Use the table of contents below to navigate through the guide:
01Tubular Ball Mill
Widely used in cement, silicate. It has the similar function of cement ball mill.
Superfine lamination ball mill: combine screening and classification at one machine, which will dismiss the middle and fine screening and unti-dusting work.
02Cone Ball Mill
Could be installed on the horizontal plane, because it is a whole equipment which combine the machine itself and the trap at one machine.
Ceramics mill: the liner in the ceramic ball mill is made from ceramics. There are unitary ceramics ball mill and independent ball mill, which are used to mix and grind materials.
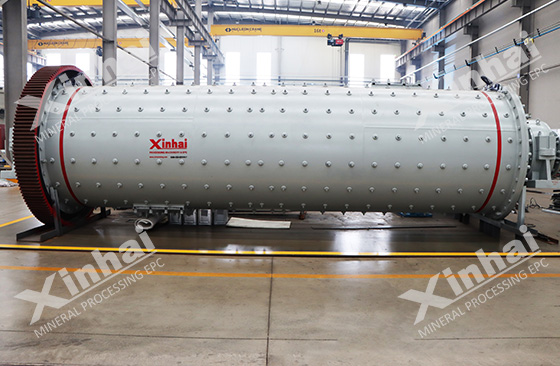
03Overflow Ball Mill
Materials are overflow through the hollow axis. The overflow ball mill are often indicate with MQY, such as the MQY2836 over flow ball mill form XINHAI mining machinery company limted.
04Grate Ball Mill
There are grate installed in the end of the discharging end. The grate are constituted by some fan-shaped plates where the sieve are 7mm to 20mm. Ore get into the room between the grate and cover, and then lifted by the lifting board. Materials slide along the lifting board and are discharged out of the machine.
There are also wind-force discharging ball mill, double warehouses ball mill and energy-saving ball mill.
05Critical Speed of Ball Mill
There is the force analysis of steel balls in the cylinder, which includes GSinα, Gcosα N, centrifugal force C and friction force F. When the centrifugal force and N are equal and opposite, F=0, the steel balls are divorced from the cylinder, making parabolic motion. It is the time when steel balls reach the highest. If the rotational speed is low, steel balls could not reach the highest, and N equals C, steel balls make parabolic motion. At that time, the height steel balls can reach is determined by the Critical speed of ball mill. If the mill rotates too fast, and the steel balls reach to the peak, C is bigger than G. Steel balls could rotate with cylinder, and there is a centrifugal rotation.

Therefore, Critical speed of ball mill is so important that it has a direct effect on its grinding efficiency.
First, we should consider its stress: steel ball's gravity itself, centrifugal force when doing circular motion, and friction force from the relative motion with the cylinder. Composition of three forces together determines the moving state of steel balls. Stress of steel balls is different with different positions. Therefore, steel ball's moving state is determined by its stress. During the process of grinding, the gravity of steel ball is related to its quality. Centrifugal force is related to the rotational speed of ball mill. The higher speed is, the bigger centrifugal force is.
06Grinding Balls for Ball Mill
Grinding medium and the way of steel ball’s moving in the ball mill determines its working efficiency, which is donated by the amount of ore that is qualified an hour. The principle of grinding balls for ball mill is that driven by the dynamo and transmission device, the cylinder rotates with the materials fed from the cylinder inlet and crushed by the falling impacts and autogenous grinding of the steel balls and ores in the cylinder. Due to the continuously feeding materials, the pressure pushes materials to the outlet and the grinded materials are discharged from the cylinder outlet. If there are only grinding balls for ball mill, steel balls have the phenomenon of moving when ball load is ten, twenty or thirty percent.
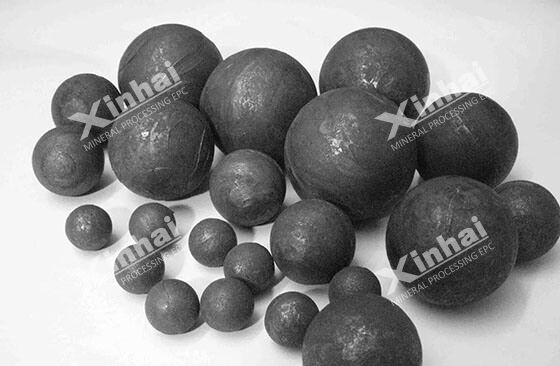
07Ball Mill Sizes
Steel balls installed in ball mill has a limit in size: there should be a proportion of different size steel balls. Commonly, ball mill sizes range from 25mm to 60mm. If there are only big size steel balls, small size ore are not ground fully which will influence grinding effectiveness. If there are only small size balls, impact force from balls is so small that grinding efficiency will be effected which will cause cost increasing.
There is must a certain percentage of the large balls and small balls in the mill, then the grinding effect is better. Due to the grinding, big steel balls will continue to wear into small balls, so in the production process, steel balls generally are in large diameter and small balls generally do not need to join.
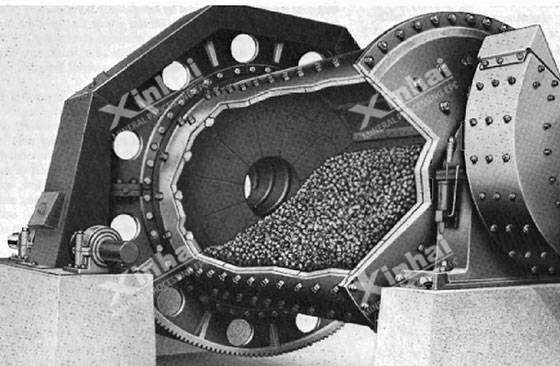
08Ball Mill Working Principle
The ball mill working principle is driven by the transmission device and dynamo, the cylinder rotates with the materials. With the force of friction, rotating cylinder drives the grinding medium-steel balls rise up, fall down and revolve. On the whole process, steel balls ran afoul of each other, collide with cylinder and materials. The collision of steel balls and materials is an effective work, which has a direct effect on the efficiency of semi autogenous grinding mills. However, the collision among steel balls and the collision between steel balls and liners reduce the rate of work and led to the wastage of steel balls themselves.
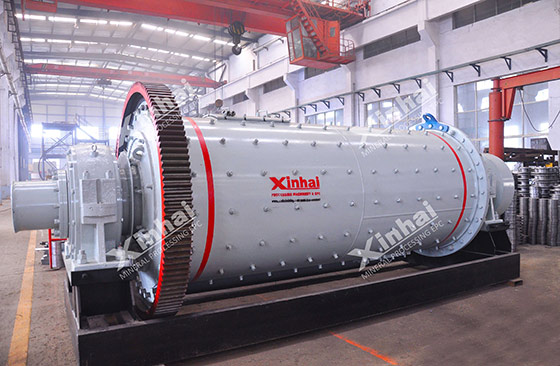
The movement state of steel balls are associated with the speed of the grinding machine. When mill rotates in a low speed, steel balls turn around their own axis, at the same time roll along the wall of shell. Steel balls rise to a certain height along the shell wall, then roll down the surface which means steel balls do falling movement. When the speed of the mill increases, steel balls rise to a certain height and not roll down along the surface, but along a parabolic which means steel balls do throwing movement. When the mill’s speed exceeds the whirling speed, steel balls do centrifugal movement inside the shell wall, which means steel balls do centrifugal movement. Steel balls have grinding effect only when they do falling movement and throwing movement. This is the ball mill working principle.