Flotation is an important mineral processing technology. It is affected by many factors during the flotation process. These factors are directly related to the mineral separation effect and the recovery rate of the concentrate. Among them, grinding fineness, pulp concentration, reagent dosage, aeration and stirring, flotation time and flotation process are all key factors that affect the interaction between minerals and flotation reagents. In addition to these main factors, water quality and pulp temperature will also have a certain impact on the flotation effect. In order to more clearly understand the impact of these factors on the flotation process, these key factors will be introduced in detail below. Through the analysis of these factors, important theoretical support can be provided for the optimization and improvement of the flotation process.
Use the table of contents below to navigate through the guide:
01Effect of grinding particle size on flotation process
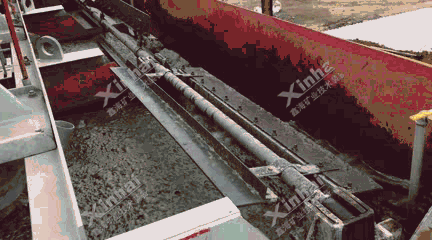
Mineral particle size that is too coarse or too fine will affect the recovery rate of the mineral, so the grinding particle size must be strictly controlled during flotation. When the mineral is coarse-grained, the mineral particles are heavy and easy to fall off from the bubbles, so some optimization measures need to be adopted, such as adding sufficient high-efficiency collectors, increasing the aeration volume of the slurry to generate larger bubbles and microbubbles, properly controlling the stirring intensity or increasing the slurry concentration. When the mineral is a finer sludge, due to its small mass, it is easy to adhere to the surface of the coarse particles, reducing the floatability of the coarse particles. Fine-grained minerals have a large specific surface area and are easy to adsorb a large amount of flotation reagents, resulting in a decrease in reagent concentration, which in turn affects the flotation efficiency. In summary, reasonable control of grinding fineness and ensuring that the mineral particles are within the appropriate particle size range are the key to improving flotation recovery and concentrate quality.
02Effect of slurry concentration on flotation process
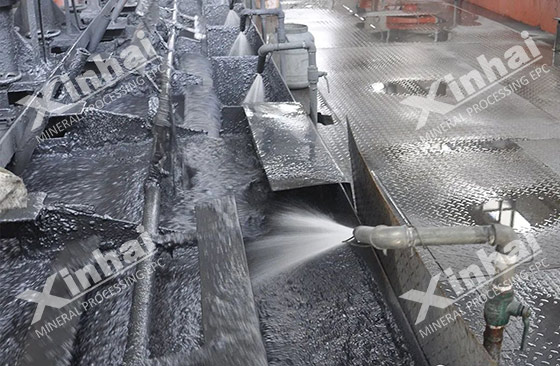
Slurry concentration is a key control parameter in the flotation process, which has a direct impact on mineral recovery rate, concentrate quality, reagent consumption, flotation equipment working efficiency and energy consumption. Reasonable slurry concentration helps to improve mineral recovery rate, but too high slurry concentration will destroy the aeration conditions of the flotation machine, resulting in poor separation of bubbles and mineral particles and reduced recovery rate. In general, dilute slurry is more conducive to improving the quality of concentrate, but it will also increase the amount of reagents and energy consumption. Concentrated slurry can effectively reduce reagent consumption and water and electricity costs, and the processing capacity of flotation equipment can be further improved, but the flotation time will be extended. Therefore, according to the characteristics of different ore properties and the requirements of production processes, the slurry concentration range should be reasonably determined to ensure flotation within the optimal concentration range, so as to achieve efficient flotation.
03The influence of flotation reagents on flotation process
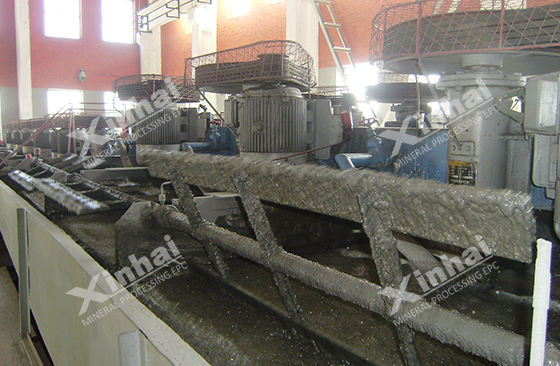
As the core element in the flotation process, the types, dosages, dosing locations and dosing methods of flotation reagents are collectively referred to as reagent systems. Among them, the reasonable control of reagent dosage is particularly critical. Increasing the dosage of collectors and frothers within an appropriate range can speed up flotation speed, improve recovery rate and concentrate quality. However, if the dosage of reagents is too much, the foam stability is too strong, and the selectivity of mineral particles becomes poor, thereby reducing the mineral recovery rate and concentrate quality. The dosage of inhibitors and activators also needs to be precisely controlled. Excessive or insufficient dosage will affect the flotation effect. Therefore, in the flotation process, the optimal dosage of reagents and dosing methods are determined through mineral processing tests and production practices to ensure the efficiency and stability of the flotation process.
04Effect of aeration and stirring on flotation process
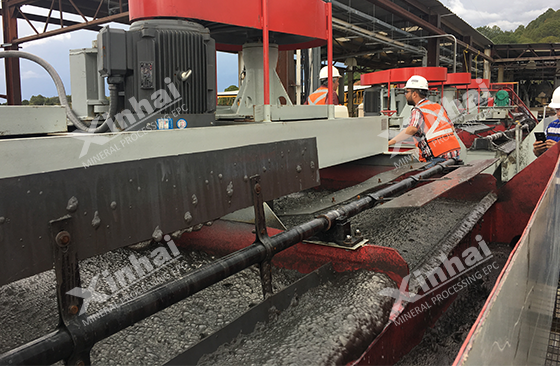
Aeration and stirring are necessary operation links in flotation process, which have a direct impact on flotation effect. Bubble size and stirring intensity need to be finely controlled to ensure the stability of flotation process while improving mineral recovery rate and concentrate quality. Small bubbles have a larger surface area and more contact opportunities with mineral particles, which helps to improve recovery rate and concentrate quality. However, if the bubbles are too small, the floating speed will be changed and the flotation efficiency will be affected. The role of stirring is to promote the suspension and uniform dispersion of mineral particles. After uniform stirring, the air is fully dispersed in the slurry to form a large number of active microbubbles, and the flotation effect is enhanced.
Aeration and stirring need to be appropriate. Excessive aeration and stirring will bring many negative effects, such as increased energy consumption, reduced concentrate quality, and increased equipment wear. Therefore, in actual production, it is necessary to determine the optimal aeration volume and stirring intensity through mineral processing tests according to the type and structure of the flotation machine to ensure the efficient and stable operation of the flotation process.
05The influence of flotation time on flotation process
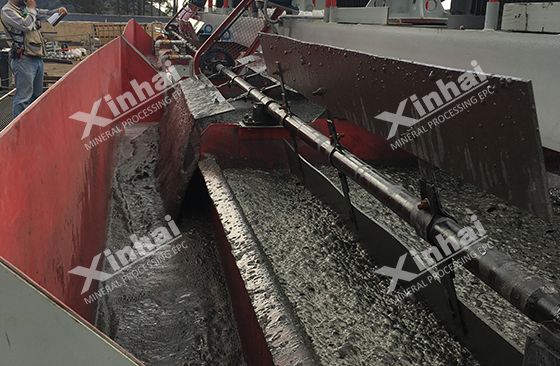
Each ore has its appropriate flotation time. When the flotation time is too short, the ore particles cannot fully contact with the bubbles, reducing the recovery rate. When the flotation time is too long, the concentrate quality will decrease and the beneficiation cost and energy consumption will increase. The determination of flotation time is affected by many factors such as ore floatability, target mineral content, feed particle size, and reagent system. Reasonable control of flotation time and ensuring that the flotation process operates within the high-efficiency range are the key to achieving high recovery and high-quality concentrate.
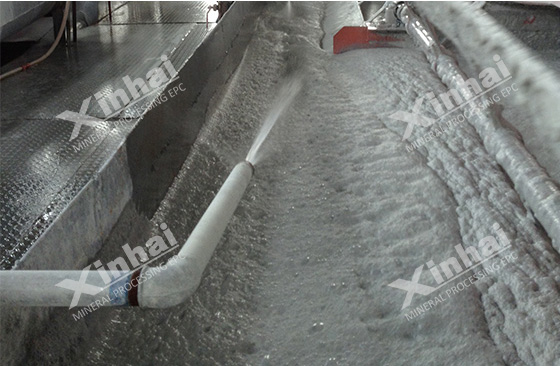
The above is an analysis of the factors affecting the flotation process. It can be seen that the efficient operation of the flotation process depends on the coordinated control of multiple key factors. The reasonable adjustment of these factors will directly affect the mineral sorting effect and the recovery rate of the concentrate. According to the differences in the properties of different ores, optimizing the operating conditions of each link can not only improve the mineral recovery rate and concentrate quality, but also reduce the cost of beneficiation reagents and energy consumption, and achieve a double improvement in the production efficiency and economic benefits of the beneficiation plant. In actual production, it is necessary to combine mineral processing tests and production requirements, dynamically optimize and adjust these factors, and continuously improve the efficiency and quality of the flotation process.