Fluorite is an important non-metallic strategic resource, widely used in defense, chemical industry, metallurgy, optics and other fields. China is rich in fluorite resources and reserves, but most of them are poor ores with complex composition and great difficulty in beneficiation. Fluorite ores are divided into two types: single type and associated type: single type fluorite ores have simple mineral combination, high grade and relatively simple beneficiation process, while associated type fluorite ores are mostly skarn type. According to different gangue minerals, fluorite ores are divided into quartz-fluorite type, calcite-fluorite type, sulfide-fluorite type and barite-fluorite type. At present, fluorite ore beneficiation processes mainly include hand selection, gravity separation and flotation. Among them, flotation has become the main method for separating fluorite from gangue due to its advantages in processing poor ores and complex embedded ores.
Use the table of contents below to navigate through the guide:
01Flotation process of quartz-fluorite ore
Quartz-type fluorite ores are mainly composed of fluorite (content up to about 85%) and quartz, containing a small amount of gangue minerals such as calcite, barite and sulfide. The process of coarse grinding and rough selection, re-grinding of coarse concentrate and multiple selection is often adopted. In the process, sodium oxide is often used as a pH adjuster to maintain the pH of the ore pulp in the alkaline range of 8-9, fatty acids are used as collectors for fluorite, and water glass is used to inhibit quartz. Among them, the amount of water glass must be properly controlled. A small amount will activate fluorite, and an excessive amount will inhibit fluorite. In order to improve the quartz inhibition effect and reduce the amount of water glass, polyvalent metal cations such as Al³⁺, Fe²⁺, alum, aluminum sulfate, etc. are usually added. Cr³⁺ and Zn²⁺ are also often used to inhibit calcite and quartz.
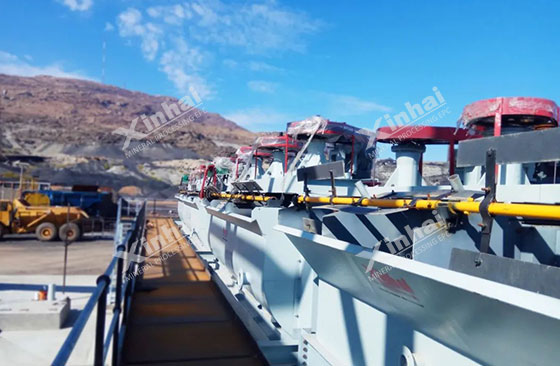
According to the distribution characteristics of the mineral, the process can be divided into two types: coarse-grained and fine-grained distribution. Coarse-grained distributed ore is easy to handle, and high-quality fluorite concentrate can usually be obtained through a one-rough-and-multiple-fine process; fine-grained distributed ore requires stage grinding and stage separation to improve the degree of monomer dissociation, thereby obtaining high-quality, low-silicon fluorite concentrate.
02Flotation process of calcite-fluorite ore
Fluorite and calcite often coexist in nature. Both are calcium salt minerals with similar surface physical and chemical properties and solubility, so separation is difficult. Since the surfaces of calcite and fluorite are easily transformed in the ore pulp, conventional fatty acid collectors have a good collection effect on both, resulting in poor flotation separation selectivity. In order to improve the separation effect, fatty acid collectors are usually emulsified, modified or used in combination. In addition, the selection of efficient inhibitors is the key, among which water glass is widely used. However, when the surface of the gangue mineral is activated by metal ions such as Ca²⁺ and Mg²⁺, the inhibitory effect of ordinary water glass will be reduced, and acidified or modified water glass is required. Its silicate ions can produce strong complexation with calcium ions, effectively squeeze out the calcite surface collector, thereby achieving separation.
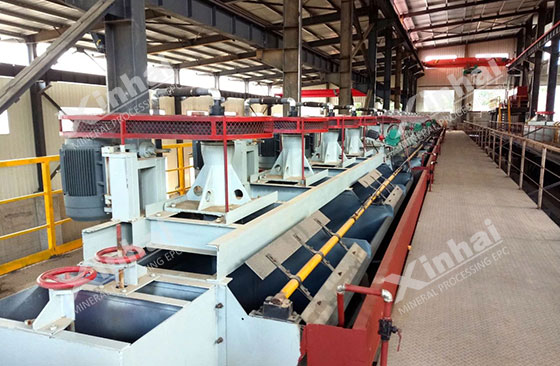
For fluorite ore containing gangue minerals such as barite and calcite, oleic acid can be added first as a collector to preferentially flotate fluorite, or aluminum salts and dextrin can be added to activate fluorite and inhibit calcite and barite. . For complex ores, such as those containing a large amount of calcite, limestone, dolomite and other gangue minerals, tannins or lignosulfonates can be used as inhibitors with better results. During flotation, the pH value of the slurry is adjusted to 8 to 9.5, and inhibitors such as water glass, acidified water glass, sodium hexametaphosphate, lignosulfonate, dextrin, and tannin are used alone or in combination to significantly improve the efficiency of flotation. Separation effect of calcite and fluorite.
03Sulfide-fluorite ore flotation process
Sulfide fluorite is associated with chalcopyrite, pyrite, galena and sphalerite. The comprehensive recovery of these metal minerals is usually considered during flotation. Due to the large difference in the surface properties of sulfide ore and fluorite, xanthate or black medicine collectors are usually added to the slurry to preferentially float the sulfide ore, and then the fluorite is floated from the tailings with fatty acid collectors. If the sulfide ore content is low and the recovery value is not high, sodium sulfide can be used directly to inhibit the sulfide ore, and then the fluorite can be directly floated with fatty acid collectors. In addition, if fluorite needs to be activated before flotation of fluorite concentrate, sodium sulfide can be added, and then fatty acid flotation can be used. At the same time, a small amount of cyanide can be added during the flotation process to inhibit the residual sulfide ore, further improving the purity of the fluorite concentrate.
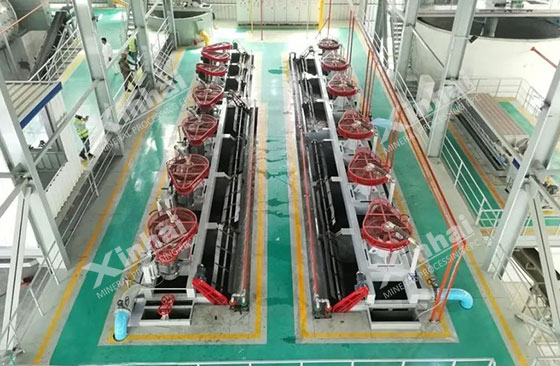
04Flotation process of barite-fluorite ore
The main minerals of barite-fluorite ore are barite and fluorite, which are often accompanied by sulfide minerals such as pyrite, galena, sphalerite, etc. Since the floatability of barite and fluorite is similar, they are usually separated by preferential mixed flotation. In the mixed flotation process, oleic acid is often used as a collector and water glass is used as an inhibitor to suppress other gangue minerals.
There are two main solutions for separation of mixed concentrates: the first is to suppress the flotation of fluorite by barite, that is, use organic inhibitors (such as dextrin, tannin, etc.) in combination with iron salts to suppress barite, and then use oleic acid as a collector to float fluorite. This method can obtain high-grade barite concentrate and fluorite concentrate, but the process is more complicated. The second is to suppress the flotation of barite by fluorite, that is, use sodium hydroxide and sodium silicate to suppress fluorite, use hydrocarbon sulfate as a collector to float barite, and then use water glass as an inhibitor and sodium oleate as a collector to float fluorite from the tailings. However, the grade or recovery rate of fluorite concentrate obtained by this method may not be high.

In fluorite ore flotation, different types of fluorite ores need to be treated differently according to their technical requirements and process flow, and blind decisions cannot be made. It is recommended to carry out mineral processing tests first to fully understand the properties of the ore, and determine the appropriate flotation process flow and reagent system based on the actual situation of the concentrator and the investment budget to ensure the efficiency and economy of the flotation process.