The quartz gravity–magnetic separation combined process is a widely applied
and effective method in quartz ore beneficiation. By leveraging the differences
in mineral density and magnetic susceptibility, this process efficiently
separates quartz from heavy mineral impurities and iron-bearing minerals. It is
especially suitable for removing high-density gangue minerals and magnetic
contaminants such as magnetite, hematite, titanium minerals, mica, and
chlorite.
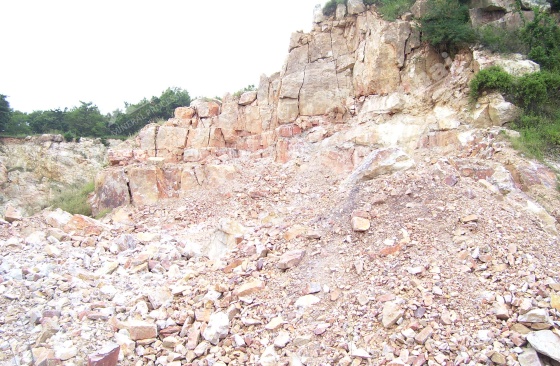
After treatment with the gravity–magnetic separation combined process, the
SiO₂ content of quartz ore can reach 98% to 99.2%, making it suitable for
various applications, including high-white glass, fine ceramics, chemical
silicon raw materials, casting, refractory materials, and mid-range electronic
components.
This article serves as a process distribution guide, introducing the quartz
gravity–magnetic separation combined process. The main steps are as follows:
Use the table of contents below to navigate through the guide:
01Quartz Grinding and Classification
1. Process Flow
Ore bin buffering → Belt conveyor feeding → Vibrating screen pre-screening →
Ball mill grinding → Slurry pump conveying → Desliming bucket desliming →
Hindered settler classification → Vibrating screen classification → Ball mill
regrinding
2. Analysis of Key Steps
Pre-screening and particle size control:
The raw ore is screened by a vibrating screen. The coarse particles retained
on the screen are sent to the ball mill for grinding, while the fine particles
passing through the screen enter the pump box directly, reducing the energy
consumption of the mill.
Two-stage closed-circuit grinding design:
The first-stage grinding product is classified by a hindered settler. The
underflow (coarse particles) returns to the ball mill for regrinding, forming a
closed-circuit loop to ensure the final particle size meets the required
standard.
Efficient desliming in the desliming bucket:
Fine clay particles in the grinding product are removed by the desliming
bucket, preventing blockage in subsequent equipment.
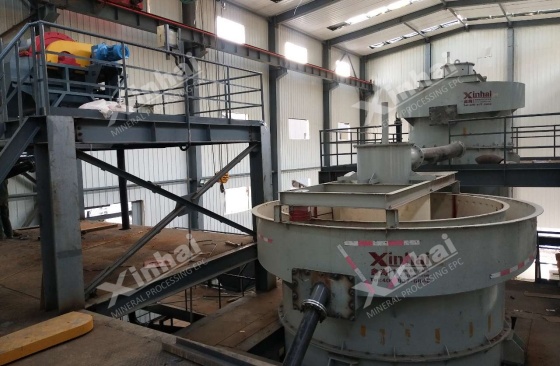
02Quartz Gravity Separation and Magnetic Separation
1. Process Flow
Hindered settler separation → Slurry pump conveying → Wet drum magnetic
separator (low-intensity) → Vertical ring high-gradient magnetic separator
(high-intensity) → Desliming bucket → Scrubbing machine → Secondary
desliming
2. Analysis of Key Steps
Magnetic Separation Process:
Low-intensity magnetic separation (magnetic field intensity: 0.3–0.5 T) is
used to remove strongly magnetic impurities such as hematite and magnetite.
High-intensity magnetic separation (magnetic field intensity: 1.2–1.5 T)
targets weakly magnetic minerals such as mica and garnet.
Enhanced Liberation with Scrubbing Machine:
A high-efficiency agitator washer is used to mechanically
remove iron-bearing films from the quartz surface. A small amount of NaOH (pH =
9–10) can be added to enhance the scrubbing effect, increasing the SiO₂ recovery
rate to as much as 92%.
Secondary Desliming:
Following magnetic separation, the slurry undergoes secondary desliming in a
desliming bucket to ensure the cleanliness of the feed for the subsequent
gravity separation stage.
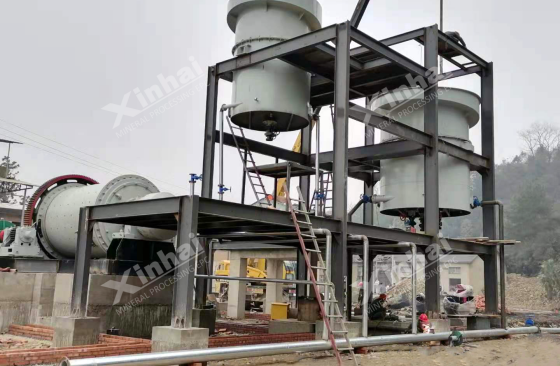
03Quartz Classification and Dewatering
1. Process Flow
Coarse Particle Concentration:
Hindered settler underflow → Slurry pump → Desliming bucket → Dewatering
screen → Belt conveyor → 40–70 mesh concentrate storage
Fine Particle Concentration:
Hindered settler overflow → Desliming bucket → Belt filter → Belt conveyor →
70–140 mesh concentrate storage
2. Analysis of Key Steps
Dual-Stage Dewatering Design:
A combination of desliming buckets and dewatering screens or belt filters
(final moisture ≤8%) balances efficiency and operational cost.
Graded Product Storage by Particle Size:
The 40–70 mesh concentrate is used for photovoltaic glass substrates, while
the 70–140 mesh concentrate is supplied for electronic-grade silica
powder—enabling value-added product differentiation.
Water Recycling System:
Water recovered during the dewatering process is treated in a sedimentation
tank (with PAC flocculant added). Once the suspended solids (SS) level is
reduced to ≤50 mg/L, the water is pumped back into the grinding system,
resulting in a water-saving rate of over 85%.
04Quartz Tailings Dewatering
1. Process Flow
Tailings thickener → Slurry pump → Filter press → Belt conveyor → Tailings
storage
2. Key Step Analysis
High-Efficiency Thickening Technology:
A deep-cone thickener, equipped with an automatic dosing system, achieves
underflow concentrations of 45%–50%.
High-Pressure Filtration and Dewatering:
A membrane filter press reduces the moisture content of the filter cake to
≤18%, making it suitable for direct use in brick-making or as roadbed
filler.
Zero-Discharge Design:
Overflow from the thickener and filtrate from the press are reused after pH
adjustment (neutralized to 6.5–7.5), achieving zero wastewater discharge.
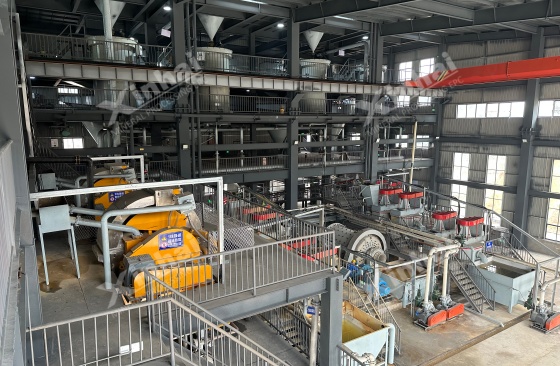
05Advantages of the Gravity-Magnetic Combined Process
1. Low Investment Cost
Power Consumption:
The gravity-magnetic combined process relies mainly on physical separation.
Energy use is concentrated in grinding and magnetic separation, resulting in
lower electricity costs.
Reagent Use:
Only a small amount of NaOH is required in the scrubbing stage, significantly
reducing reagent costs compared to the quartz flotation method.
Equipment Maintenance:
Gravity and magnetic separation equipment features simple structures. Devices
like spiral chutes are highly wear-resistant, which helps minimize maintenance
expenses.
Tailings Treatment:
Because no chemical reagents are used, tailings treatment is more
cost-effective.
2. Pollution-Free and Environmentally Friendly
This process removes impurities solely through differences in density and
magnetism—without the use of collectors, depressants, or regulators typically
required in flotation—eliminating the risk of chemical contamination.
Process water remains neutral and can be reused or discharged after meeting
environmental standards. Furthermore, its carbon footprint is much lower than
that of flotation-based methods, making it more sustainable.
Conclusion
This is a process distribution guide for quartz beneficiation using the
gravity-magnetic combined method. While this approach offers advantages such as
low cost and environmental friendliness, the resulting quartz purity may not
meet the stringent requirements of photovoltaic glass or semiconductor
applications. For higher purity, additional processes such as flotation and acid
leaching are required.
Xinhai Mining has rich experience in quartz processing and has successfully
delivered dozens of quartz beneficiation projects. With an independent R&D
team and seasoned mineral processing experts, we are ready to provide customized
solutions for your quartz beneficiation needs.