Silver is a common precious metal.The mining and processing of silver mines
is a complex process. From ore to pure silver, it is necessary to go through the
process of mining-ore dressing-smelting-refining. This article will
systematically analyze the complete process of silver mining, and provide
professional reference for friends who are concerned about silver mining and
processing.
Use the table of contents below to navigate through the guide:
01Silver Mining and Exploration
1. Exploration
In nature, silver often exists in the form of symbiosis with other metals,
such as lead, zinc, copper, gold, etc. The exploration work must first conduct
geological surveys, grasp the surface characteristics through satellite imaging
technology, and then combine soil sampling and analysis to locate the location
of the silver mine. Next, drilling and testing are completed to evaluate the
content and quality of silver in the ore.
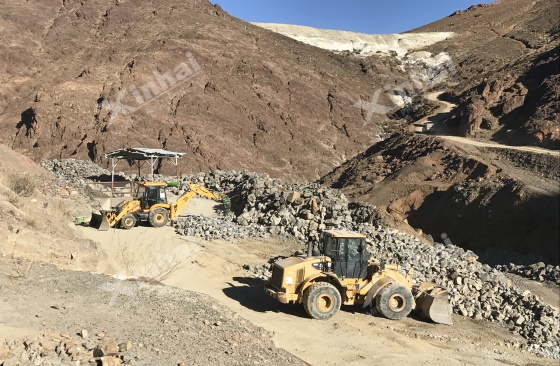
2. Mining
The choice of mining method depends on the occurrence parameters of the ore
body: when the stripping ratio is <6:1, open-pit mining is adopted, equipped
with a 40m³ electric shovel and a 240-ton mining truck; underground mining
mainly adopts the segmented caving method, and for thin vein ore bodies with an
inclination angle of >45°, a skylight drill is used in combination with the
VCR method. The current intelligent mining system has achieved a silver ore
depletion rate of less than 8%, and the mining recovery rate can reach 95%.
02Silver extraction
1. Pretreatment system
The raw ore is crushed through a three-stage closed-circuit process: jaw
crusher (feeding particle size 1200mm→250mm)→cone crusher (discharging
50mm)→high-pressure roller mill (-10mm). The grinding adopts a semi-autogenous
grinding + ball mill unit, equipped with a hydrocyclone classification to ensure
that the grinding fineness reaches -200 mesh accounting for 75-80%.
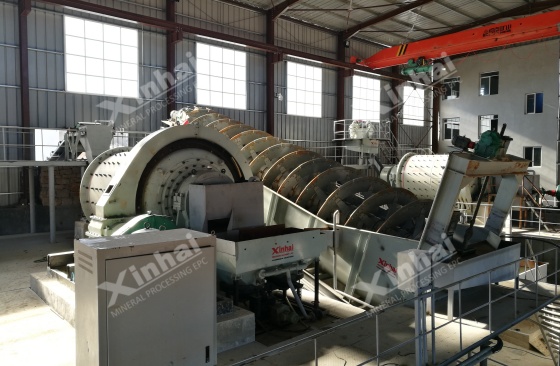
2. Silver ore flotation
Flotation is one of the most widely used mineral processing methods. During
the flotation process, the slurry is mixed with a series of chemical agents,
including collectors and frothers. The collector can change the properties of
the silver mineral surface, making it hydrophobic, so that it can attach to the
bubbles and float to the surface of the slurry; while the frother is used to
produce stable bubbles to help the silver mineral particles float and separate
from the waste rock (gangue). After flotation, concentrates with high silver
content can be collected, and their grade can usually reach 20% to 50%.
3. Silver ore gravity separation
For some ores containing coarse silver (embedded particle size> 50μm),
gravity separation is an effective means of enrichment. Gravity separation uses
the principle of centrifugal force to separate dense silver particles from
low-density gangue minerals through equipment such as shaking tables and spiral
chutes. In these devices, under the combined action of water flow and
centrifugal force, the silver particles move along a specific path of the
equipment due to their high density, and finally separate from the gangue.
Optimization of the mineral processing process is crucial to improving the
recovery rate of silver and the quality of the concentrate. Mineral processing
technicians need to accurately adjust the type and dosage of reagents and the
operating parameters of the equipment according to the properties of the ore to
ensure the best mineral processing effect. At the same time, with the continuous
advancement of science and technology, new mineral processing technologies and
equipment are constantly emerging, providing more options and possibilities for
silver mineral processing.
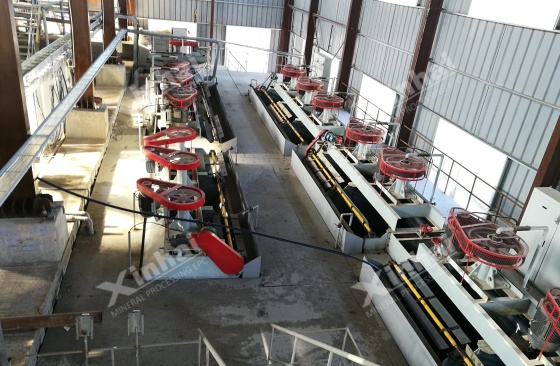
03Smelting and Refining
1. Smelting
The silver concentrate obtained after beneficiation will then enter the
smelting stage to remove impurities. In a high-temperature furnace (temperature
can reach about 1200°C), the silver concentrate is melted together with flux
such as quartz stone, limestone, etc. The role of the flux is to react
chemically with impurities in the ore to form slag. These impurities, such as
iron and sulfur, react with the flux at high temperature and float on the
surface of the molten metal in the form of slag, thereby separating from
precious metals such as silver. After this process, the remaining metal alloy is
called "Dole alloy", which contains a variety of metals such as silver, gold,
copper, and lead.
2. Refining
Electrolytic refining uses stainless steel cathode plates, electrolyte AgNO3
concentration of 80-120g/L, current density of 250-300A/m², and produces 4N
grade silver ingots. Anode mud treatment introduces pressure leaching
technology, and the comprehensive silver recovery rate reaches 99.2%.
The entire process of silver mining covers multiple complex links such as
exploration, mining, crushing, beneficiation, smelting and refining. Each link
requires the use of advanced technology and equipment, and requires strict
quality control and environmental protection measures.
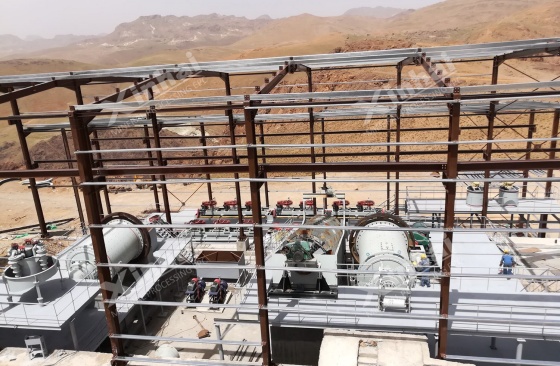
Xinhai Mining has focused on silver mine development for 30 years, providing
a full-process solution from geological exploration to beneficiation plant
construction. Xinhai has successfully implemented a number of large-scale silver
mining projects in Morocco and other places, and the beneficiation recovery rate
has increased by 8-15 percentage points compared with traditional processes. We
always focus on the core business of mining and beneficiation, and promote the
green development of precious metal resources with technological innovation.