Chromium is a transition metal widely used in various industries, and chrome mineral is the main source of chromium metal. Chrome ore usually occurs as dark, shiny and brittle crystals. The mining and processing of chrome ore involves various beneficiation techniques to separate chromite from associated gangue minerals. The extracted chromite is processed through crushing, grinding and gravity or magnetic separation to obtain a concentrate rich in chromite minerals, which can be further processed into ferrochrome alloys or other chromium products.
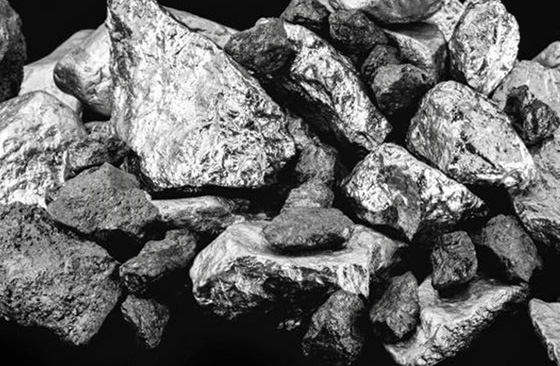
In chrome ore processing, a commonly used technology is gravity separation. Gravity separation is widely used in the processing of chromium ore due to its simplicity, economy and ability to efficiently separate chromite from gangue minerals based on the density of the mineral. The following will introduce you to the gravity separation technology of chrome minerals.
Use the table of contents below to navigate through the guide:
01Introduction To Gravity Separation Technology Of Chrome Mineral
In the DMS process, crushed mineral chrome is mixed with a density medium, usually a suspension of ferrosilicon or magnetite in water. The density of the density medium is between that of chromite and gangue minerals. When the ore is acted upon by gravity, the denser chromite particles sink to the bottom, while the less dense gangue minerals float to the top. In this way, the separation of chromite and gangue minerals is achieved.
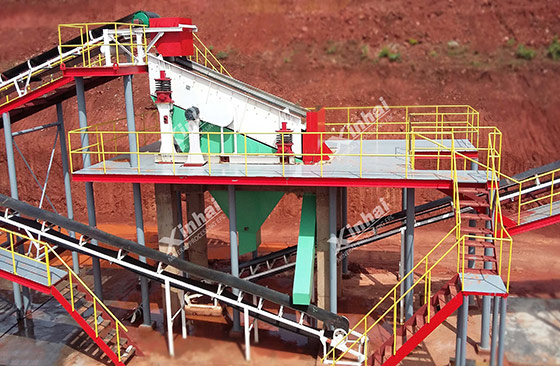
02Chrome Mineral Gravity Separation Process
The broad range of chrome mineral uses drives demand for efficient separation technologies. The chromium ore density media separation (DMS) process is a commonly used chromium ore processing method that uses the density differences of different minerals to separate chromite and gangue minerals. The following are the basic steps of the chromium ore density media separation (DMS) process:
1. Ore crushing and pretreatment: Chromium ore undergoes crushing, grinding and screening steps to reach appropriate particle size for subsequent processing. Typically, larger ores are broken into smaller particles. Commonly used equipment in this process include jaw crushers, cone crushers and impact crushers. Vibrating screens or drum screens are used to screen the crushed ore, and rod mills or ball mills are used to grind the ore.
2. Density medium preparation: Prepare a density medium, usually using a suspension. In chromium ore processing, the commonly used density media are suspensions of ferrosilicon or magnetite. The density of the density medium is generally between that of chromite and gangue minerals.
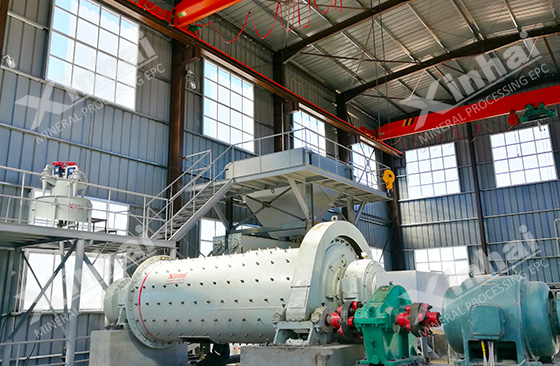
3. Density separation: Mix the crushed chrome ore with density medium. Under the action of the density medium, the denser chromite ore particles will sink to the bottom of the medium, while the less dense gangue mineral particles will float on the upper layer of the medium. In this way, the separation of chromite ore and gangue minerals is achieved. Density Media Separation (DMS) cartridges can be used to handle this process. The DMS cartridge is the core component of the density media separation process. It is a rotating cylinder filled with density medium suspension, such as iron silicon or magnetite in water. The crushed chromium ore is introduced into the DMS barrel where it is separated based on the density difference between the valuable chromite minerals and the gangue minerals.
4. Density grading: By controlling the concentration and flow rate of the density medium, further grading of chromite and gangue minerals can be achieved. Particles with different densities are deposited in different locations, further improving separation. This process can use a cyclone to separate the density medium from the chromite mineral-rich particles after the chromite particles are deposited at the bottom of the DMS cylinder. The cyclone uses centrifugal force to separate the density medium from the chromite concentrate so that the medium can be recycled and reused in the DMS process.
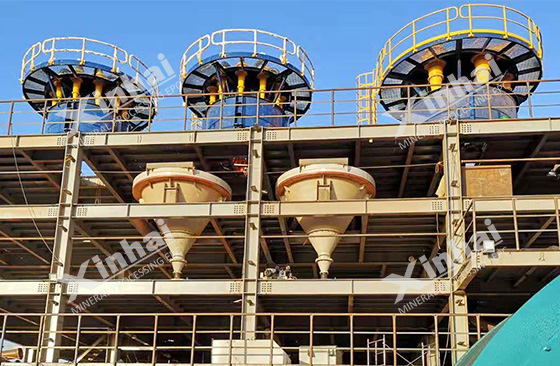
5. Concentrate recovery: During the density separation process, the denser chromite ore particles are deposited at the bottom to form concentrate, and the smaller density gangue mineral particles float on the upper layer to form tailings. By collecting and extracting the concentrate, a concentrated product rich in chromite minerals can be obtained. A sedimentation tank or thickener can be used to separate the density medium from the gangue minerals and concentrate the chromite-rich particles. These tanks use gravity settling or sedimentation to separate and collect the desired chrome concentrate.
The above content is the gravity separation technology of chrome mineral, which can effectively separate chromite and gangue minerals to obtain high-grade chromite mineral concentrate. This process has simple operation, low cost and high separation efficiency, and is widely used in the processing of chromium ore.
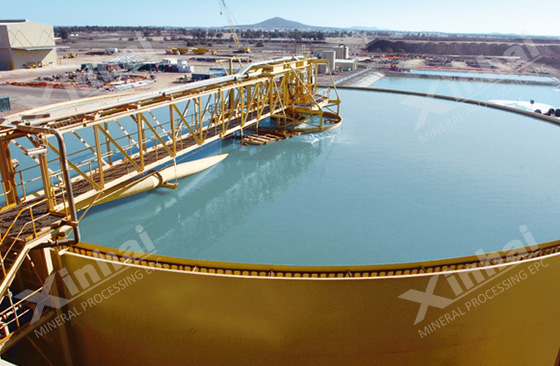
In actual production, gravity separation technology may be combined with other mineral processing technologies, such as magnetic separation or flotation. The specific beneficiation technology should be based on the different surface properties of chromite and gangue minerals, the characteristics of the ore deposit, the desired concentration grade, and the specific requirements for downstream processing. Different processing plants may employ different technologies or combinations of technologies to optimize chromite recovery and achieve the desired product quality.