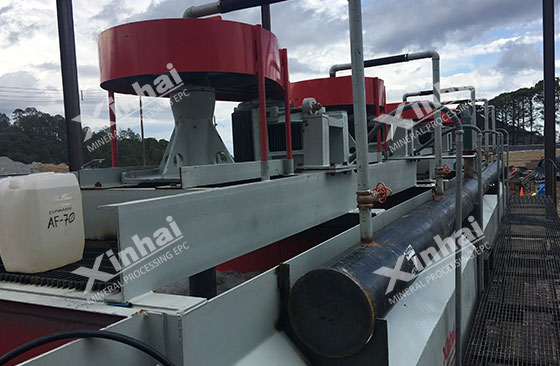
1. Microbial culture: Cultivate suitable microbial communities in the slurry, such as sulfur-loving bacteria (sulfur-oxidizing bacteria, thiobacillus).
2. Slurry pretreatment: Microorganisms act on the ore surface to change the surface charge and floatability of the mineral.
3. Flotation separation: After the surface modification of the mineral induced by microorganisms, it enters the flotation process to achieve selective recovery.
Microbial flotation is environmentally friendly and pollution-free. It can reduce the use of flotation reagents. It also has good selectivity and can effectively separate complex paragenetic minerals.This method is mainly suitable for low-grade ores to improve resource utilization.
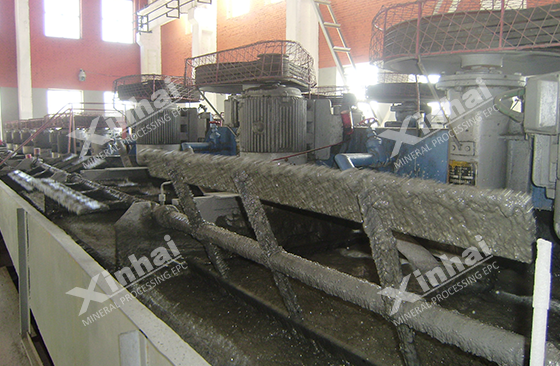
As mineral resources become increasingly depleted, improving mineral processing recovery and environmental protection has become the key. Sphalerite beneficiation is still mainly based on flotation. High-iron content zinc ores can be separated by flotation + magnetic separation, and microbial induced flotation has potential as an environmental protection technology. With rich experience and technical strength, Xinhai Mining can provide efficient, energy-saving and eco-friendly zinc mineral processing technology and equipment, we can also combine intelligent control to improve mineral processing efficiency. Xinhai Mining is committed to the development of green mineral processing technologies, such as non-toxic flotation agents and wastewater treatment, to promote the sustainable development of the industry and continue to provide innovative solutions for the global mining industry.