Flotation, as an important mineral separation process, its design is directly related to production efficiency, resource utilization and economic benefits. The scientific flotation process can significantly improve the concentrate recovery rate, reduce tailings loss, and reduce energy consumption and mineral processing costs. This article will introduce you to the core technology, design elements, common process types, selection and scavenging design, medium ore treatment methods, optimized flotation process, etc. of the flotation process, and provide methods for the design and optimization of the flotation process.
Use the table of contents below to navigate through the guide:
01Core technology of flotation process
The core technology of flotation process is: roughing, concentrating and scavenging. The reasonable configuration and optimization of each flotation process are the key to ensure the flotation effect.
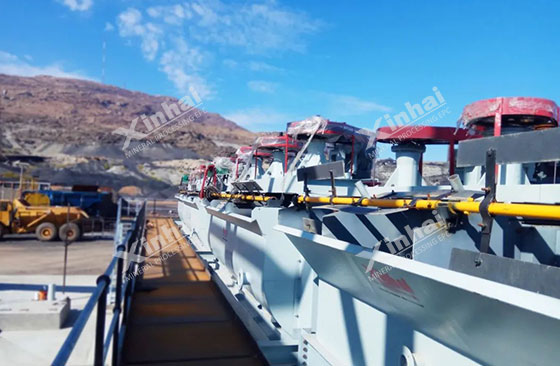
Roughing process: The first step of flotation process. During operation, it is necessary to ensure that the pulp is fully stirred to increase the contact opportunities between mineral particles and bubbles. The selection and dosage of reagents during roughing should be reasonable to avoid excessive foaming or mudification of pulp caused by excessive amount. Control the roughing time to prevent excessive floating of intergrowths caused by long flotation time.
Concentrating process: In order to further purify the foam products in roughing, appropriately increasing the number of times during concentrating can ensure the full removal of gangue minerals. By adjusting the bubble size and stirring speed of the flotation equipment during concentrating, the contact opportunities between mineral particles and bubbles can be optimized. The effect of mineral concentrating can be improved by using efficient inhibitors and collectors.
Scavenging process: Further flotation of roughing tailings can maximize the recovery of useful minerals in tailings and avoid resource loss. Appropriately extend the scavenging time during scavenging to ensure the full recovery of target minerals remaining in tailings. During scavenging, attention should also be paid to the control of slurry concentration and stirring speed to avoid particle agglomeration and mudification.
02Design elements of flotation process
The design of flotation process needs to comprehensively consider the physical and chemical properties of ore and production requirements. The following is a brief introduction to the design elements of flotation process:
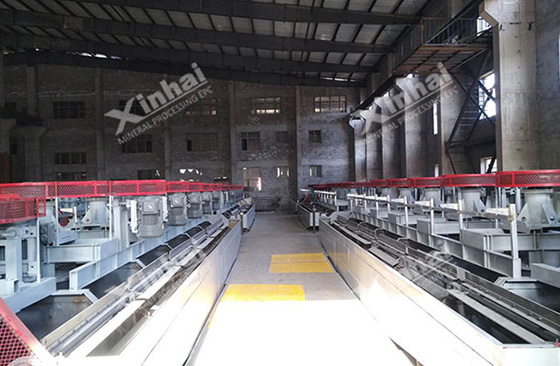
1. Ore impregnation particle size and symbiotic characteristics: The particle size distribution of the target mineral directly affects the selection of grinding and flotation process. When the particle size is coarse, one-stage flotation is sufficient. When the target mineral presents a fine particle distribution, a multi-stage flotation process is required for recovery.
2. Control the degree of ore mudification: Muddy ore will absorb reagents during flotation, thereby forming a large number of foam and adhesive particles, reducing the flotation effect. The effect of mudification can be reduced by setting a reasonable grinding process and reagent addition system.
3. Mineral composition and floatability analysis: Because the floatability of different minerals is different, the floatability of various minerals needs to be considered when designing the flotation process, and batch flotation process is required.
4. Consider the ore grade and oxidation degree: high-grade ores require a simplified flotation process, but ores with a high degree of oxidation have poor floatability and require a more complex process and the use of special reagents to improve the flotation process effect.
03Types and designs of flotation processes
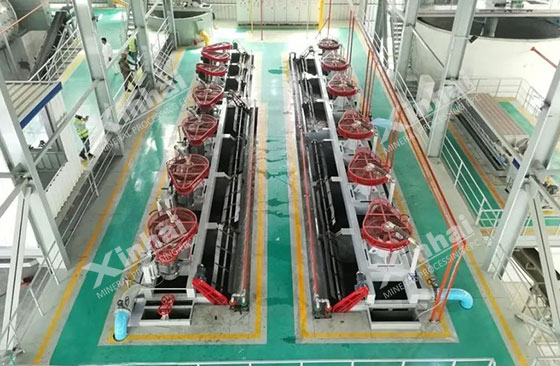
First stage flotation: ore is directly floated after grinding, and after roughing, it is subjected to concentrating and scavenging, and finally concentrate and tailings are obtained. When the impregnation particle size of useful minerals in the ore is uniform and there are few intergrowths, the first stage flotation process can be adopted.
Second stage flotation: After the first stage flotation, the tailings are ground and then enter the second stage flotation, which is used for ores with uneven impregnation of useful minerals. The low-grade concentrate obtained by the first stage flotation is floated after regrinding. This process is mainly used to treat ores impregnated with fine particles of useful minerals.
How to design the concentrating and scavenging process of flotation?
Concentration design: The number of flotation concentrating is determined according to the concentrate grade requirements, the original ore grade and the mineral floatability. When the grade requirements are high, the number of concentrating can be appropriately increased.
Scavenging design: The number of scavenging mainly depends on the recoverable mineral content and floatability in the tailings. When the content of useful minerals in the tailings is high, increasing the number of scavenging can reduce metal loss.
04Common flotation process problems and optimization measures
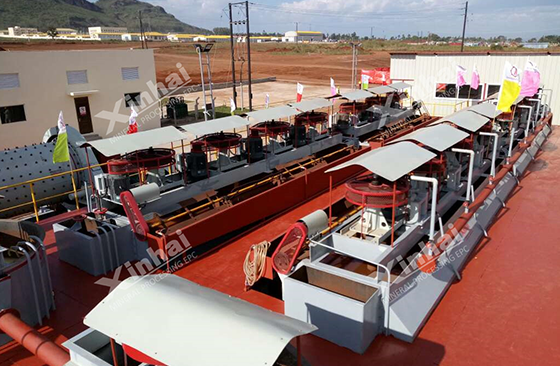
1. Too much middlings: adjust the number of cleaning times and optimize the return method of middlings.
2. The concentrate grade does not meet the standard: optimize the number of cleaning times and scavenging conditions, and adjust the speed and bubble size of the flotation equipment.
3. Large tailings loss: extend the scavenging time, increase the number of scavenging times and optimize the flotation reagent system.
How to optimize?
1. Selection and control of flotation equipment: select suitable flotation equipment according to mineral characteristics, adjust the speed, bubble size and pulp concentration.
2. Design and adjustment of reagent system: reasonably select the type and dosage of collectors, depressants and frothers.
3. Automation and intelligence of flotation process: realize automation and intelligence of flotation process through real-time monitoring and feedback of flotation control system.
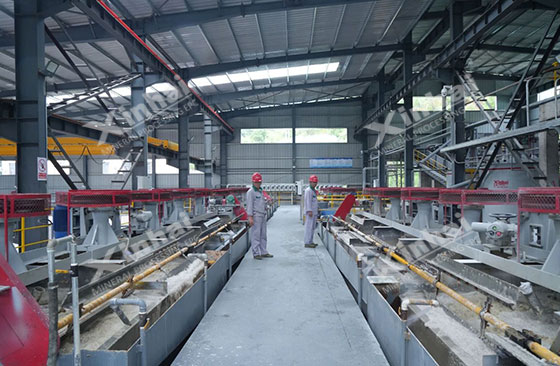
The above is a brief introduction to the design and optimization of flotation processes. In summary, the selection and design of flotation processes need to comprehensively consider the properties of ore, the requirements of concentration and scavenging, equipment selection and automation control. By rationally designing the flotation process and optimizing the flotation operation, efficient recovery of mineral resources can be achieved, and production costs and resource consumption can be reduced. Ore dressing plants can pay attention to the intelligence and automation of flotation processes to cope with complex and changeable mineral processing.