The function of a chrome washing plant is to process chrome ore into chrome
concentrate, and then extract chrome metal through smelting. Chromium metal is
widely used in the fields of metallurgy, electroplating, pigments and coatings,
refractory materials, etc. 70% of the world's chrome ore resources are
concentrated in South Africa. In addition, there are certain reserves in
countries such as Kazakhstan and India. The existence of chrome washing plants
is precisely to make better use of these resources.
This article introduces the process flow and equipment types of chrome
washing plants, and conducts a cost analysis of chrome washing plants through a
South African case.
Use the table of contents below to navigate through the guide:
01Chrome Washing Plant Process Flow
Do you know how a chrome washing plant works? This requires us to first
understand the properties and characteristics of chrome ore.
The color of chrome ore is black to brownish black, with a semi-metallic
luster, a hardness of 5.5~6 (Mohs hardness), and a density of 4.5~5.1g/cm³. Due
to the high density of chrome ore, most low-density impurities such as clay,
serpentine, olivine, etc. can be removed by gravity separation.
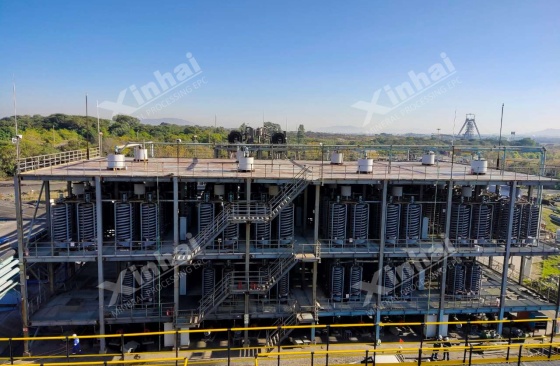
The typical process flow is as follows:
1. Crushing: Use jaw crushers, cone crushers and other
equipment to crush the raw ore to a particle size suitable for washing
(<30mm).
2. Ore washing: Use drum washers, trough scrubbers and other
equipment to remove fragile impurities such as clay and weathering layers.
3. Screening: Use vibrating screens, drum screens and other
equipment to classify chromite and separate coarse chromite from fine mud.
4. Gravity separation: Use spiral chutes, shaking tables,
jigs and other gravity separation equipment to remove low-density impurities and
enrich chromite. This step is the core link in the entire process.
5. Dehydration: Use thickener, filters and other equipment
to reduce the moisture in the concentrate, which is convenient for the
concentrate to be transported or enter the next processing link.
02Chrome Ore Washing Plant Equipment
1. Spiral Chute Washer
When the chrome ore contains a lot of mud and is seriously muddy, a spiral
chute washer should be used. The working principle is to use the different
sedimentation speeds of solid particles in the liquid to quickly remove the low
specific gravity and fine particle size ore mud.
2. Spiral chute
The spiral chute is based on the differences in specific gravity, particle
size and form between chrome ore and gangue minerals, and produces a dynamic
centrifugal flow film of slurry on the inclined surface of the spiral. In the
combined force field of gravity and centrifugal force, the gravity, hydrodynamic
pressure and friction of different particles are used to separate chrome ore and
gangue.
3. Shaking table
Combining the lateral water flow and the asymmetric reciprocating motion of
the bed surface, the mineral particles are layered and separated according to
density and particle size. The bed surface is an inclined plane covered with
riffles, forming fine grooves to promote mineral stratification. It has high
separation accuracy and plays an irreplaceable role in the chrome ore
re-selection process.
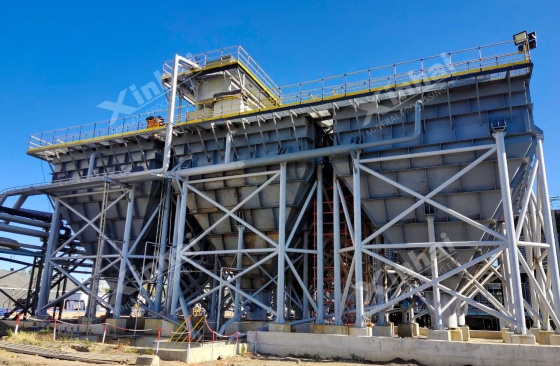
4. Jig
The pulsating water flow is used to repeatedly loosen and settle the ore
particles on the screen plate, and the ore particles are separated by density:
the chromite ore sinks to become concentrate, and the low-density minerals float
up and are discharged with the water flow. The sorting is optimized by adjusting
the water stroke, frequency and bed thickness. It is suitable for coarse and
medium-grained ores (0.5~30mm). The processing capacity is large, but the
sorting accuracy is lower than that of the shaking table.
5. Thickener
The thickener is used for dehydrating chrome concentrate. It uses the
sedimentation principle to separate the chrome concentrate from water and reduce
the water content of the chrome concentrate.
03Cost Analysis of Chromium Washing Plant
1. South Africa 300tpd chrome washing plant case
The ore grade of this project is 8.53%, and the processing capacity is
300tpd. The process flow designed by Xinhai is: two-stage one-closed circuit
crushing and screening-one-stage closed circuit grinding and
classification-gravity separation-concentrated tailings dewatering process
flow.(South Africa 3000t/d Chromite Flotation Processing Plant)
In the gravity separation stage, the hydraulic classifier is first used for
gravity separation. The selected tailings are used as the final tailings. The
middlings are scavenged, and the concentrate flows into the shaking table for
selection to obtain the final concentrate. The tailings in the shaking table are
returned to the ball mill for re-grinding.
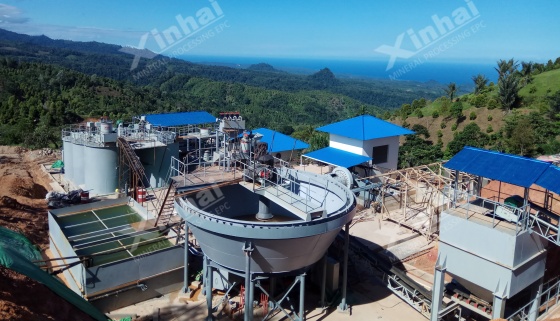
2. Cost Analysis
The investment cost of a chrome washing plant can be divided into the
following aspects:
(1) Site and infrastructure costs: The site should be located near the chrome
deposit. Infrastructure is the preliminary work for building a chrome washing
plant.
(2) Permits and licenses: Comply with local regulations and apply for mining
permits and licenses. The local government may require the company to take
pollution control measures.
(3) Equipment investment: including investment in crushing equipment,
re-selection equipment, dehydration equipment and some auxiliary equipment, as
well as equipment installation costs.
(4) Infrastructure and public facilities: including electricity costs (chrome
washing plants require a lot of electricity), water supply costs, and office
area construction costs.
(5) Operating costs: After the chrome washing plant is put into operation, we
usually have to pay more operating costs, including hiring workers, equipment
maintenance, raw material costs, etc.
Return on investment of chrome washing plant: Under the
conditions of Cr₂O₃>30%, large-scale production (200+ t/d), and low-cost
regions (such as South Africa and India), the ROI of chrome washing plants can
reach 20%~35%, which is very attractive. It is recommended to conduct ore
selectivity tests and market research in the early stage for accurate
calculation.
The above introduces the process flow, main equipment, investment cost and
return on investment of the chrome washing plant. As a Chinese company, Xinhai
Mining has undertaken many mineral processing businesses in more than 100
countries and regions around the world. We can provide customers with EPC+M+O
services, using scientific mineral processing processes and high-quality
equipment to create more profits for customers.