Flotation is a key step in the copper ore beneficiation process, and has an important impact on the copper recovery rate and economic benefits. In the copper ore flotation process, choosing the right and reasonable flotation equipment can ensure high flotation efficiency. Mechanical agitation flotation machines and air agitation flotation machines are two common flotation equipment. In the flotation process, optimizing operating parameters and flotation reagents are also important factors in improving flotation efficiency. The following article will introduce copper ore flotation equipment and optimize flotation operating parameters in detail to help you better understand copper ore flotation technology.
Use the table of contents below to navigate through the guide:
01Mechanical stirring flotation machine for copper ore
The mechanical stirring flotation machine is the key equipment for copper ore flotation. The working principle of this flotation equipment is based on the interaction between solid particles and bubbles in the ore pulp. In the flotation process of copper ore, the raw ore reaches a certain particle size after crushing and grinding, and the fine ore particles will be suspended in water to form ore pulp. When these ore pulps enter the flotation machine, the mechanical stirring device will introduce air to form a large number of tiny bubbles, which will contact and act on the copper sulfide particles in the ore pulp. Adding an appropriate amount of collector to the ore pulp will increase the hydrophobicity of the surface of the copper sulfide particles, and then the ore particles will adhere to the bubbles and rise to the surface of the ore pulp with the bubbles to form a foam layer. The foam product is rich in copper sulfide particles, which are then scraped out by the scraper to achieve the separation and enrichment of copper.
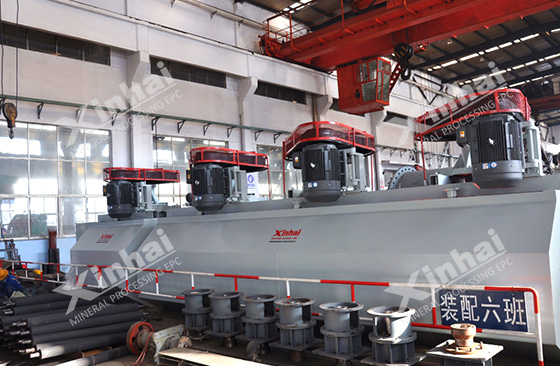
In actual production, the working effect of the copper ore mechanical stirring flotation machine will be affected by many factors, including stirring intensity, bubble size, slurry concentration and slurry pH value. Appropriate stirring intensity can ensure that the bubbles are in full contact with the mineral particles, but too intense stirring will cause the mineral particles attached to the bubbles to fall off, affecting the copper recovery rate. In summary, the design and operation of the flotation machine need to be optimized according to the characteristics of the copper ore and the flotation requirements. Reasonable adjustment of the stirring intensity and bubble generation rate of the flotation machine can effectively improve the copper recovery rate.
02Copper ore air agitation flotation machine
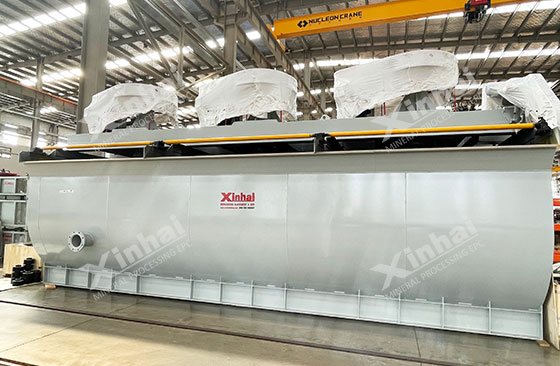
The air agitation flotation machine plays a vital role in the copper ore flotation process due to its unique design and working principle. The air agitation flotation machine mainly generates bubbles by introducing air. The bubbles combine with the copper ore particles in the slurry to form a foam layer, thereby achieving the separation and enrichment of the copper ore. Compared with the flotation machine with mechanical agitation, the flotation machine with air agitation has lower energy consumption and simpler maintenance. When processing fine-grained copper ore, the bubbles generated by the air agitation flotation machine are more evenly distributed, which is conducive to flotation selectivity and recovery rate.
03Operation and optimization of copper ore flotation process
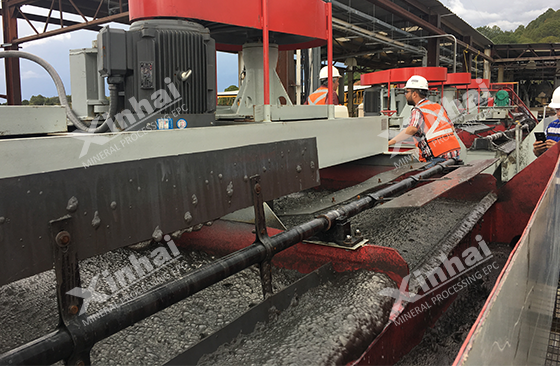
pH control in flotation process
During copper ore flotation, pH control directly affects flotation efficiency and selectivity. Copper sulfide ore flotation is often carried out in a weakly acidic to neutral environment, so the pH value is generally controlled in the range of 6-7. The surface hydrophilicity of copper sulfide minerals within this range is low, which is conducive to the adsorption of collectors, thereby improving the flotation effect of copper ore. The commonly used collector type for copper sulfide minerals is xanthate. The flotation pH value of copper oxide ore needs to be kept in the range of 9-11 to ensure the effectiveness of collector amine compounds. In the flotation process of copper ore, pH control is also closely related to the selection and dosage of flotation reagents, so it is necessary to comprehensively consider the chemical properties of the reagents and the characteristics of the ore to achieve the best flotation effect.
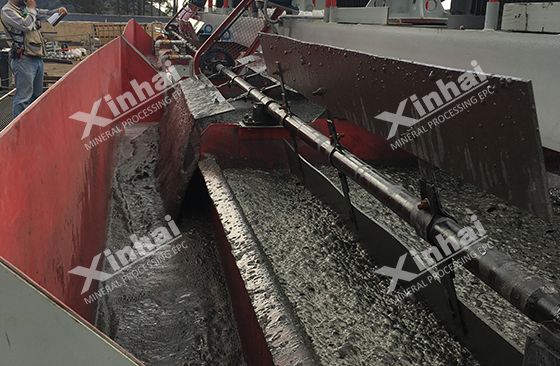
Optimization of flotation rate and recovery rate
When flotating copper ores, optimizing the flotation rate and recovery rate can improve the overall economic benefits. Increasing the flotation rate means processing more ore in a shorter time, while increasing the recovery rate is related to increasing the efficiency of copper extraction. Optimizing the use of flotation reagents can significantly improve the hydrophobicity of mineral surfaces and speed up the flotation rate. By precisely controlling the amount of collector added, the flotation rate can also be increased. In addition, the use of advanced flotation equipment can also improve the contact efficiency between bubbles and ore particles, thereby improving the copper ore flotation rate and recovery rate. If you want to improve the recovery rate of copper ore, you can adjust the pH value of the slurry to improve the charge state of the mineral surface, thereby improving the flotation selectivity.
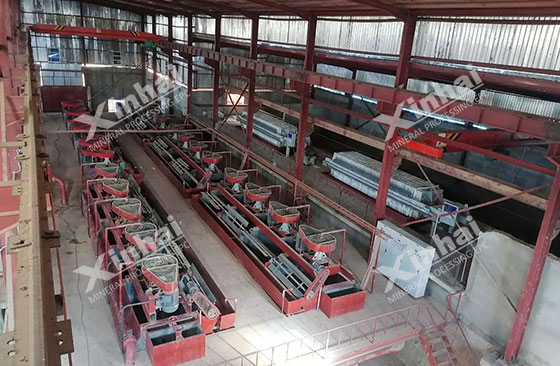
To sum up, the optimization of the copper ore flotation process needs to consider a variety of factors, including the selection of flotation equipment, the pH value of the slurry, the use of flotation reagents, and the adjustment of operating parameters. By rationally designing the copper ore flotation process and accurately controlling the flotation parameters, the recovery rate and flotation efficiency of copper ore flotation can be significantly improved, promoting the efficient utilization of copper ore resources and improving the economic benefits of the dressing plant.