Zinc and lead are widely used in industries such as construction, automobiles, electronics and batteries. Both sphalerite and galena are valuable sources of zinc and lead, essential metals in these industries. The beneficiation process can extract and concentrate these valuable minerals and improve the utilization rate of lead-zinc ore resources. This article will introduce you to the flotation separation method of sphalerite with galena and the precautions during flotation.
Use the table of contents below to navigate through the guide:
01Flotation separation method of sphalerite with galena
Flotation is the most effective method for separating galena and sphalerite. The technique utilizes the mineral surfaces' hydrophobicity difference to separate the valuable minerals from the accompanying chalcopyrite minerals.
The lead zinc beneficiation equipment includes XCF flotation machines, KYF flotation machines, SF flotation machines, JJF flotation machines, chemical stirring tanks, and high-efficiency stirring tanks.Here's the typical process:

1. Crushing and grinding process:
The ore containing sphalerite and galena first enters the crusher to be broken into smaller particles for further processing. It is then ground into a fine powder using a mill. This step increases the surface area of the ore, allowing the valuable minerals to be more fully dissociated.
2. Froth flotation process:
Froth flotation is a method widely used to separate minerals from ores. During this process, collectors are added to the slurry. The collector selectively attaches to the surface of valuable minerals (sphalerite and galena) while repelling gangue minerals. Air foam is then introduced into the slurry, causing the valuable minerals to float to the surface to form foam, which can be collected.
Commonly used collectors include xanthates (e.g., potassium ethyl xanthate, PEX) and dithiophosphates, typically dosed at 50–150 g/t depending on the ore properties.
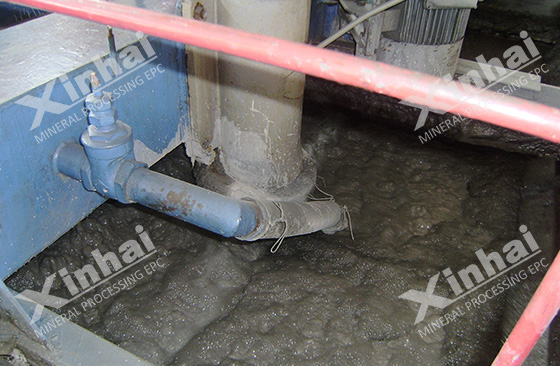
3. Differential flotation process:
Due to their different flotation properties, differential flotation separates sphalerite and galena. For selective separation, depressants such as sodium cyanide (100–300 g/t) or zinc sulfate (500–1000 g/t) are introduced to inhibit sphalerite flotation while galena is recovered first. Lime is added to maintain an alkaline pH (typically 8–10), stabilizing the flotation environment. An efficient and precise separation can be achieved by carefully adjusting reagent types, dosages, and flotation conditions.
4. Dehydration and filtration process:
Once the foam is collected, it is usually dewatered and filtered to remove excess water and obtain a concentrated mineral product. Various methods, such as filtration, centrifugation or drying, can be used to achieve this.

5. Smelting and refining process:
The concentrated sphalerite and galena products are further processed through smelting and refining operations to obtain pure zinc and lead metals, respectively. Smelting is the process of heating a concentrate with a suitable flux in a furnace to remove impurities and keep the metal in a molten state. The metal is then further refined using refining processes such as electrolysis or other purification techniques.
02Sphalerite and Galena Flotation: What You Must Know
1. Pulp acid pH adjustment: The pH value (pH value) in the flotation process has an important impact on the flotation effect. Properly adjusting the pH can improve the flotation performance of valuable minerals and increase the beneficiation efficiency.
2. Collector selection: Selecting a suitable collector is a key step in the sphalerite flotation process. The collector should be selectively adsorbed on the surface of valuable minerals, and at the same time have a small adsorption capacity for gangue minerals. Different ore properties may require different collector options.

3. Depressants application: Due to the different flotation properties of sphalerite and galena, it may be necessary to use an depressant to inhibit the flotation of one of the minerals. The choice and dosage of depressants need to be optimized for effective separation.
4. Foam generation and control: Foam is the key to bringing valuable minerals to the liquid surface in the flotation process. Proper bubble generation and control can improve flotation performance. Note the effect of bubble size, bubble generation rate, and bubble attachment on the flotation process.
5. Flotation leaching time: Flotation leaching time is an important factor affecting the flotation effect. Proper leaching time can fully release valuable minerals and achieve effective separation.
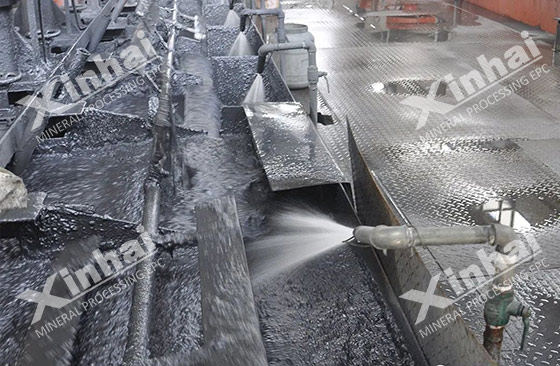
6. Flotation temperature and agitation intensity: temperature and agitation intensity play an important role in the dispersion and mixing of suspended solids during flotation. Proper temperature and stirring intensity can improve flotation effect and beneficiation efficiency.
7. Flotation wastewater treatment: The wastewater generated during the flotation process may contain chemicals and solid particles, which need to be properly treated and discharged to reduce the impact on the environment.
The above is the flotation process of sphalerite and galena and the precautions in the process. Due to the different characteristics of different ores, the flotation process should be selected and optimized according to their characteristics. Xinhai Mining recommends to conduct mineral processing test analysis and formulate a suitable lead-zinc mineral processing plan to improve the mineral processing efficiency and resource utilization.