In the production of modern mineral processing technology, fault diagnosis technology of mineral processing machinery and equipment has gradually received attention. If major equipment fails and fails to be discovered and eliminated in time, it will not only cause damage to the equipment itself, but also affect normal production, and may even cause serious consequences such as machine crash and death. In addition, in a continuous production system, if the main mineral processing machinery and equipment cannot continue to operate due to failure, it will often involve the operation of the entire plant's production system equipment, causing huge economic losses. As an important piece of equipment in the mineral processing production process, ball mill fault diagnosis is also very important. The following will introduce to you the necessity of ball mill fault diagnosis and the content of fault diagnosis to help you better operate and maintain the ball mill.
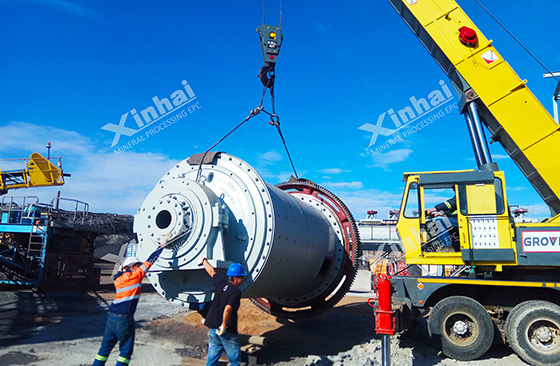
Use the table of contents below to navigate through the guide:
01The necessity of ball mill fault diagnosis
Ball mill, as a widely used and important grinding equipment in the mineral processing process, is increasingly becoming large-scale, automated and complex. Therefore, once the ball mill breaks down, it will often have a serious impact. If the equipment failure is not accurately predicted, the company will suffer huge losses. Therefore, the mineral processing plant spends a large proportion of maintenance costs every year to keep the ball mill system in normal operation. It can be seen from this that it is very important to diagnose and analyze the operating status, information and deterioration status of the ball mill.
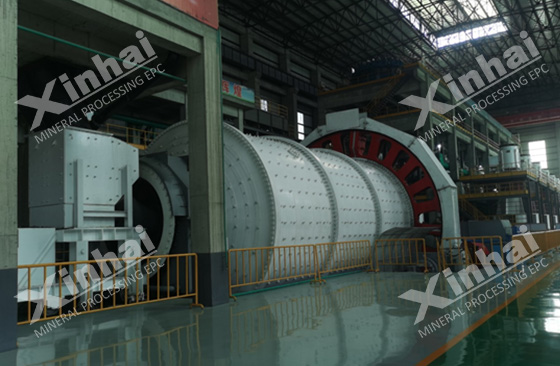
Cylindrical ball mill is a commonly used type of equipment in industrial production. While large-scale grinding equipment is developing, small and medium-sized grinding equipment also accounts for a large proportion in mining production. The grinding operation is mainly for the monomer dissociation of minerals to facilitate the subsequent separation process. As the main equipment of the grinding operation, the ball mill, its technical status, equipment integrity rate and operating efficiency will directly affect the selection operation. various indicators. As the operation rate of the ball mill increases, its failure rate and hidden dangers are also increasing year by year. Common ball mill failure conditions mainly include: "bulging belly" of the ball mill, "burnt shaft" of the bearing, cracks in the large shaft, rising temperature and loud noise of the reducer, broken gear shaft and broken teeth, uneven wear of large and small gears, local defects, and spots. Loud noise and vibration caused by corrosion, gluing and coupling misalignment.
02Main diagnostic contents of ball mill faults
(1) Diagnosis of bearings at both ends of ball mill
The bearings at both ends of the cylinder are an important support system in the ball mill. They are affected by fatigue wear, indentation, cracks, burning and other factors, resulting in bearing damage. Once the bearing is damaged, it will produce impact vibration. The height ratio of the impact waveform can be used as an indicator to indicate the varying degrees of bearing damage. Through the diagnostic system, the degree and location of bearing damage can be grasped in time, and the working time of the bearing reaching the critical level can be estimated and an alarm can be issued in time to stop the use to avoid the phenomenon of "shaft burning".
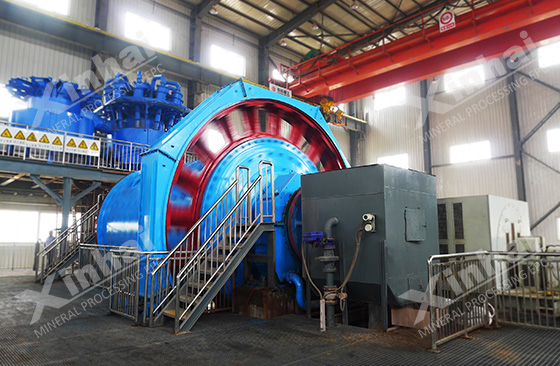
(2) Monitoring and diagnosis of reduction gearbox
It mainly monitors the operating status and deterioration of the gears, shafts and rolling bearings in the reduction box. The analysis of the fault point and cause of the fault is based on the vibration amount (vibration speed effective value) of each measuring point of the reducer and the spectrum characteristics of the three-dimensional direction of the gear shaft. The ball mill reducer is also a frequently encountered part of the machine.
(3) Monitoring of ball mill operating status
Record, monitor and protect the starting current, starting voltage, operating current and operating voltage of the main motor of the ball mill.
(4) Ball mill“belly swelling”protection system
The filling rate of the grinding equipment during operation can be detected by a power transmitter. The level of the output signal is directly proportional to the load inside the ball mill. That is, the greater the load, the higher the signal output of the power transmitter. However, when the ball mill "swells", the power transmitter signal does not increase but decreases. Therefore, it is ensured that the grinding equipment works within the power signal close to the threshold. Through physical calibration, the power signal of the "swelling" trend point of the grinding equipment is used as " Bloated belly” signal critical point. When the power signal is greater than the critical point, the grinding equipment works normally. If the power signal is lower than the critical point, it means that the grinding equipment has a "bulging belly" tendency, and the control process enters the "bulging belly" protection part. During the protection process, the working status of the grinding equipment is mainly adjusted through feedback signals, controlling the ore supply volume, and the graded sand return ratio.
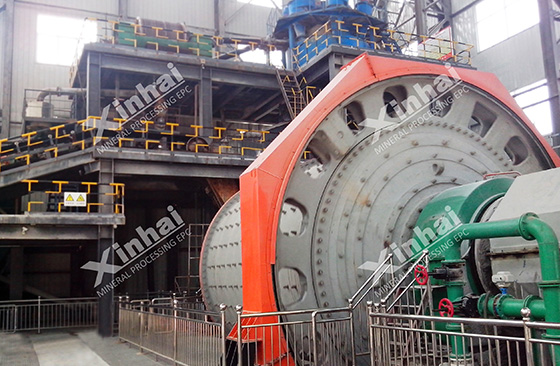
The above content is a brief introduction to the fault diagnosis and diagnostic content of the ball mill. In actual production, there are many factors that affect the operation of the ball mill, and real-time monitoring and regular maintenance are required according to production conditions to ensure the normal and efficient operation of the ball mill. Xinhai Mining, as a professional ball mill manufacturer, can provide you with more operating skills on ball mill operation and maintenance.