In general, the main mineral of natural silica sand and quartz sandstone is quartz, and some other impurity minerals are often associated with it, such as mica minerals, feldspar minerals and iron and aluminum oxide minerals. However, the mixing of these impurities greatly reduces the value of quartz sand and affects the quality of products. Therefore, it is necessary to carry out the impurity removal for the silica sand. Here are the silica sand purifying process and equipment for the silica sand processing plant.
Use the table of contents below to navigate through the guide:
01Process and equipment used for the impurity resolution of silica sand
The impurity resolution process of silica sand means to adopt the crushing, grinding and classifying to break the natural quartz sandstone ore and make the impurities and minerals reach the state of monomer dissociation, and then use the classifying operation to obtain the raw silica sand meeting the requirements of grain size, so as to prepare for the subsequent impurity resolution of silica sand.
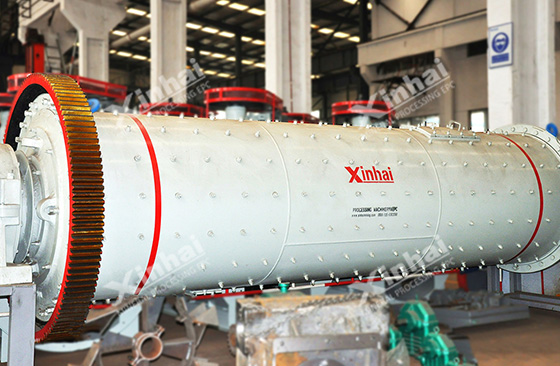
Here is the detailed process:
Adopting the jaw crusher to break the natural quartz sandstone ore into small pieces, and then using the grinding mill to grind the small pieces of quartz ore into finer silica sand through the wet grinding way. The wet grinding process can not only eliminate the dust generated in the grinding process, but also make the particles of silica sand rub against each other, and prompt the impurities attached to the surface of silica sand (such as iron oxide and hydroxide) to dissociate from the silica sand particles. Subsequently, the grinding products enter into the classification operation, the silica sand meeting the particle size requirements can be used as raw silica sand to carry out the impurity removal of silica sand, the coarse grains are returned to grinding mill for re-grinding.
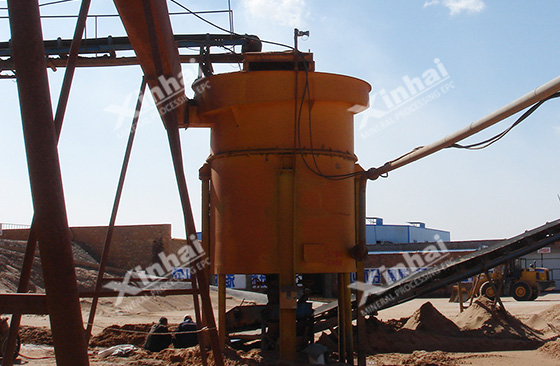
02Process and equipment used for the impurity removal of silica sand
The impurity removal process of silica sand is to remove the mineral impurities from the raw silica sand by scrubbing and desliming, magnetic separation, chute gravity separation, flotation, pickling or several combined methods, so as to obtain the high-purity silica sand with required particle size and impurity content.
1. Scrubbing and desliming method
Adopting the mechanical force of the washing machine and the grinding force among the sand particles to remove the thin film iron outside the silica sand, the binding and muddy impurity mineral deposits.
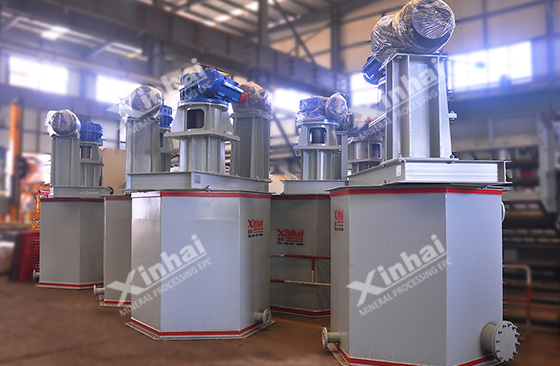
2. Magnetic separation method
Magnetic separation method is one of the effective methods to remove iron impurities from raw materials. The hematite, limonite, biotite and other minerals contained in the raw materials are weakly magnetic, which can be selected by the wet type strong magnetic separator with the magnetic field strength of 8×105A/m. and using the weak magnetic separator or the medium magnetic separator can be used when the raw material contains the strong magnetic mineral (such as magnetite). In order to further remove other small amounts of weakly magnetic minerals (such as amphibole, pyroxene and the continuous growth of magnetic minerals and quartz), a high gradient magnetic separator with a magnetic field strength greater than 12,000 Gauss can be used for secondary magnetic separation.
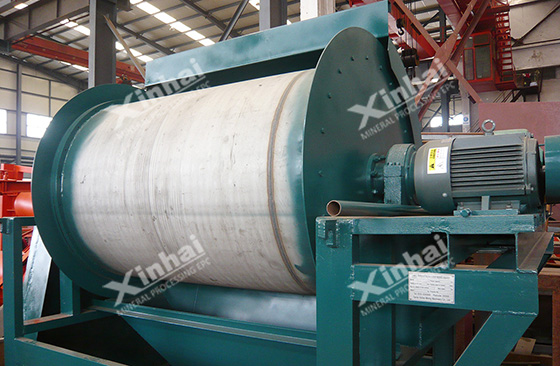
3. Chute gravity separation method
When the raw material contains a very small amount of heavy mineral impurities (such as zircon), the spiral chute gravity separation method can be used to effectively remove such heavy mineral impurities because they don't have the magnetism and has a greater weight than silica sand.
When the raw mortar rotates along the spiral chute surface, the various minerals will be separated according to their respective specific gravity. Under the dual action of gravity and centrifugal force, the greater the difference in mineral specific gravity, the higher the separation degree will be. It is worth noting that the mineral morphology also has a certain influence on the separation of spiral chute. The flake minerals are easy to be separated from the granular minerals. Therefore, the separation of quartz mortar body can be divided into three parts when the spiral chute is used to separate the silica sand slurry: granular heavy mineral area, granular silica sand area, flaky and light mineral area, which can not only remove the heavy mineral in the silica sand, but also remove some sheets mica minerals.
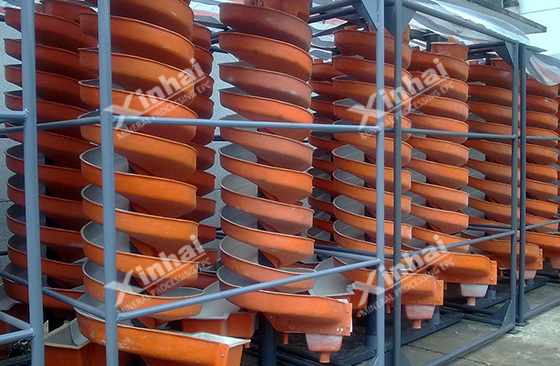
4. Flotation method
If there are many mica minerals in the raw materials, it is impossible to completely remove the impurities only by using the spiral chute. In addition, if the raw material also contains a certain proportion of feldspar minerals who has a similar specific gravity to silica sand, the flotation process can be used to remove these impurities minerals. At the same time, it is necessary to increase the grinding fineness when the silica sand and gangue minerals do not reach a certain degree of monomer dissociation.
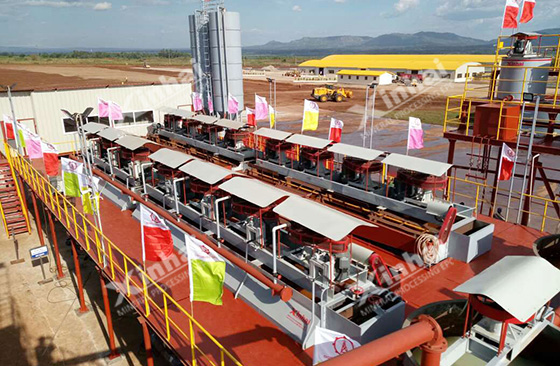
Here is the flotation process:
Adopting the three-stage flotation process to remove the mica and feldspar minerals from silica sand respectively. In the first stage flotation, the iron-containing argillite is extracted from the slurry by the corresponding flotation reagent system under a neutral or weak acid environment. In the secondary flotation, the mica minerals and their symbionts with silica sand are extracted from the slurry by the corresponding flotation reagent system under neutral or weak acid conditions. In the third stage flotation, the feldspar minerals and their symbionts with silica sand from slurry by the corresponding flotation reagent system under neutral or weak acid environment.
5. Pickling method
The pickling method can be adopted if the color of the finished sand or the product sand after the separation operation is red and the high content of iron and titanium does not meet the quality requirements of the product.
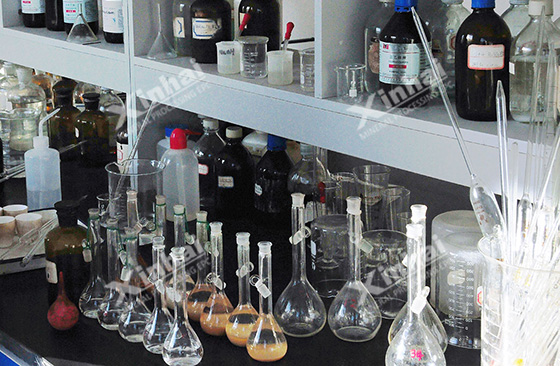
The above are process and the equipment used in the impurity removal of silica sand. Carrying out the impurity removal when the impurity mineral and silica sand reach the state of monomer dissociation can remove almost all the impurity mineral in the raw material, and greatly improve the purity of silica sand, so as to obtain the corresponding silica sand concentrate.