During the grinding process, the consumption of grinding media is large, and its cost accounts for half of the grinding cost. Understanding the relationship between grinding media and grinding efficiency can provide high-quality conditions for the grinding process and improve grinding efficiency, thereby Achieve direct or indirect reduction of grinding costs. The following will introduce to you the aspects of grinding media that affect the working efficiency of grinding equipment and help you improve the efficiency of the grinding process.
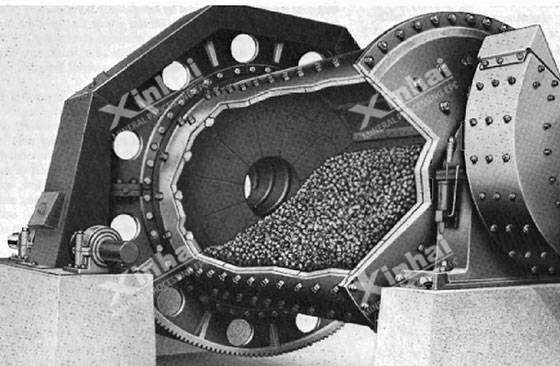
Use the table of contents below to navigate through the guide:
01Suitable mill speed to improve grinding efficiency
Both ball mills and rod mills use the rotation of the cylinder to move the grinding medium and grind the ore. The movement modes of grinding media in the cylinder can be divided into three types: falling, throwing and centrifugal movement. When performing fine grinding, it is necessary to strengthen the grinding effect on the material. During rough grinding, the impact on the material needs to be strengthened. Theoretically, rough grinding requires all the steel balls to make a throwing motion and some of the steel balls to make a falling motion. Practice has proved that when the filling rate of steel balls is normal and the rotation speed of the mill is 88% of the critical speed, the throwing point of the steel balls is higher and the throwing distance is larger. The grinding efficiency is better.
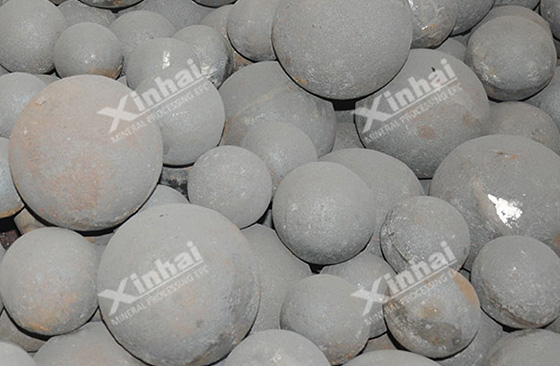
02The influence of steel ball material on grinding efficiency
The material of the grinding ball directly affects the use effect of the ball mill and the economic benefits of grinding. In order to achieve good grinding effects and reduce the consumption of grinding media, the required grinding media must have high hardness and good wear resistance. At the same time, it should Tough enough to ensure that it does not break when impacted within the equipment. The hardness and toughness of steel balls are mainly affected by their chemical composition, metallographic structure and heat treatment status. At the same time, the roundness of the steel ball, segregation of alloy elements and defects on the surface of the steel ball will also affect the normal working efficiency of the ball mill. Because the cost of grinding media is one of the most expensive items in the production cost of a mineral processing plant, in order to ensure good economic benefits, when selecting a ball mill, attention should be paid to the material of the grinding media.
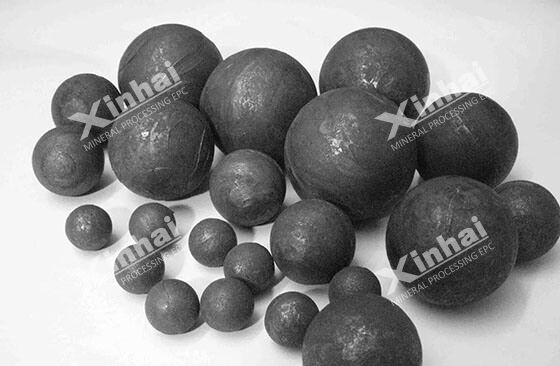
03Effect of ball charge on grinding efficiency
The working efficiency of the grinding equipment is related to the degree of throwing of the steel balls and the height of the throwing point. However, when the steel balls move in the mill, there will be relative movement along the lining plate. The steel ball can reach the height of the throwing point along the lining plate because there is sufficient friction between the steel ball and the lining plate. The higher the filling rate of the steel ball, the greater the pressure between the steel ball and the lining plate, and the greater the friction force. Therefore, if you want the steel balls to perform a throwing motion, you must ensure a sufficient filling rate so that the steel balls can complete the impact and grinding and peeling effects on the material, thereby ensuring the grinding efficiency of the equipment. The filling rate should be appropriate. If it is too high, it will reduce the effective operating volume of the grinding equipment, affect the processing capacity of the grinding equipment, and increase the energy consumption of the grinding equipment.
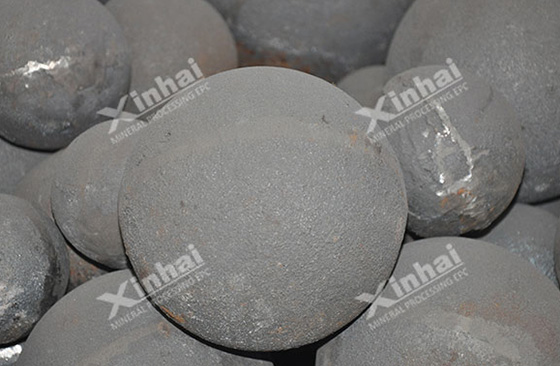
04Effect of steel ball diameter on grinding efficiency
In the fine grinding process, the particle size of the material is finer, and the focus is on grinding the material. Therefore, the diameter of the steel ball required is smaller, and the gap between the steel balls is smaller. Therefore, the steel ball can fully grind the material during the movement. When the material is coarsely ground, it needs to be impacted and broken, so the diameter of the steel ball is larger. During the throwing process, the impact force on the material is larger and the grinding efficiency is high. Therefore, it is necessary to adjust the material and ratio of steel balls during grinding to obtain ideal grinding indicators to a reasonable extent.
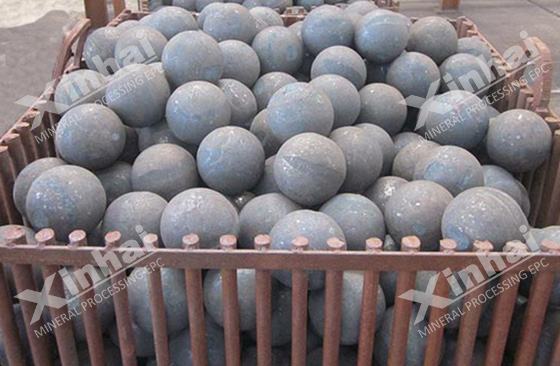
05Effect of ball ratio on grinding and classification efficiency
The working efficiency of grinding equipment is mainly reflected in two aspects: processing capacity and grinding fineness. If only one of them is met, the working efficiency of the grinding equipment cannot be reflected. When the proportion of large steel balls in the ball mill is large, the impact of the grinding medium on the material is large and the equipment processing capacity is large. However, due to the large gap between the steel balls, it will lead to insufficient grinding of the material and discharge of mineral products. Coarse particle size will increase the classification cycle load, which will affect the grinding capacity, and vice versa. In actual production, it is difficult to achieve the ideal ratio of steel balls, and the concentrator generally needs to add balls regularly to ensure it.
06Effect of grinding concentration on grinding efficiency
The grinding concentration will affect the specific gravity of the slurry, the degree of adhesion of the ore particles around the steel balls and the fluidity of the slurry. The grinding concentration is low, the slurry flows quickly, and the adhesion of the material around the steel ball is low, resulting in weakened impact and grinding effects of the steel ball on the material, and the particle size of the discharged mineral product is unqualified. When the grinding concentration is high, the adhesion of the material around the steel ball is good, and the impact and grinding effect of the steel ball on the material is increased. However, the slow flow of the slurry easily causes over-crushing of the material, which is not conducive to increasing the processing capacity of the grinding equipment.
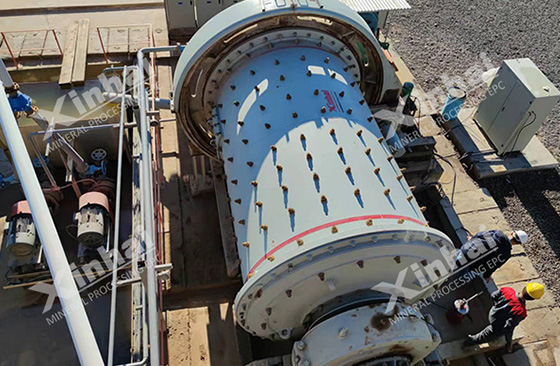
The above are several aspects of grinding media that affect the working efficiency of grinding equipment. In actual production, there are other factors that affect the grinding efficiency of the equipment, and the specific adjustment strategy should be applied according to the actual situation. Because the grinding and classification process is quite complex, and the existing influencing factors change from time to time. Therefore, qualitative analysis is needed to judge the impact, and adjustment decisions cannot be made quantitatively. Continuous optimization of the grinding and classification process can improve the production line efficiency of the entire mineral processing plant. Reduce production costs and energy consumption, and improve the economic benefits of the dressing plant.