Grinding is an important process in the mineral processing. It uses mechanical means to reduce the ore particle size to the required particle size for mineral processing, which is convenient for subsequent mineral processing operations. The grinding process is affected by many factors, mainly ore properties, equipment conditions and operation aspects. In order to optimize the grinding effect and improve the mineral processing productivity, it is necessary to have a deep understanding of these factors and take appropriate adjustment measures. The following will give you an in-depth introduction to the factors affecting grinding, helping you to better understand the grinding process.
Use the table of contents below to navigate through the guide:
01The influence of ore properties on grinding effect
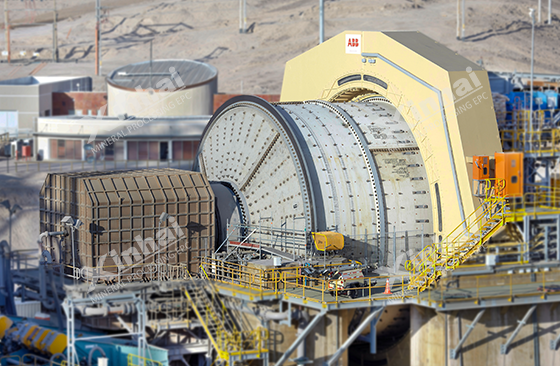
1. Ore particle size: The initial particle size of the ore will affect the production capacity and grinding effect of the grinding equipment. Equipment with larger particle size will reduce the production capacity of the grinding equipment, and ore with smaller particle size can improve the grinding efficiency. The requirements for the particle size of the grinding product are different, and the size of the in-grinding particle size has different effects on the production capacity of the ore dressing. In actual production, it is necessary to adjust the working parameters of the grinding equipment according to the particle size characteristics of the ore.
2. Ore hardness: Ores with higher hardness require longer grinding time to achieve the required fineness, so they will affect the processing capacity of the grinding equipment to a certain extent. Ores with lower hardness are easy to grind, and the processing capacity of the grinding equipment will also increase accordingly. In production, when handling ores with higher hardness, operators need to adjust the operating parameters appropriately to improve the grinding effect.
3. Ore physical properties: The physical properties of the ore, such as the structural density and crystal particle size, will affect the grinding process. Dense ores with smaller crystals are difficult to grind, and the grinding time needs to be extended to achieve the goal. Ores with loose structures and fragile structures can quickly reach the required particle size.
02The influence of grinding equipment on grinding effect
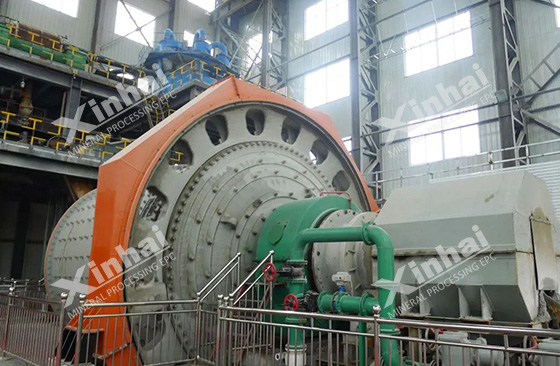
1. The diameter and cylinder length of the grinding machine: The unit volume productivity of the grinding equipment is proportional to the square root of its diameter. Grinding equipment with a larger diameter can withstand greater load pressure and steel ball impact force, so its processing capacity is larger. In recent years, grinding equipment has gradually developed towards large-scale, increasing its diameter to increase its processing capacity.
2. Liner type and material: The liner type and material inside the grinding equipment have an important influence on the grinding efficiency and product quality. When a liner with a low manganese content is used, its wear resistance is poor, which is easy to affect the impact of the steel ball on the ore, thereby reducing the grinding efficiency. Xinhai Mining uses wear-resistant rubber plates as liner, which can effectively improve wear resistance and grinding efficiency.
3. Ball loading and filling rate: Reasonable ball loading and filling rate can improve grinding efficiency. However, too few steel balls will lead to poor grinding effect, and too many steel balls will affect the normal circulation of steel balls and reduce grinding efficiency. When the speed of the grinding equipment is low, the grinding effect can be improved by appropriately increasing the amount of balls loaded. In production, the medium filling rate can be adjusted according to the speed to improve the grinding effect.
03The influence of operating conditions on grinding effect
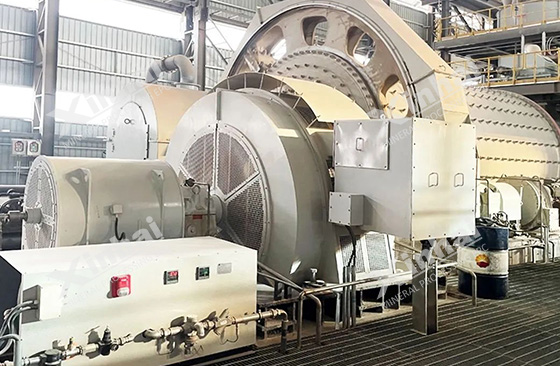
1. Discharge concentration: The slurry concentration will directly affect the fluidity of the slurry and the conveying capacity of the ore particles. Too high or too low a concentration will affect the grinding efficiency. Generally, the grinding concentration is more suitable in the range of 60%-83%. The slurry concentration is higher during coarse grinding, and the grinding concentration can be appropriately reduced during fine grinding. The optimal slurry concentration varies with the specific gravity of the ore, and needs to be adjusted according to the specific characteristics of the ore.
2. Matching of grinding time and grinding medium: During the grinding process, the grinding time determines the degree of ore grinding. Ores with higher hardness require longer grinding time. Operators should adjust the grinding time according to the characteristics of the ore, and ensure that the grinding medium matches the properties of the ore.
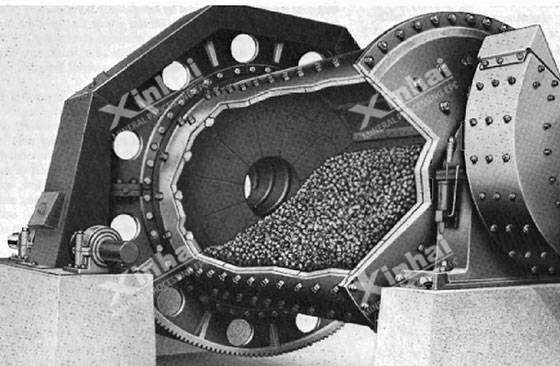
The above is an introduction to the factors that affect grinding efficiency. In summary, the grinding effect and quality will be affected by factors such as ore properties, equipment configuration and operating conditions. In order to ensure the best grinding effect, operators need to flexibly adjust the parameters of the grinding equipment, such as the particle size of the grinding, the discharge concentration, and the grinding time, according to the characteristics of the ore particle size and hardness. In addition, the design of the grinding equipment and the selection of the lining material are also ways to improve the grinding efficiency. Taking these factors into consideration, the grinding effect can be maximized and the product quality can be improved.