As a lighter metal in nature, lithium is also an element with strong electrochemical activity. Lithium products can be widely used in metallurgy, ceramics, battery and other industries. There are many types of lithium-containing minerals in nature. Among them, the lithium minerals with development value mainly include spodumene, lepidolite, lithium feldspar and spodumene. At present, spodumene has become a widely exploited lithium ore resource. Spodumene is mainly of the pegmatite type. In addition to spodumene, this type of ore also contains silicate minerals such as feldspar, quartz and mica. Commonly used spodumene beneficiation methods include flotation separation, magnetic separation, heavy liquid beneficiation and thermal cracking. The following mainly introduces you to the commonly used beneficiation methods of spodumene, flotation separation methods, new flotation technologies and flotation reagents used in flotation, to help you better understand spodumene flotation.
Use the table of contents below to navigate through the guide:
01Spodumene flotation separation method
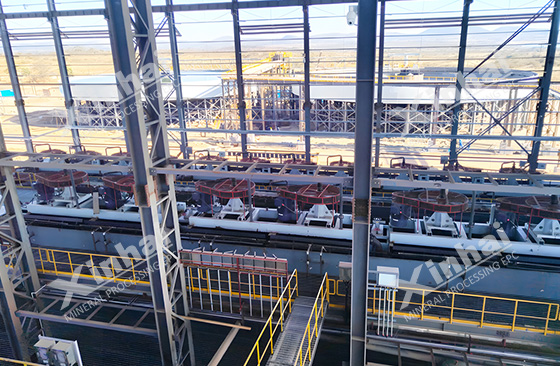
For the selection of pegmatite-type spodumene, flotation is often used at home and abroad, which can effectively separate spodumene from gangue minerals such as mica and feldspar. Spodumene flotation separation methods can be divided into two types: forward flotation and reverse flotation, but in general, the effect of forward flotation is better than reverse flotation. Spodumene positive flotation technology generally needs to be carried out in an alkaline environment, and fatty acids and soap collectors are used to recover foam products. The reverse flotation method needs to be carried out in an acidic environment, using amine collectors, starch and other inhibitors to prioritize gangue minerals such as feldspar and quartz, leaving spodumene and iron-containing minerals in the flotation tank. Within, flotation or magnetic separation methods are then used to separate out the iron-containing minerals, and the final residue is spodumene concentrate.
02New technology for spodumene flotation separation
Modern industry continues to develop, mineral processing technology is also constantly innovating, and methods applied to spodumene mineral processing are also emerging in endlessly. Since spodumene has the characteristics of easy weathering and high slime content, flotation column and stirring pretreatment and other processes can be used for spodumene separation, thereby improving the spodumene beneficiation effect.
(1) Application of flotation column in spodumene separation
Flotation columns are mainly used for the separation of fine-grained minerals. When applied to coarse-grained minerals with a particle size greater than 75 μm, it is often difficult to obtain good beneficiation indicators. Therefore, when using a flotation column to process spodumene, it is necessary to carry out a reasonable grinding process to reach the size of the ore required by the flotation column. When flotation column separation is performed on fine-grained spodumene, good results can be obtained, and the concentrate in the foam product has a finer particle size.
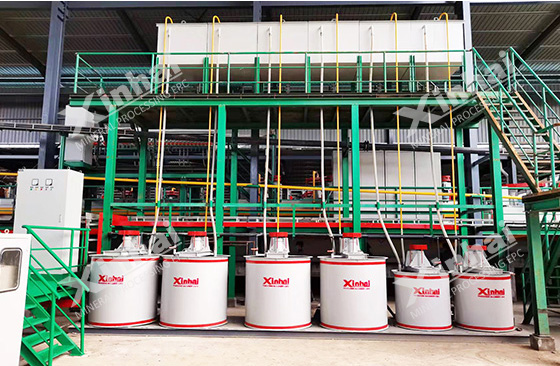
(2) Stirring pretreatment is used in spodumene selection
The stirring pretreatment method of spodumene is mainly carried out in a strong alkaline medium. By adding regulators and adjusting the stirring time and intensity, the fresh surface of the mineral is exposed and the surface properties of the mineral are changed, thereby facilitating the flotation of spodumene.
03Spodumene flotation separation reagent
During spodumene flotation, in order to obtain good beneficiation indicators, it is necessary to add appropriate chemicals to the slurry. The types of spodumene flotation agents usually added include amine collectors, fatty acid collectors, new collectors and regulators.
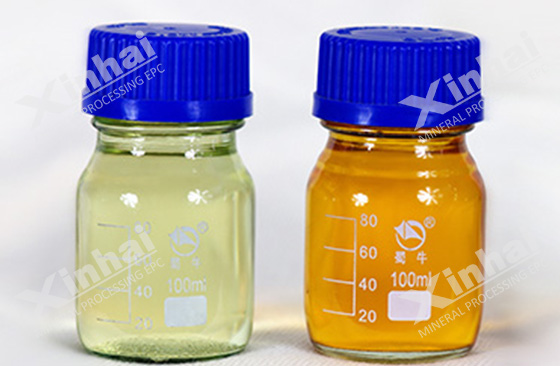
(1) Amine collector: one of the most commonly used collectors in silicate ore flotation. Spodumene mainly exists in granitic pegmatite deposits, and spodumene, quartz, feldspar and other gangue minerals are silicate minerals, so amine collectors have strong capture performance on these minerals.
(2) Fatty acid collectors: Fatty acid collectors commonly used in spodumene flotation mainly include sodium oleate, oxidized paraffin soap and naphthenic acid soap.
(3) New collectors: After years of research, spodumene beneficiation technology has been greatly improved. A lot of research and experiments have been done on the research of high-efficiency collectors for spodumene, and the separation effect has been developed. As well as collectors with good water solubility, oxamic acid is a chelating collector, which can use oxime to chelate based on the active ions on the mineral surface, thereby achieving a collection effect.
(4) Adjuster: The reagent system for spodumene flotation is generally "three bases and two soaps". The "three bases" are sodium carbonate, sodium sulfide and sodium hydroxide, and the two soaps are oxidized paraffin soap and naphthenic acid soap. In actual production, oxidized paraffin soap and naphthenic acid soap are used in large amounts. When used alone, their collection ability is not strong, and they are not easy to dissolve and disperse. Therefore, adjusters need to be added to the slurry to bind spodumene and suppress gangue minerals. Commonly used regulators for spodumene flotation include NaOH, CaCl2, Na2S and Na2CO3.
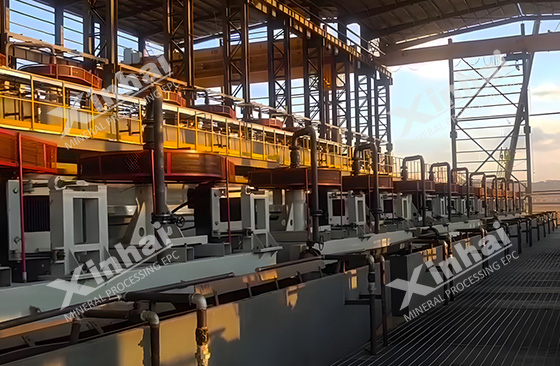
The above content is the spodumene flotation separation method, new flotation technology and flotation reagents. With the development of science and technology and continuous research, spodumene separation technology will gradually be updated and iterated. While considering improving the efficiency of mineral processing, the mineral processing plant can apply new mineral processing technologies to improve production efficiency, reduce production labor costs, and at the same time improve the overall mineral processing plant's efficiency. Automation facilitates the development of subsequent mineral processing plants. In addition, the rational planning of spodumene beneficiation technology should be based on the nature of the ore itself and the actual production requirements, and improve the production efficiency and economic benefits of the overall mineral processing plant by formulating a reasonable beneficiation process and arranging production equipment.