Placer gold is an important gold resource, and its mining and processing play an important role in the gold mining industry. The formation of placer gold is closely related to geological processes, usually based on the deposition of gold ore during natural transportation processes such as rivers, floods or wind. Understanding the types and properties of placer gold is essential for developing effective mining and beneficiation strategies. This article will introduce the different types and characteristics of placer gold in detail, and explore the beneficiation principles and specific steps of placer gold to help readers better understand the processing of placer gold.
Use the table of contents below to navigate through the guide:
01Types and properties of placer gold ore
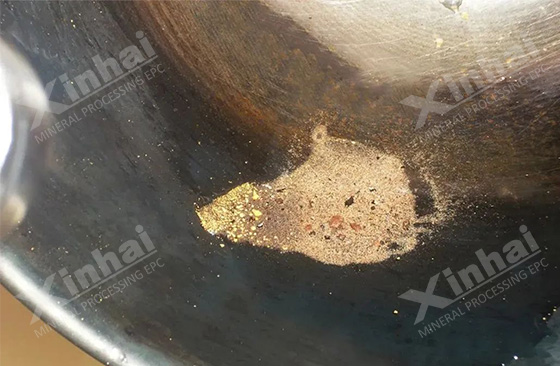
Gold in placer gold ore usually presents various forms such as granular, flaky or branch-shaped, and the particle size is generally between 0.5 and 2 mm. However, large nuggets of gold weighing several kilograms or fine particles of gold may also be found. The gold fineness is generally 50% to 90%, and the relative density is 17.6 to 18. Placer gold deposits are widely distributed, and the main types include: residual accumulation, slope accumulation, flood accumulation, riverbed alluvial and shore. Among them, riverbed alluvial type is the most common. According to the nature of the transport force, placer gold deposits can be divided into aeolian, glacial and hydrogenic types. According to the different transport eras, they can be divided into deep, terrace and river beach placer gold deposits.
The width of placer gold deposits is usually 50 to 300 meters, sometimes wider, and the length can reach several kilometers or longer. The burial depth is generally 1 to 5 meters, but it can also be as deep as 20 to 30 meters or deeper. The thickness of the gold-bearing layer of the deposit is usually between 1 and 5 meters, and the thickness of some deposits can reach 10 meters.
02Principles of beneficiation of placer gold mines
The beneficiation of placer gold mines usually adopts the gravity separation method, firstly recovering gold and its associated heavy minerals from the original ore sand. Then, through gravity separation, flotation, mercury mixing, magnetic separation and electrostatic separation, gold and other heavy minerals are separated to achieve comprehensive recovery. The separation process generally includes crushing and screening, desludging and separation.
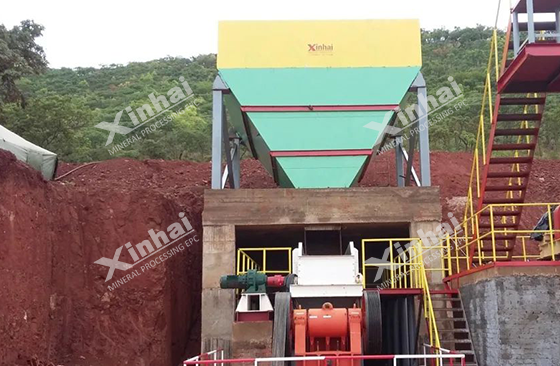
(1) Crushing and screening
Gold ore in placer gold often contains cemented mud clumps, which may exceed 100 mm in size. If these mud clumps are not effectively crushed, they may be removed together with waste rock during the screening process, resulting in gold loss. In addition, the mud may adhere to gravel or pebbles, which may also cause gold loss during the screening process if it is not crushed.
On gold mining ships, crushing and screening are usually carried out inside a drum screen, which is equipped with continuous spiral angle steel. The washing water pressure during operation should not be less than 35 kPa. Land-based fixed concentrators use washing beds for crushing and screening. Screening can remove 20% to 40% of waste rock and is an indispensable step in the selection of alluvial gold. Screening equipment includes grid screens, vibrating screens and drum screens. Water screens improve screening efficiency by flushing water on the screen and further crush the mud. Therefore, water screens are often used for screening of gold ore in alluvial gold. The flushing volume of the water screen should be determined according to the ore washing needs to meet the concentration requirements of the downstream separation process. For example, during the roughing of the chute, the flushing volume should be 8 to 14 times the amount of placer ore.
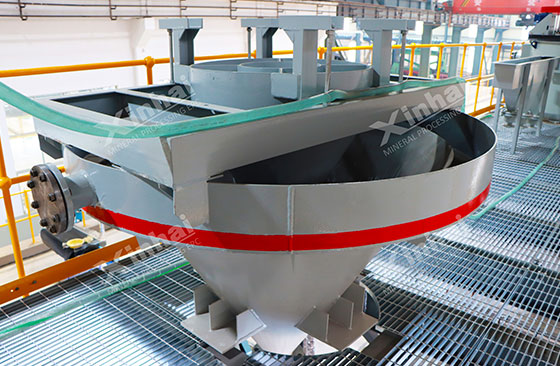
(2) Desliming
Materials with a particle size of less than 0.1 mm usually do not contain gold or have a very low gold content, which is called floating gold and is difficult to recover during the separation process. In addition, these ore slimes will interfere with the separation process, especially the mechanical separation process. Therefore, these ore slimes smaller than 0.1 mm need to be removed during the placer gold ore separation process. Commonly used desliming equipment includes various types of desliming buckets. However, due to the large processing capacity and wide particle size range of chute gold separation, desliming is usually not performed before chute separation.
(3) Separation
Gravity separation is the most effective and economical method for treating placer gold ore. Due to the different particle size compositions of gold, different gravity separation equipment has different effective particle size ranges for materials. Therefore, a reasonable separation process should be combined with multiple gravity separation equipment for joint operation. The gold grade of the gold-containing concentrate produced in the roughing stage is generally 100 g/ton, and the heavy sand mineral content is 1 to 2 kg/ton. There are currently three common methods for treating gold-containing rough concentrate:
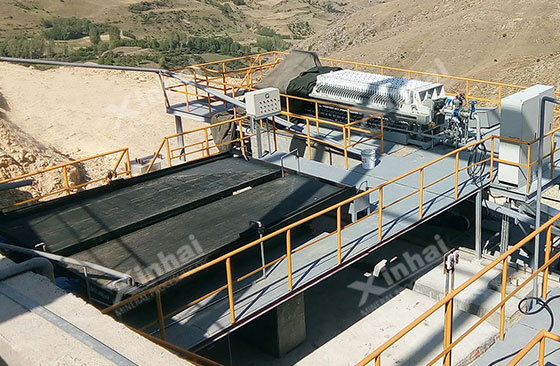
Use manual gold panning pan: Use manual gold panning pan to wash gold particles, separate gold particles, and then discard heavy sand.
Use mixing drum: Mix mercury through mixing drum, obtain mercury paste and discard heavy sand. This method is suitable for situations where mercury can effectively adsorb gold, but attention should be paid to the safe handling of mercury.
Comprehensive treatment method: First, after extracting gold through manual panning or amalgamation, the heavy sand is concentrated and sent to the concentrator for further processing. In the concentrator, magnetic separation, electric separation and other methods are used to separate various heavy sand minerals to ensure efficient recovery of gold and its associated minerals.
Each of these methods has its own advantages and disadvantages, and the specific selection should be reasonably configured according to the characteristics of the coarse concentrate and the processing requirements. The recovery rate of placer (sand) gold ore varies depending on the processing process: the recovery rate of two-stage chute separation is 70% to 74%, while the recovery rate of chute roughing, jig sweeping and shaking table selection is 85% to 90%.
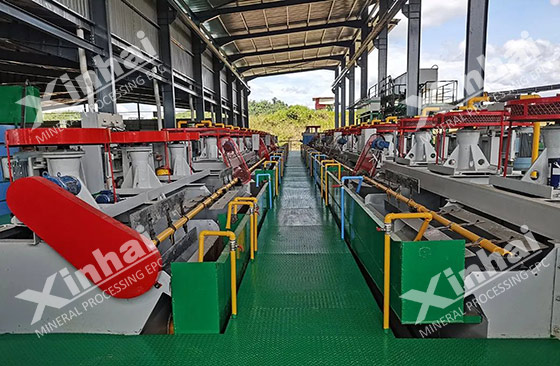
In summary, the treatment of placer gold ore involves a variety of complex beneficiation processes and equipment, including crushing and screening, desludging and gravity separation. Gold and its associated heavy minerals in placer gold ore can be effectively recovered by the comprehensive application of gravity separation, flotation, amalgamation, magnetic separation and electrostatic separation. Each beneficiation method and equipment has its unique advantages and scope of application. Reasonable selection and optimization of these processes are the key to improving the recovery rate of placer gold ore.