Mining thickeners are the common equipment for dewatering process in mineral processing plants. They are used to concentrate thinner pulp into thicker pulp and separate liquids containing little or no solid matter.
There are 4 types of thickeners in mineral processing plants: rake thickener, efficient thickener, tilted plate thickener and deep cone thickener.
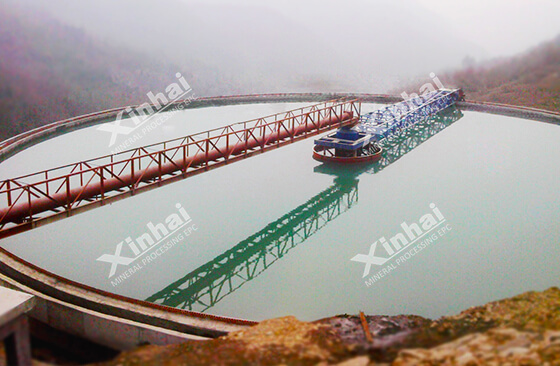
Use the table of contents below to navigate through the guide:
01Rake Thickener
Rake thickener is mainly composed of thickening tank, rake frame, transmission mechanism, feeding device and unloading device, mainly relies on gravity sedimentation to separate suspended solid particles from liquid. Rake thickeners are often used for dewatering fine-grained materials, with a maximum diameter of 150-183 meters. Rake thickener can be divided into two types: center transmission thickener and peripheral transmission thickener.
Classification of Rake Thickeners
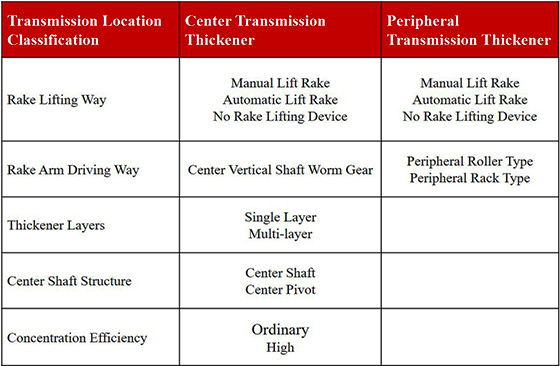
02Efficient Thickener
The structure of the tank body, rake and transmission part of the efficient thickener is roughly the same as that of the ordinary thickener. The main reason for its high concentration efficiency lies in a special feeding barrel. The pulp is fed into the exhaust system, and the air brought in is discharged, and then enters the mixing chamber through the ore feeding pipe, which is fully mixed with the flocculant, and then directly gives to the middle and upper part of the sediment layer through the radial distribution of the ore feeding pipe at the lower part of the mixing chamber. The liquid is filtered through the upper layer of the settling sand and then rises to overflow, while the floc stays in the settling sand and enters the bottom flow.
Under the condition of the same processing capacity, the diameter of the efficient thickener is only 2/3 to 1/2 of the diameter of the ordinary thickener, and covers an area of about 1/9 to 1/4 of that of the ordinary thickener, while the processing capacity per unit area can be increased several times to dozens of times.
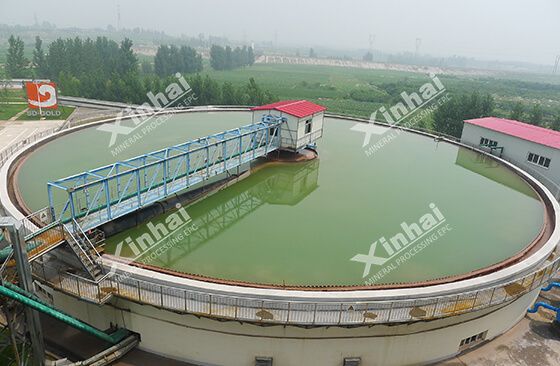
03Tilted Plate Thickener
Tilted plate thickener is a kind of high-efficiency dewatering equipment for fine-grained materials. It has small tank body, small occupation area and less investment, but it generally needs to add flocculant to the slurry. When working, the slurry is evenly fed into the thickening plate and the stable plate by the feed tube by the feed port. The overflow is discharged from the overflow dam to the manifold. The settling sand is deposited from the concentrator plate and slides down, deposited by the stabilizer plate into the square cone box and discharged from the discharge pipe. Since there are many thickening plates about 150 mm apart in the tilted plate thickener box, the sludge settling time and distance are effectively shortened, and the effective concentration area is greatly increased.
Some mineral processing plants use tilted plate thickeners for dehydration of fine-grained gravity separation products. However, it has poor dewatering effect on flotation products, and the slits of the inclined plates are easy to block, which often only acts as a chute.
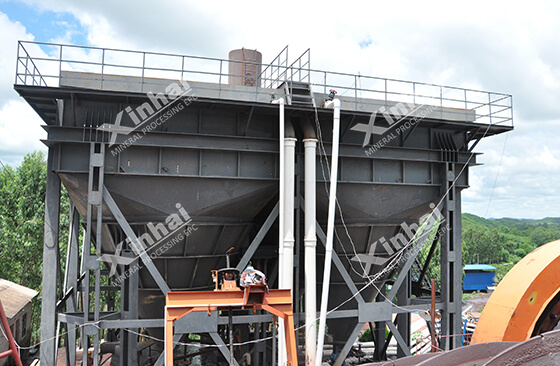
04Deep Cone Thickener
The cylinder body of the deep cone thickener is conical, and the bottom part of the cone is provided with a sand discharge valve for sand discharge and drainage in case of accident or maintenance. The cone angle is generally 55° or 60° , and 55° is generally used when the slurry contains mud. When the cone angle is less than 55° , the height of the body will increase with the same settlement area.
There are three main functions of deep cone thickener: (1) Concentration and dewatering of raw pulp before grinding. (2) Concentration and desliming of the overflow of pulp classification box before shaker operation. Gravity separation, flotation, magnetic separation products or slime dehydration. (3) Concentration and dehydration before ore feeding in centrifuge, belt chute and other separating operations.
The deep cone thickener has simple structure and no power consumption, which can play the role of ore storage, concentration and desliming to a certain extent. However, the precipitation area is small, the desliming efficiency is low, and the loss of configuration height difference is large. Generally, it is only suitable for primary dehydration of mineral processing products, and sometimes it needs to be dehydrated again when the overflow is sent to the next operation.
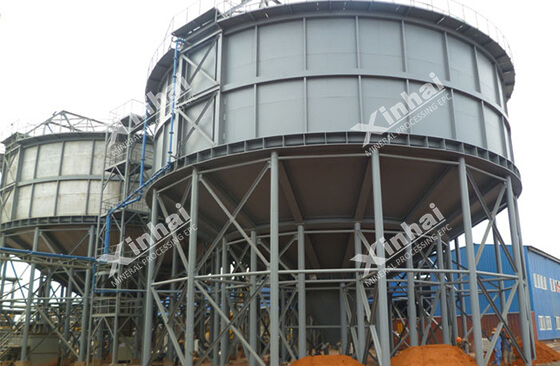
To Wrap Up
The above are the four common types of thickeners in mineral processing plants. Different mining thickeners are suitable for different environments, and the economic benefits produced are also different. It is recommended to carry out a mineral processing test before selecting a mining thickener, and determine the appropriate type and specification of the mining thickener according to the test results.