With the development of the iron and steel industry, the development of ferrochromium resources is increasingly intensified. In order to make better use of chromite resources, it is particularly important to choose a suitable beneficiation process. Chromite has the characteristics of high specific gravity and weak magnetic properties. Concentrators can choose gravity separation method and magnetic separation method for chromite mineral processing according to this characteristic. The following will focus on these two chromite mineral beneficiation processes.
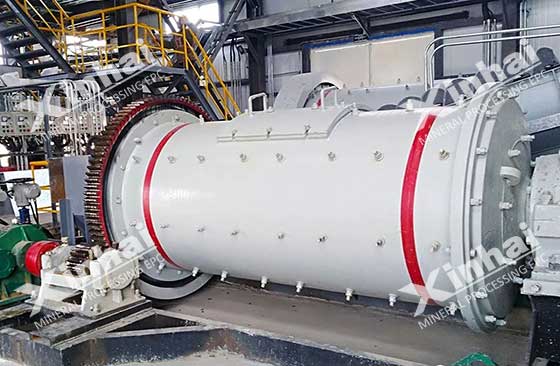
Use the table of contents below to navigate through the guide:
01Chromite gravity beneficiation process
The gravity separation process of chromite can be divided into three types: full-grain shaker separation, spiral chute tailing-shaker separation, and desliming tailing-shaker separation.
1. Full-grain shaker beneficiation process
The chromite raw ore is crushed and screened into the ball mill for grinding, and then directly enters the shaker for separating after grinding to the required particle size of the shaker. In order to ensure the efficient progress of the shaking table gravity separation process, it is very important to grasp the grinding particle size of the ore. Too coarse or too fine ore particle size will affect the recovery of its concentrate. Therefore, before the beneficiation, the beneficiation plant needs to conduct a beneficiation test analysis to determine the grinding particle size of the chromite. Shaking table beneficiation of full-grain chromite is generally divided into two stages: primary beneficiation and secondary beneficiation. In order to obtain high-grade chromite concentrate, the width of the concentrate belt can be reduced during the first stage of the shaking table process. In this way, after the shaker, a concentrate with substantially no impurities and a medium ore containing some impurities can be obtained. This beneficiation process has the advantage of high beneficiation precision.
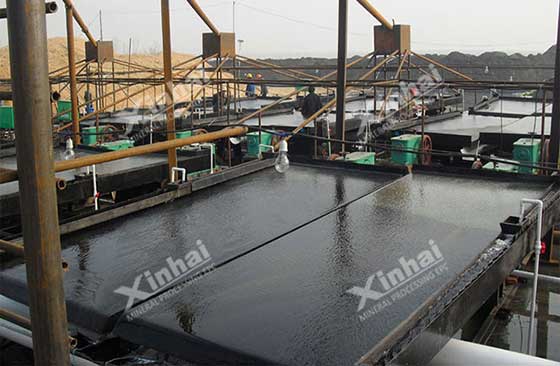
2. Spiral chute tail throwing-shaker beneficiation process
If the production site of the concentrator is limited, the spiral chute tailing-shaking process can be considered to treat chromite. The specific process is as follows: the raw ore is ground to the required particle size by a ball mill and then enters the spiral chute for sorting. After sorting, the qualified tailings are thrown away, and the rest of the ore enters the shaker for beneficiation again. The purpose of the spiral chute for tail throwing is to reduce the processing capacity of the shaker, and at the same time, it can also reduce the artificial interference to the gangue and improve the working efficiency of the shaker. The ore after the tailing of the spiral chute will go through two stages of shaking table and middle ore beneficiation. Spiral chute is one of the advantageous equipment for gravity separation, which has a large processing capacity and does not require power.
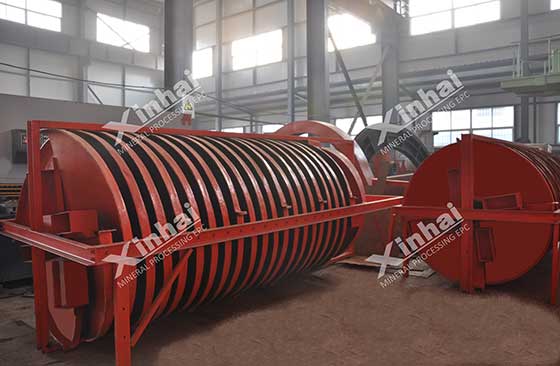
3. Desliming and tailing - shaker beneficiation process
Because the chromite ore will produce some fine mud after grinding, because the shaking table has low sorting efficiency for the fine mud, it will affect the recovery of high-grade concentrate. Therefore, in this method, the ore desliming process is added before the shaker classification. The main process flow is as follows: raw ore enters the ball mill for grinding, and ore with qualified particle size enters the desliming bucket for desliming treatment. Then the coarse concentrate after desliming is subjected to shaking table classification and medium ore re-selection. After the ore is deslimed, the zoning of various ore products is obvious when the shaker is used for sorting, which is conducive to the control of sorting indicators.
The above is the gravity separation process of three kinds of chromite. Before the concentrator decides to use the gravity separation process to process the chromite, it should conduct ore composition analysis and beneficiation test analysis of its own ore, so as to determine the appropriate beneficiation process.
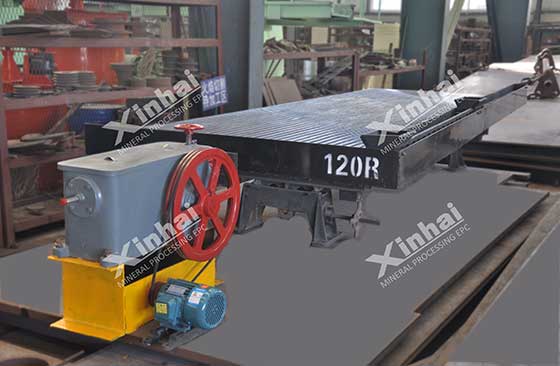
02Chromite magnetic separation method beneficiation process
Because chromite has a high magnetic susceptibility, it can be sorted by magnetic separation. The magnetic separation method can be divided into two processes: strong magnetic tail throwing-shaker separation and full-intensity magnetic separation.
1. Strong magnetic tail throwing-shaker sorting process
In this process, a strong magnetic separator is used as the first stage of separation to enrich most of the concentrate and discard the tailings. The first-stage magnetic separation concentrate enters the shaker for sorting. The purpose of this is to improve the grade of the concentrate selected by the shaker. In order to avoid waste of resources, the medium ore in the shaker gravity separation needs to be re-selected. The grinding process before the strong magnetic separation should also be noted that the ore particle size will affect the subsequent beneficiation process, so the properties of the ore need to be determined before the process design to select the appropriate grinding particle size.
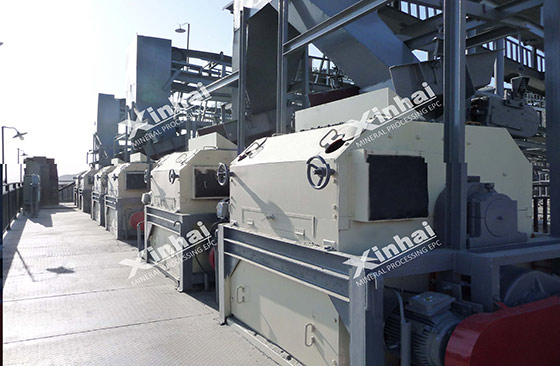
2. Full-strength magnetic separation and sorting process
When magnetic separation is used to treat chromite, a higher recovery rate can be obtained, but the concentrate obtained by the first-stage magnetic separation has a lower grade. In order to improve the grade of the recovered concentrate, the concentrator can use one stage of strong magnetic roughing and one stage of strong magnetic selection. The specific process is as follows: the chromite ore is ground to a qualified particle size and then enters into a strong magnetic separator for a rough separation. The rougher concentrate enters the second-stage magnetic separator for selection. This technological process is simple and easy to operate, reliable in operation and stable in indicators.
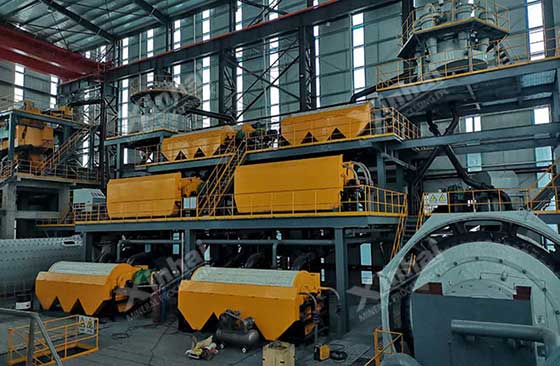
The above content is the gravity separation and magnetic separation for chromite mineral processing. Xinhai Mining recommends to conduct ore selectivity analysis and beneficiation test analysis during process design of the ore dressing plant. Based on the results of the test analysis, we can formulate a suitable beneficiation process for you. Xinhai Mining has more than 20 years of experience in beneficiation process design and equipment manufacturing, and can customize chromite beneficiation process and beneficiation equipment for you. If necessary, welcome to consult.