Apatite is an important phosphate mineral and the main source of phosphorus.
It has a wide range of uses, including the production of phosphate fertilizers,
phosphoric acid, and detergents, as well as the manufacturing of cathode
materials for lithium iron phosphate batteries. Apatite flotation is the primary
method for phosphorus extraction, but it currently faces challenges such as fine
particle distribution, complex associated minerals, and increasingly stringent
environmental regulations. As a supplier of mineral processing technology and
equipment, Xinhai Mining is committed to providing efficient and environmentally
friendly apatite flotation solutions.
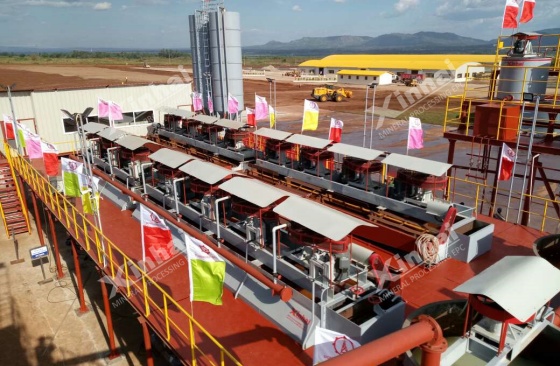
Use the table of contents below to navigate through the guide:
01Apatite mineral composition
Apatite belongs to the hexagonal crystal system and is commonly found in
columnar, plate-like, or granular aggregates, with a Mohs hardness of 5. Pure
apatite is colorless and transparent, while the presence of impurities can give
it green, blue, yellow, purple, or other colors.
Apatite often coexists with gangue minerals such as quartz, calcite,
dolomite, and mica. Sedimentary apatite is typically associated with clay, while
igneous rock types often contain magnetite and ilmenite. Some apatite deposits
also contain rare earth elements and have comprehensive recycling value.
02Apatite flotation process
Apatite flotation adopts the typical roughing–scavenging–cleaning process.
The specific steps are as follows:
1. Raw Ore Preparation
After mining, apatite is crushed to less than 10 mm through coarse, medium,
and fine crushing. Then, a ball mill is used for grinding. Based on the particle
size of apatite, the ore is ground to -200 mesh, with 60%–80% passing. During
grinding, a spiral classifier or hydrocyclone is used to control grinding
fineness and avoid over-grinding.
2. Desliming Pretreatment
Excessive slime may be produced during grinding, which can interfere with
flotation by increasing reagent consumption or coating the mineral surface.
Therefore, desliming pretreatment can be added if necessary. Desliming can be
achieved by removing overflow from the classifier or by using a cyclone.
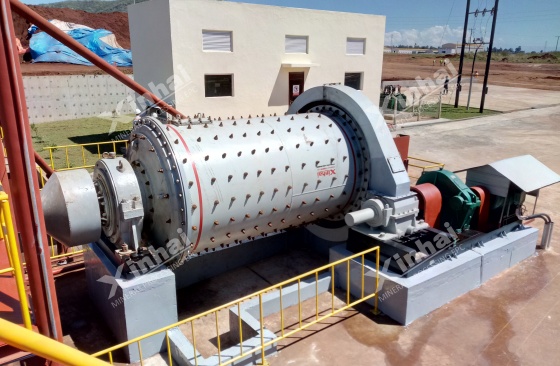
3. Roughing
Two methods are commonly used in the roughing stage: direct (positive)
flotation and reverse flotation.
Positive flotation involves directly floating apatite, leaving gangue in the
tank. It is suitable for separating gangue minerals such as quartz and
feldspar.
Reagent system: Sodium carbonate is used as a pH regulator to activate
apatite, water glass as a depressant for silicates, and fatty acids (e.g., oleic
acid, oxidized paraffin soap) or sulfates as collectors.
Reverse flotation involves floating gangue while apatite remains in the tank.
It is suitable for separating gangue minerals such as calcite and dolomite.
Reagent system: Sulfuric acid is used to depress apatite, while phosphates or
sulfonated succinic acid serve as collectors.
4. Scavenging and Cleaning
Scavenging recovers residual apatite from roughing tailings to improve
recovery.
Cleaning refloats the roughing concentrate (1–3 stages) to remove entrained
gangue and improve concentrate grade.
5. Concentration and Filtration
In the concentration stage, a efficiency thickener is used to reduce the
concentrate’s moisture content. The underflow concentration can reach 60%–70%.
In the filtration stage, a vacuum filter or filter press is used for dewatering,
and the moisture content of the filter cake is controlled below 12%.
6. Tailings Dewatering
Apatite tailings must be dry stacked. After dewatering, they can
be used for goaf backfilling. Flotation wastewater can be recycled after
sedimentation and neutralization to reduce water consumption.
03Apatite flotation technology innovation
1. Innovation in Flotation Reagents
The reagent system is the core of apatite flotation and directly affects the
separation efficiency. Traditional oleic acid collectors have issues such as
poor selectivity, low adaptability at low temperatures, and environmental
pollution.
Today, modified fatty acid collectors and amphoteric collectors are
increasingly used in apatite flotation. Compared with traditional collectors,
these new reagents improve flotation performance at low temperatures and are
more environmentally friendly. Amphoteric collectors also enhance adaptability
to complex ores.
The use of inhibitors has evolved from single inhibitors to composite
inhibitors, which offer stronger and more selective suppression effects.
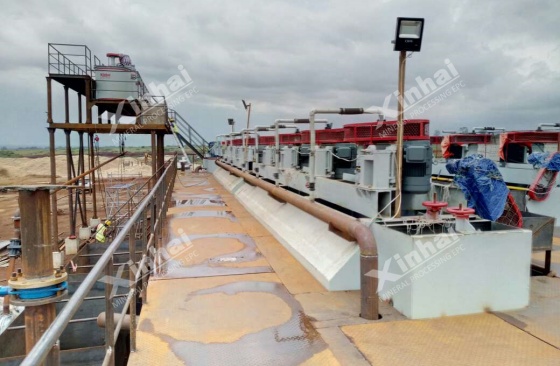
2. Improvement in Flotation Equipment
Flotation equipment is now equipped with microbubble generators to increase
the collision probability between apatite particles and bubbles.
Self-priming flotation machines are used, eliminating the need for external
air supply and reducing energy consumption by 15%–20%.
The agitation system uses a stepped impeller design to shear the pulp in
layers, preventing sedimentation of coarse particles and ensuring uniform bubble
distribution.
Adjustable stator–rotor gaps allow for adaptation to ores of different
particle sizes and help reduce the loss of over-ground particles.
All flotation equipment is equipped with intelligent control systems,
enabling real-time monitoring of foam color and size, automatic regulation of
air flow and reagent dosing. Online grade analyzers are used for rapid ore grade
detection and closed-loop control of flotation parameters.
3. Process Innovation
Traditional apatite beneficiation processes use single-stage fine grinding,
which may lead to over-grinding and generate excessive ore slime that negatively
affects flotation.
The innovative process adopts stage grinding and stage separation, which
reduces grinding energy consumption by 20% and decreases ore slime generation by
50%.
In addition to standalone flotation, the process can be combined with
magnetic separation for iron removal and gravity separation for pre-enrichment
before flotation, resulting in improved separation performance.
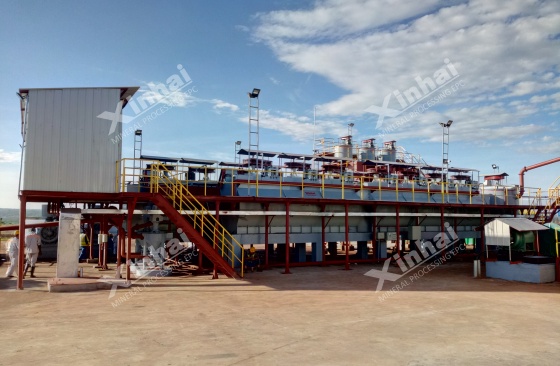
04Xinhai Solution
The apatite EPC+M+O project undertaken by Xinhai Mining involved raw ore with
a P₂O₅ grade of 12%. Due to the high slime content, the recovery rate of the
traditional process was less than 70%. After conducting detailed mineral
processing tests, Xinhai adopted a desliming + two-stage reverse flotation
process. As a result, the concentrate grade was increased to 32%, and the
recovery rate reached 85%.
Looking ahead, apatite flotation technology is expected to evolve toward
intelligent control, environmental sustainability, and comprehensive resource
utilization. Xinhai Mining remains committed to providing customers with
scientific and efficient mineral processing solutions, driving the sustainable
and efficient development of phosphorus resources through innovative processes
and reliable equipment.