In the flotation process, the importance of the slurry agitator tank is often
underestimated. However, effective contact and efficient interaction between
ore, reagents, and air are key to improving flotation efficiency—and this is
precisely the role of the slurry agitator tank.
Xinhai's slurry agitator tank has taken slurry agitator performance to a new
level through fluid dynamics optimization.Tests have shown that it can improve the mineral recovery rate by more than
1%. (Based on a plant processing 10,000 tons per day, this translates to an
annual revenue increase of over 1.5 million USD.)
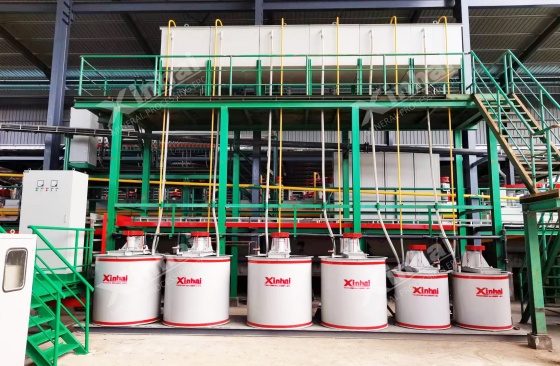
Use the table of contents below to navigate through the guide:
01Disadvantages of traditional slurry agitator tanks
1.The structural design is unreasonable, and there are dead zones
inside the tank
Traditional slurry agitator tanks typically feature a straight cylindrical
body with a flat bottom design. This causes a sudden drop in flow velocity in
areas more than 30 cm from the impeller, leading to the formation of permanent
sedimentation zones.
Additionally, this structure results in uneven reagent distribution.
Testing at a lead-zinc mine revealed that the reagent concentration at the
tank edges was only 43% of that in the central area, leading to excessive
reagent consumption and significant waste.
2.Impeller design is backward
The impeller of a traditional slurry agitator tank typically has a small
diameter, low linear speed (1–2 m/s), and a braided or spiral shape. This design
results in weak agitation performance, inadequate mixing, and low negative
pressure within the tank. As a consequence, the circulation capacity is reduced,
and energy utilization is limited to only 35%, making it difficult to achieve an
ideal agitation effect.
3.Poor adhesion efficiency
The conventional agitation method results in bubble coverage of less than
60%, leading to uneven bubble distribution and a limited mineral-gas contact
area. Reagents are adsorbed onto the surface of mineral particles in a "spotted"
pattern, resulting in low adhesion efficiency.
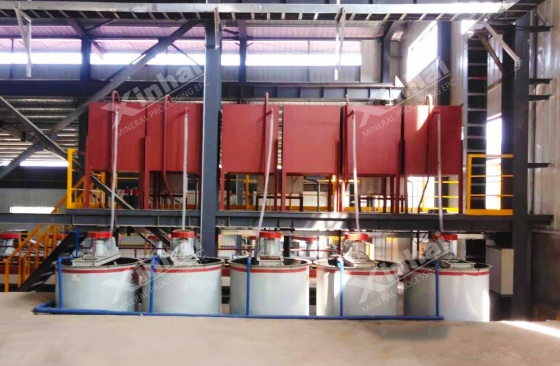
02Features of Xinhai Slurry Agitator Tank
The high-efficiency slurry agitator tank developed by Xinhai avoids the
above-mentioned shortcomings. Designed from both the impeller and circulation
systems, it features strong circulation capacity and thorough mixing.
1.Umbrella-Shaped Impeller System
Large diameter and high linear speed design: The impeller diameter is
increased and paired with special alloy materials to enhance bending strength.
Linear speed reaches 5–8 m/s, tripling the shear rate and significantly
improving agitation capacity. The umbrella-shaped surface guides the slurry to
form both axial main circulation and radial diffusive flow, increasing
circulation volume by 220%. The negative pressure reaches 15–20 kPa, enabling
forced mixing of reagent microbubbles.
2.Three-Stage Circulation Enhancement System
Built-in circulation body: The internal circulation structure confines
high-energy agitation to the core zone. The flow rate inside the tank exceeds 3
m/s, ensuring forced convection of ore, reagent, and gas phases for complete
mixing.
Vortex injection device: An inclined nozzle at the bottom sprays slurry at a
pressure of 0.8 MPa, reducing bottom sediment to below 0.05%. A
three-dimensional cross-flow field is formed, increasing the probability of
bubble-mineral attachment to 92% (compared to ≤75% in traditional
equipment).
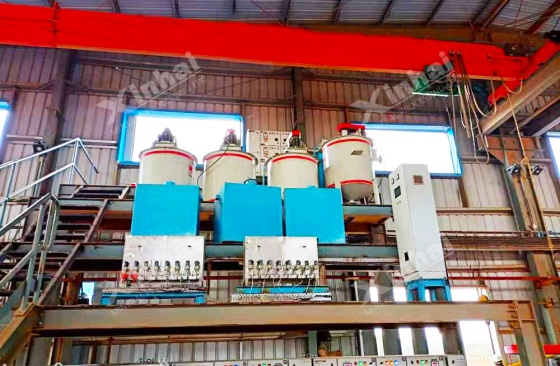
03Effect of Slurry Agitation Tank on Flotation Efficiency
Measured data from a gold concentrator show that compared with traditional
agitation tanks, Xinhai’s slurry agitation tank reduces reagent consumption by
14%, increases the bubble mineralization rate by 31%, boosts the roughing
recovery rate by 1.1%, reduces power consumption per ton of ore by 17%, and
improves the overall recovery rate by 1%.
04Application Cases of Xinhai Slurry Agitation Tank
1.Tibet Spodumene Project
Due to high altitude and low-pressure conditions, slurry concentration
fluctuates significantly, causing frequent sedimentation in traditional
agitation tanks. As a result, lithium recovery remained below 82%. After
replacing with Xinhai’s slurry agitation tank, reagent dispersion became
uniform, stabilizing the recovery rate at over 87.5%.
2.Chilean Copper Mine Project
The high-density slurry previously led to more than 5% sedimentation within
48 hours using traditional tanks. After switching to Xinhai’s slurry agitation
tank, no visible sedimentation occurred during continuous operation. The copper
recovery rate improved by 1.3%, and annual electrolytic copper output rose by
800 tons.
Conclusion
Xinhai’s high-efficiency agitator tank improves both mixing and flotation
efficiency through a technical approach of structural innovation → flow field
optimization → performance quantification.
When a 1% increase in recovery rate translates to billions of yuan in
revenue, the slurry agitator tank is no longer just an optional “auxiliary
device”—it becomes a critical component determining a mine’s profitability.