As an important non-metallic mineral raw material, barite is widely used in industrial production. It can be used as drilling mud weighting agent, zinc white pigment and various barium compounds. With continuous mining, high-quality single barite ore is decreasing day by day. Due to the close association of other metal ores and non-metal ores, its industrial value will be affected. Therefore, the use of reasonable beneficiation technology to select high-grade barite concentrate is one of the solutions to this situation. The beneficiation methods of barite generally include: manual selection, gravity separation, flotation and magnetic separation. This article will introduce the process flow of barite gravity separation method in detail.
The gravity separation process of barite can be divided into five parts, namely crushing operation, screening operation, buffer operation, gravity separation operation and dehydration operation.
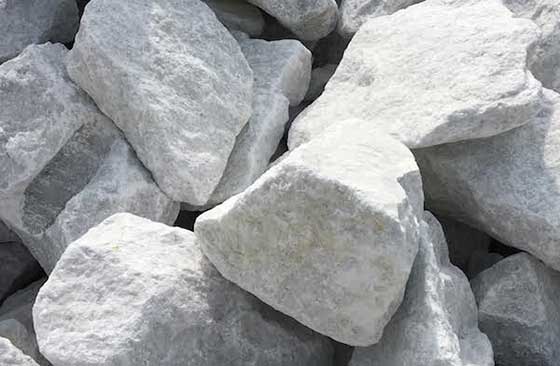
Use the table of contents below to navigate through the guide:
01Crushing process of barite
Because barite is brittle and fragile, jaw crusher is mainly used when barite is crushed. In order to make the crushed barite meet the particle size range required by entering the jig machine, two-stage crushing is generally used. The barite raw ore enters the jaw crusher through the feeder for one-stage crushing. After crushing, the products are transported to the second-stage jaw crusher by belt conveyor for fine crushing. In the crushing operation, dust is usually generated. In order to reduce the impact of dust on the overall working environment, it is recommended to add appropriate water to the crushing process to reduce the dust generated when the crusher is working.
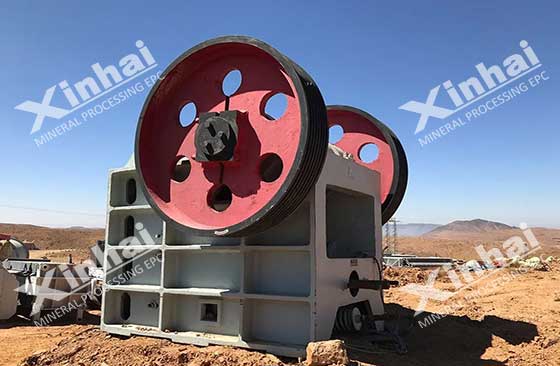
02Screening process of barite
The barite gravity separation generally adopts the jig machine. Due to its strict requirements on the particle size of the incoming materials, it is required to classify and classify to improve the processing capacity and the beneficiation index. Therefore, the screening operation of the crushed product is carried out before the barite re-selection. After screening, the products are divided into different grades and enter the jigger for gravity. When screening, the concentrator can use a circular vibrating screen. This equipment has the advantages of easy operation, high efficiency and large processing capacity, and is an ideal equipment for barite screening operations.
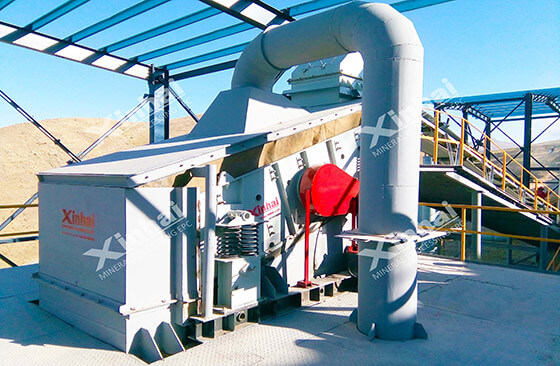
03Buffering process of barite
In order to ensure the normal operation of the jig, it is necessary to ensure a uniform and stable feeding amount when feeding ore. Therefore, it is necessary to set the buffer part before the product enters the jig after screening. Concentrators can choose silo or vibrating feeder. When using the buffer silo, make sure that some materials are pre-stored in the silo to avoid the situation that the amount of feeding is fluctuating at the beginning of work. The vibrating feeder can ensure that the materials can enter the jig uniformly and stably for gravity separation.
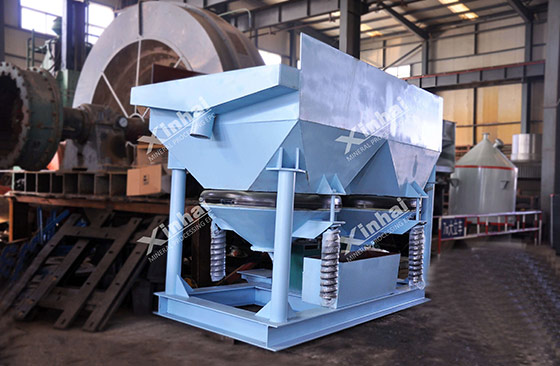
04Gravity separation process of barite
The separation of barite by jig is mainly based on the specific gravity difference between barite and other associated gangue minerals. The barite enters the jig machine through the silo or vibrating feeder, and undergoes density stratification under the action of the alternating water flow generated by the equipment agitating the water flow. Due to the large specific gravity of barite and the fast settling speed, it will enter the lower layer of the sorting tank. Gangue minerals with low specific gravity will occupy the upper part of the sorting tank. The sorted barite and gangue minerals will be removed from the machine through the ore discharge device, and the barite concentrate and tailings can be obtained.
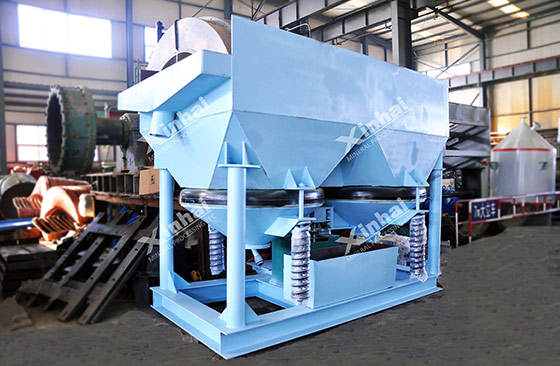
05Dehydration process of barite
Because a large amount of water is used in the jig gravity separation process, the resulting barite concentrate has a high moisture content and needs to be dewatered. Concentrators can choose different dehydration processes according to their needs, such as mechanical dehydration, concentration tank dehydration, dryer dehydration, etc. Without avoiding the waste of water resources, the concentrator can also set up a water circulation system as needed, which can not only ensure the smooth progress of the technological process, but also make full use of resources and avoid waste of resources.
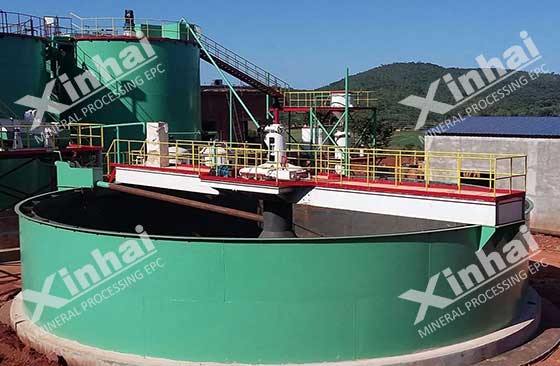
The above content is the barite gravity separation process. Due to the different compositions and characteristics of different types of barite, the concentrator needs to select the process according to the actual situation. Xinhai Mining recommends the beneficiation plant to conduct ore beneficiation test before process design, and then formulate a reasonable beneficiation process. Xinhai Mining, as the proposer and practitioner of "Mining Whole Industry Chain Service (EPC+M+O)", can customize barite beneficiation plan and complete equipment for you. If necessary, welcome to consult Xinhai Mining.