Magnetic separator is a key equipment in the mineral processing process, and the performance of the equipment will directly affect the mineral processing effect and product quality. The magnetic separator mainly separates minerals with different magnetic properties through the action of the magnetic field to achieve mineral enrichment and purification. In the mineral processing process, the setting of the magnetic separator operating parameters, the adjustment of the equipment, and the ore and other factors will affect the magnetic separation effect. Therefore, in the mineral processing process, it is necessary to strictly control the operating parameters such as the magnetic field strength, the rotation speed of the magnetic separation drum, and the feeding speed. Understanding these factors and optimizing the operating parameters of the magnetic separator have an important impact on improving the mineral processing effect.
Use the table of contents below to navigate through the guide:
01Drum speed on magnetic separation effect
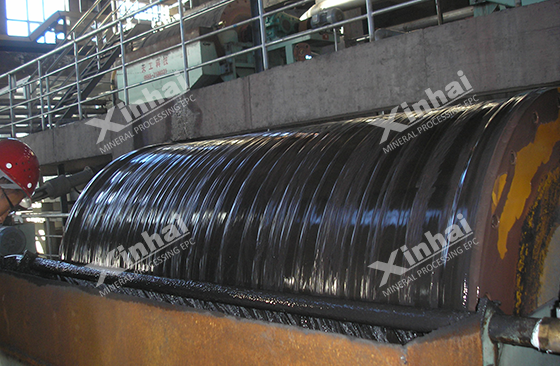
The drum speed will affect the processing capacity of the magnetic separator and the quality of the magnetic concentrate. Generally speaking, magnetic separators with smaller diameters use higher speeds, and magnetic separators with larger drum diameters use lower speeds. For example, the speed of a magnetic separator with a diameter of 600mm is generally 40r/min, while the speed of a magnetic separator with a diameter of 750mm is 35r/min.
When the speed of the magnetic separator is higher, the processing capacity of the equipment is increased, but the ore particles with weaker magnetism are difficult to be selected, so the concentrate quality is higher. When the speed of the magnetic separator is lower, the mineral particles with weaker magnetism are likely to be selected, which will cause the concentrate quality to decrease. Therefore, it is necessary to comprehensively consider the characteristics of the ore and the mineral processing indicators to select the appropriate drum speed.
02Magnetic system deflection on magnetic separation effect
.jpg)
The size of the magnetic system deflection will directly affect the quality and recovery efficiency of the mineral processing concentrate. During the operation of the equipment, the magnetic system deflection can be changed by adjusting the deflection on the shaft head. Selecting a suitable deflection can improve the mineral processing effect. Once the deflection is too small, the magnetic particles are more easily adsorbed on the magnetic system, reducing the tailings grade, increasing the recovery rate, but the concentrate grade decreases. On the contrary, when the deflection is too large, the separation is more stringent, the concentrate quality is improved, but the magnetic particles in the tailings increase, reducing the recovery rate. Generally speaking, the adjustment range of the magnetic system deflection is 15°-20°, and it needs to be adjusted according to the properties of the ore and production needs to ensure the best magnetic separation effect.
03Working gap on magnetic separation effect
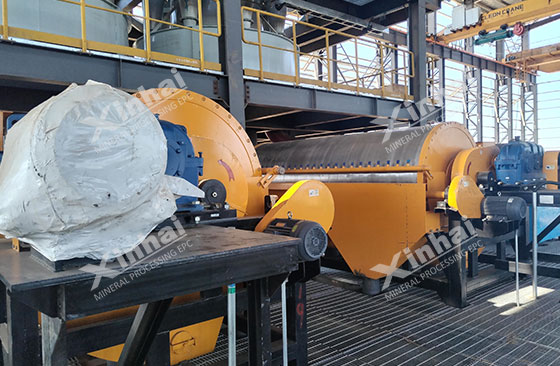
The working gap refers to the distance between the drum skin box trough body, which mainly affects the quality of magnetic separation concentrate. Working gaps that are too large or too small will affect the magnetic separation process. Too small a gap will affect the flow of slurry and increase the difficulty of mineral separation, but the recovery rate will increase and the grade of tailings will decrease. When the gap is too large, magnetic separation will only select the part with stronger magnetism of the ore particles, which will cause an increase in magnetic particles in the tailings, a decrease in the recovery rate, but an increase in the grade of the concentrate. Through long-term production practice, it has been verified that the working gap is better at 35-60mm, and it can be adjusted through the gasket under the bracket angle steel.
04Discharge gap on magnetic separation effect
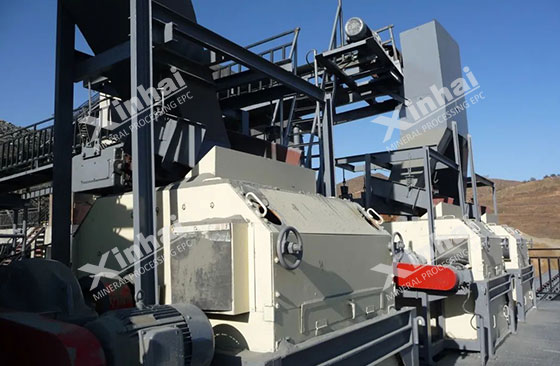
The discharge gap is an important factor affecting the smoothness of concentrate discharge, and its size will directly affect the magnetic separation efficiency and concentrate quality. In actual production, the discharge gap needs to be accurately adjusted according to production requirements. If the gap is too small, it will lead to poor discharge, blockage or backlog, and then cause concentrate loss in the tailings, reducing the overall quality of the concentrate. If the gap is too large, the residence time of the concentrate in the magnetic field will be prolonged, which may cause some concentrate particles to be discharged along with the tailings, affecting the mineral processing recovery rate. In order to achieve a balance between concentrate quality and recovery rate, it is usually recommended that the discharge gap be within the range of 15-20mm, mainly by moving the trough body back and forth to adjust the gap size.
05Effect of operating conditions on magnetic separation effect
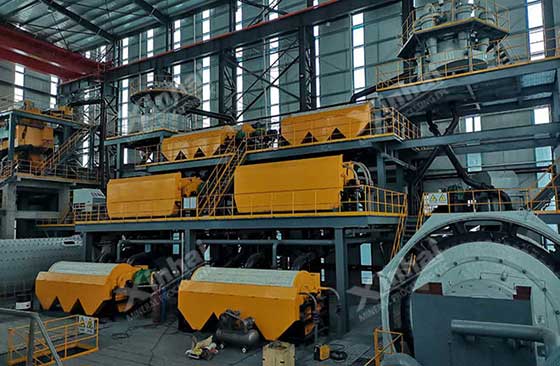
1. Angle and pressure of high-pressure flushing water: flushing water is mainly used for unloading ore. The angle and pressure of water spraying will affect the beneficiation effect. If the water spraying angle is too low, the concentrate particles will be washed back into the slurry, requiring re-selection. If the angle is too high, the unloading will be incomplete, affecting the selection efficiency. When the flushing pressure is too low, the magnetic field attraction cannot be overcome, resulting in residual magnetic particles. When the pressure is too high, it will cause a waste of resources. Adjust the water spraying angle by observation to obtain the best beneficiation effect.
2. Slurry concentration: Too high or too low concentration will affect the beneficiation effect. When the slurry concentration is too high, the viscosity of the slurry is large, and the concentrate particles are easily covered by gangue minerals, reducing the concentrate grade. When the slurry concentration is too low, the slurry flow rate will increase, which will shorten the selection time and cause the loss of fine magnetic particles.

Through comprehensive analysis of the key influencing factors of magnetic separation, it can be found that operating parameters, equipment adjustment and ore conditions play a vital role in the magnetic separation effect. Reasonable optimization of these factors can not only improve the quality of concentrates, but also improve resource utilization efficiency, thus providing a strong guarantee for mining production.