In modern mining production, ball mill is a kind of key grinding equipment, and their performance directly affects the efficiency and output of ore processing. Improving the output of ball mills can not only improve the economic benefits of mining companies, but also optimize production processes and reduce resource waste. To this end, it is particularly important to understand and apply some key optimization strategies.
Use the table of contents below to navigate through the guide:
01Optimization of ball mill feed particle size
Particle size affects grinding efficiency, so choosing the right material particle size is one of the ways to improve ball mill grinding efficiency. In actual production, smaller particle size helps to increase the contact surface and friction during the grinding process, thereby improving the grinding effect of the ore. Controlling the ore particles within the optimal range helps to increase the uniformity of grinding and the processing capacity of the ball mill, while reducing energy consumption. Generally, ore dressing plants will optimize the crushing and screening processes, use online monitoring and automatic control systems, and regularly evaluate the grinding effect to improve the overall performance and production efficiency of the ball mill.
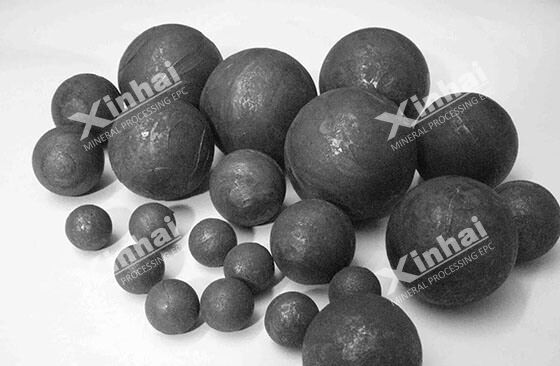
02Selection of grinding media for ball mill
Choosing the right grinding media and size is crucial to the grinding effect of the ball mill. Common grinding media are mainly steel balls, cast balls and ceramic balls. Steel balls are suitable for high wear occasions, cast iron balls are suitable for low wear occasions, and ceramic balls are more suitable for occasions with higher environmental pollution requirements. The size and weight of the media will also affect the grinding efficiency. Larger grinding media have greater impact and are suitable for coarse grinding processes, while smaller grinding media are more suitable for fine grinding processes. The density and hardness of the media will affect the friction and grinding during the grinding process. When selecting the type and size of grinding media, mineral processing tests and data analysis should be carried out in advance to optimize the output and grinding effect of the ball mill and reduce energy consumption and wear during the grinding process.

03Adjustment of ball mill speed and load
The speed and load of the ball mill are important factors affecting the grinding effect. The optimal speed should be determined according to the type and design characteristics of the ball mill, generally within the range of 60%-80% of the critical speed. Too fast or too slow will affect the working efficiency of the ball mill. When the speed is too fast, the centrifugal force of the medium and the ore increases, the grinding efficiency decreases and the energy consumption increases. Too slow speed will lead to insufficient grinding and reduce the production capacity of the equipment.
The load setting of the ball mill is mainly related to the amount of boring filling inside the equipment, which is measured by the filling rate. Appropriate load can ensure full contact between the medium and the ore. Too high load will cause poor material flow and increase equipment wear. Too low load will reduce the processing capacity of the equipment.
04Slurry concentration control
Slurry concentration, i.e. the ratio of ore to water, affects grinding efficiency and ball mill output. Higher concentrations can improve grinding efficiency because the chances of collision between ores increase, but too high a concentration will increase viscosity, slow down the movement of the medium and ore, and reduce grinding efficiency. On the contrary, although lower concentrations can reduce viscosity and promote the movement of the medium and ore, they may also lead to insufficient grinding and reduce processing capacity.
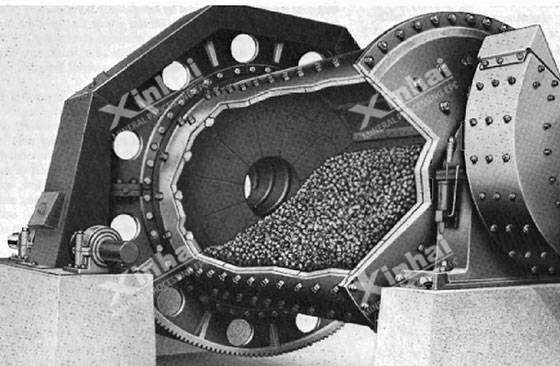
05Improvement of ball mill feeding method
When segmented feeding or uniform feeding is adopted, the grinding efficiency of the ball mill can be significantly improved.
Staged feeding refers to dividing the material into several parts and gradually feeding them into the ball mill in batches. This can avoid uneven grinding or overload caused by excessive feeding at one time. Optimizing the feeding method also includes adjusting the position and angle of the feeding port to ensure that materials are evenly distributed inside the mill.
Uniform feeding can improve the contact between the medium and the ore, reduce the retention and agglomeration of materials inside the mill, thereby improving the grinding effect and overall output. By improving the feeding method, the processing capacity and operating efficiency of the ball mill can be effectively improved.
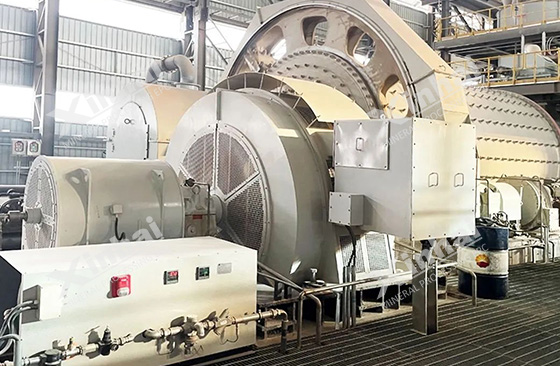
06Ball mill liner and screen optimization
Optimizing the material and design of the liner can improve its wear resistance and grinding effect. Liners made of highly wear-resistant materials (such as high chromium alloys or composite materials) can extend service life and improve grinding efficiency. In addition, optimizing the geometric design of the liner (such as corrugated, trapezoidal, etc.) can improve the movement trajectory of the medium and ore, thereby improving the grinding effect.
The aperture of the screen determines the discharge speed and particle size distribution of the grinding product. The appropriate screen aperture can prevent too many fine particles from being retained inside the mill, reduce over-grinding, and maintain the consistency of product particle size. Adjusting the screen aperture and design can optimize the material classification effect and improve the processing capacity and production efficiency of the ball mill.
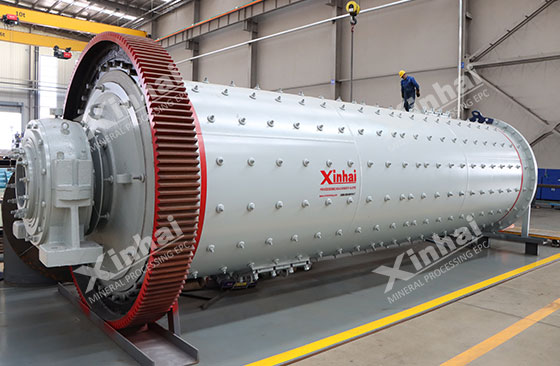
In addition to the above factors, regular maintenance and maintenance of the ball mill and the application of new technologies can improve the working efficiency of the ball mill. The implementation of specific measures should be verified based on mineral processing tests, data analysis and actual applications.