In the modern mineral processing industry, ball mill is one of the main equipment. With the global attention to production efficiency and energy conservation, the equipment update and application of ball mill is the key to improving productivity. This article will explain how to improve the working efficiency of ball mill from the aspects of working principle, types and applications, selection and configuration, maintenance and care.
Use the table of contents below to navigate through the guide:
01Working principle and classification of ball mill
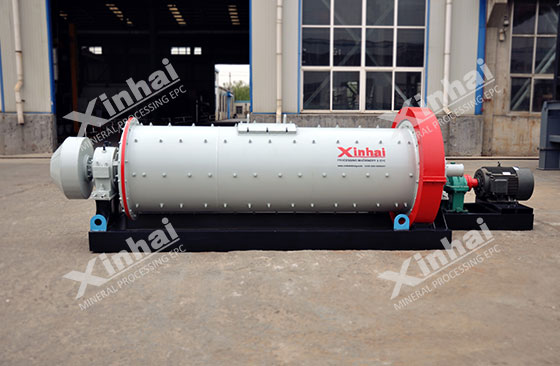
When the ball mill is working, the collision and friction between the high-speed rotating cylinder and the internal steel balls or ceramic balls can achieve the refinement and crushing of minerals. When the ball mill starts running, the ore rotates inside the cylinder along with the grinding medium, and constantly collides and grinds with the balls, and finally crushes the ore particles to the required particle size. Grinding methods can be divided into dry grinding and wet grinding. Choosing a suitable grinding method can improve the material processing efficiency. Dry ball mills mainly use air flow to help material discharge, while wet ball mills can reduce dust generation and increase fine grinding effect by adding water. They are mainly used for fine grinding of ore.
02Application and selection of ball mill
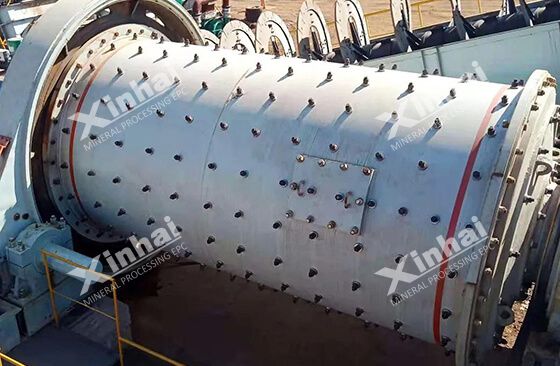
Ball mills are widely used, especially in the mining industry. They are the core equipment for processing raw materials such as ore and coal. Ball mills can provide necessary fine-grained materials for the next flotation, magnetic separation and other processes by grinding large pieces of ore, thereby improving the efficiency of subsequent processing. In addition, ball mills are also widely used in chemical, cement production, ceramic and other industries.
Choosing the right ball mill model is the key to improving production efficiency. When choosing, you first need to determine the type of ball mill based on the hardness, humidity and required particle size of the material. Ores with higher hardness require a ball mill with stronger grinding media and higher power. Secondly, according to the production scale and output requirements, the size of the cylinder, speed, grinding media and ratio should be considered when selecting. Accurate selection can not only improve grinding efficiency, but also reduce energy waste and ensure uniform fine grinding of materials.
In order to meet the needs of different customers, Xinhai Mining can customize and configure ball mills according to specific needs. For high-output requirements, choose a large-capacity ball mill and configure high-efficiency balls to increase the grinding effect of the material. For fine grinding requirements, a ball mill grinding system with high speed and multi-stage grinding can be selected.
03Maintenance and care of ball mill
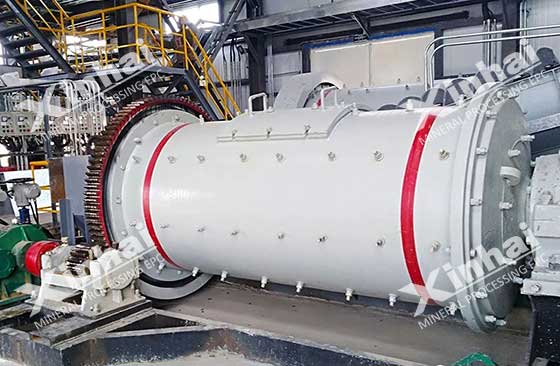
In order to ensure the long-term stable operation of the ball mill, regular maintenance and care are very important. First of all, regularly check the cylinder, liner, gears and other parts of the ball mill to avoid equipment failure caused by excessive wear and affect the overall mineral processing process. The liner and grinding medium of the ball mill need special attention. After being worn, they need to be replaced in time. Therefore, the liner of the ball mill should be made of high-efficiency and wear-resistant materials, which can effectively extend the service life of the ball mill and reduce the number of repairs and replacements.
In addition, optimizing the lubrication system and reducing mechanical friction can also improve the operating efficiency of the equipment. The bearing and gear system of the ball mill need to choose suitable lubricants, which can ensure its long-term stability and efficient operation after lubrication. Through precise maintenance measures, the service life of the ball mill can be effectively extended, the maintenance cost can be reduced, and the mineral processing stagnation caused by ball mill failure can be avoided.
04Energy saving and efficiency improvement of ball mill
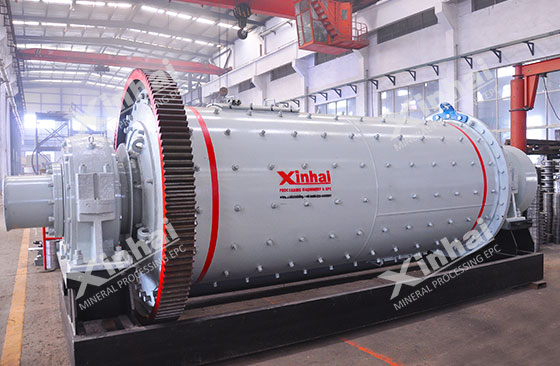
As energy costs continue to rise, ball mill energy conservation has gradually attracted attention from the industry. By adopting frequency conversion speed regulation technology, optimizing the grinding medium, and improving the cylinder structure, the energy consumption of the ball mill can be greatly reduced. The variable frequency drive system can adjust the speed according to the load and reduce unnecessary energy consumption. The use of high-efficiency motors and reducers can also significantly reduce the waste of electrical energy.
The new high-efficiency ball mill improves grinding efficiency and can produce more production value using the same energy. Optimize the internal design of the ball mill to improve material fluidity and medium impact effect, while reducing the residence time of materials inside the barrel, improving grinding efficiency and reducing energy consumption.
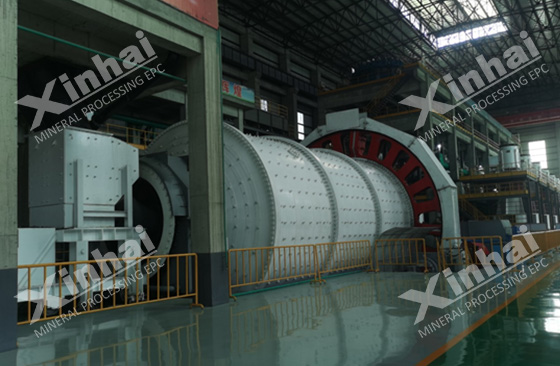
Ball mill is an indispensable key equipment in the mineral processing process and plays an important role in improving mineral processing efficiency, saving energy and reducing consumption, and improving product quality. With the continuous advancement of technology, ball mills have shown higher performance in traditional fields, while also gradually becoming intelligent and energy-saving. Therefore, choosing a suitable and advanced ball mill can help the mineral processing plant improve productivity, reduce operating costs, and improve economic benefits.