Iron is the main component of steel and an indispensable metal in industrial production. With the continuous development of the steel industry, the demand for iron metal is increasing year by year, which in turn leads to the demand for iron ore also rising year after year. Tailings are waste generated during the mineral processing process and are the main component of industrial solid waste. Due to the complexity of iron ore tailings' composition, if they are not properly treated, they will cause many hazards, such as land occupation, environmental pollution, safety hazards, etc. Therefore, reasonable recycling of iron tailings resources can not only improve the utilization rate of ore resources, but is also crucial to protecting the environment.
Use the table of contents below to navigate through the guide:
01Iron ore tailings classification
Iron ore tailings can be divided into magnetite tailings and hematite tailings according to the mineral properties of the raw ore. Due to the large displacement of magnetite, its production output is three times that of hematite, so the displacement of magnetite tailings is greater than that of hematite tailings. The yield ratio of hematite is high because it is more difficult to select than magnetite. A unit output of hematite will produce more tailings, making comprehensive iron ore tailings processing more difficult.
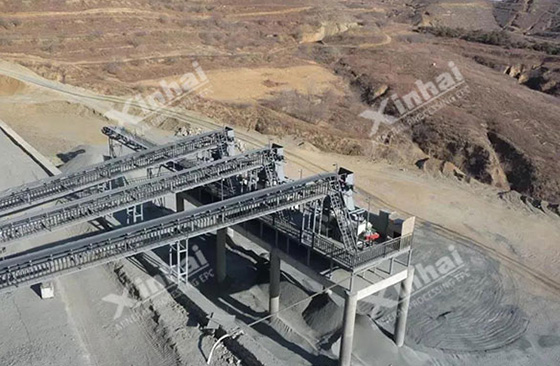
Iron tailings can be divided into five categories according to their chemical composition, namely: high silicon iron tailings, high aluminum iron tailings, high calcium magnesium iron tailings, low calcium magnesium aluminum silicon iron tailings and polymetallic iron tailings.
(1) High silicon iron tailings: high silicon content, fine particle size, and no valuable associated elements. The content of silicon dioxide is more than 70%. Most of the tailings are silicate minerals, such as quartz and chlorite. Stone, hornblende, mica, feldspar, etc.
(2) High-aluminum iron tailings: relatively small displacement, high alumina content, and generally do not contain associated elements and components. Some tailings associated minerals contain phosphorus and sulfur at a constant rate. It also contains minerals such as feldspar, mica, kaolin, chlorite, apatite and pyrite.
(3) High-calcium-magnesium iron tailings: In addition to high calcium and magnesium content, this type of tailings is also associated with sulfur and cobalt. This type of ore contains minerals such as diopside, dolomite, feldspar, pyrite, and chalcopyrite.
(4) Low calcium magnesium aluminum silicon iron tailings: the particle size is generally less than 0.074mm, accounting for about 70%. Elements such as silica, calcium, and magnesium are low in tailings, and minerals such as barite, phyllite, olivine, and jasper are common in the ore.
(5) Polymetallic iron tailings: This kind of tailings has a relatively complex composition and many associated elements. In addition to containing a large amount of non-ferrous metal elements, it also contains recyclable rare metals and precious metal elements.
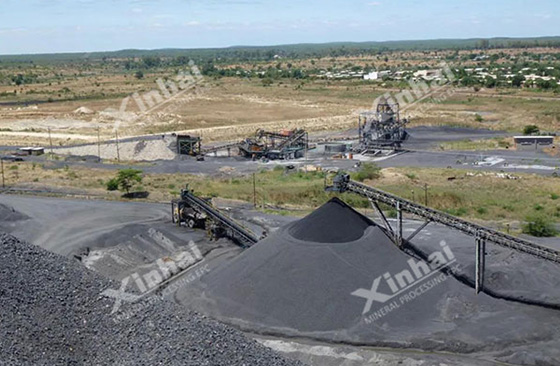
02Comprehensive utilization method of iron ore tailings
The comprehensive utilization of iron ore tailings is mainly divided into four aspects: tailings filling, plant reclamation, tailings reprocessing and manufacturing of building materials and new materials.
(1) Tailings filling: When tailings filling is carried out in the concentrator, it mainly goes through four processes: solid-liquid separation, cementing agent addition, slurry filling and filling body oxidation.
(2) Plant reclamation: Reclamation and soil modification using iron tailings as the main soil material.
(3) Iron tailings reprocessing: One of the main methods for reusing iron tailings is to re-select valuable minerals from iron tailings. The types of valuable minerals in different types of iron tailings are different, so it is necessary to adopt different mineral separation methods, such as magnetic separation, gravity separation, flotation and roasting, are used for recovery.
(4) Manufacturing building materials and new materials: tailings are used as the main raw materials to produce bricks, cement, crystallized glass, ceramic materials, decorative materials and wall coatings, etc.
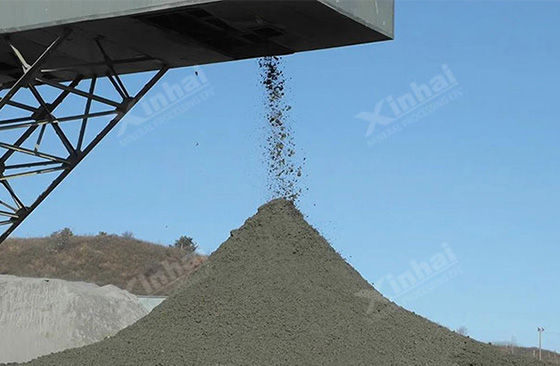
The above content is the classification of iron ore tailings and methods of comprehensive utilization. Reasonable utilization of iron tailings can improve the environment around the mineral processing plant. However, the chemical composition and mineral properties of the tailings need to be identified to determine whether they have reprocessing value. If it has re-selection value, the valuable components should be separated first, thereby improving the utilization rate of iron tailings resources. Therefore, Xinhai Mining recommends conducting mineral processing test analysis, determining the mineral processing plan and equipment configuration based on the test results, improving the working efficiency of the mineral processing production line, and obtaining higher economic benefits.