Quartz is a naturally occurring silicon dioxide mineral that is abundantly
found in Earth's crust and is the second most common mineral after feldspar.
Quartz deposits can be classified into two types: rock crystal (primary ore) and
placer deposits (secondary ore). After mining, quartz must be processed and
purified before it can be used in industrial production. This article introduces the uses of quartz , the processes of quartz mining, quartz processing, and purification.
Use the table of contents below to navigate through the guide:
01Uses of Quartz
Quartz has a wide range of uses, covering multiple fields such as industry,
technology, construction and jewelry. It can be classified into four categories
according to purity requirements:
1. Ordinary grade: SiO₂ content 85%~95%, used for concrete
and ordinary glass manufacturing.
2. Medium-high purity: SiO₂ content 95%~99.9%, used for
artificial quartz stone, ceramic glaze, etc., requiring Fe₂O₃<0.1%.
3. High purity: SiO₂ content 99.9%~99.99%, used for
semiconductors and photovoltaics, requiring total impurities <100ppm.
4. Special grade: used for jewelry and optical
instruments.
Ordinary grade quartz sand only needs simple sorting after mining, with low
processing difficulty and low cost. High-purity quartz sand requires complex
purification after mining, which is difficult and costly.
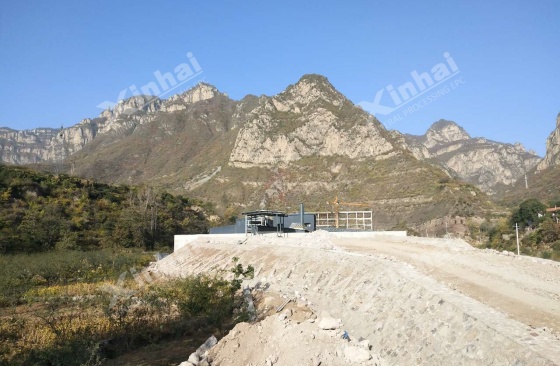
02Quartz mining
1.Open-pit mining: Suitable for extracting quartz from sand
deposits or shallow quartz veins.
Process: Removal of overburden → excavation using shovels and heavy machinery
→ sand deposits require screening and washing to remove clay and impurities.
Advantages: Cost-effective, highly efficient, and well-suited for large-scale
production.
2.Underground mining: Suitable for extracting deep-seated
quartz crystals or high-purity quartz deposits.
Process: Drilling and blasting → manual sorting to preserve high-value
crystals → quartz is transported to the surface using mine carts or conveyor
belts.
Challenges: High operational costs and significant safety risks.
3.Seabed/riverbed mining: Primarily used for extracting
quartz sand.
Process: Dredgers are used to extract sand deposits from the seabed or
riverbed → hydraulic separation is employed to separate quartz sand from
silt.
Challenges: May cause ecological damage to the seabed, necessitating strict
regulatory oversight.
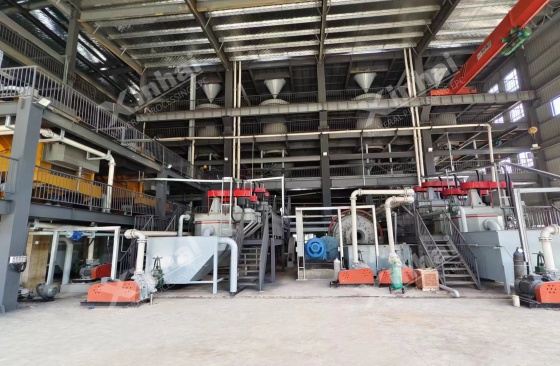
03Quartz processing and purification
1. Crushing and Grinding
Quartz is first crushed to an appropriate particle size for subsequent
sorting. First, a jaw crusher or cone crusher is used to perform coarse and
intermediate crushing, followed by an impact crusher or ball mill for fine
crushing or grinding. Next, a vibrating screen is used to
classify the material by particle size (e.g., 0.1–0.5 mm for glass sand, 1–3 mm
for building materials).
2. Sorting
After being crushed to an appropriate particle size, quartz undergoes
sorting. Sorting aims to separate quartz from associated minerals, such as
feldspar, mica, and iron-bearing minerals. Various sorting techniques are
employed depending on the type of associated minerals:
Magnetic separation: Used to remove magnetic impurities,
such as magnetite. It works by exploiting the magnetic differences between
quartz and impurities, with a magnetic separator removing
these impurities.
Flotation: Flotation works by modifying the mineral surface
properties using flotation reagents, applying agitation and air bubbles to cause
target minerals to attach to air bubbles, thereby separating quartz from gangue
minerals such as mica and feldspar. Common froth flotation process include direct
(positive) flotation and reverse flotation.
Gravity separation: Gravity
separation works by exploiting the density differences between gangue
minerals and quartz to achieve separation. This method is effective in removing
heavy minerals such as garnet and ilmenite. Typical gravity separation equipment
includes shaking tables, spiral chutes, and jigs.
After sorting, the SiO₂ purity of quartz can reach 99.99%, making it suitable
for most industrial applications.
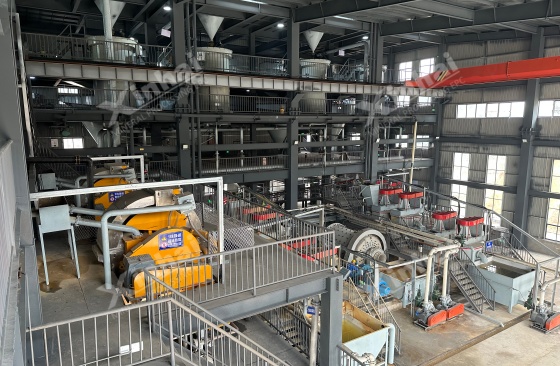
3. Purification
For applications requiring ultra-high purity, such as the semiconductor and
photovoltaic industries, quartz must undergo additional purification. The
primary purification method used in this process is acid leaching. Acid leaching
works by utilizing hydrochloric acid (HCl) or hydrofluoric acid (HF) to dissolve
metallic impurities, followed by high-temperature chlorination and water
quenching for further purification.
4. Deep Processing
Depending on its final application, quartz undergoes further processing.
Common deep processing methods include:
Drying: This process reduces moisture content. For instance,
glass sand must have a moisture content below 0.5%.
Grinding: Quartz is ground into fine powder using a Raymond
mill, making it suitable for use in coatings and fillers.
Fused Quartz: High-purity quartz glass is produced by
melting quartz at temperatures above 2000°C.
Preparation of Single-Crystal Silicon: High-purity quartz is
refined into metallurgical-grade silicon, which is subsequently purified into
single-crystal silicon ingots used in chip manufacturing.
Coating Treatment: This process enhances light transmittance
or wear resistance, making quartz suitable for applications such as UV
lenses.
5. Tailings Treatment
After quartz extraction, purification, and further processing, residual
tailings remain. The proper management of these tailings is a critical
environmental concern. Tailings can be dehydrated using tailings dry
stacking technology and then either backfilled into mining pits or
transported to tailings ponds. The location of tailings ponds should be situated
far from residential areas and must undergo anti-seepage treatment to prevent
environmental contamination.
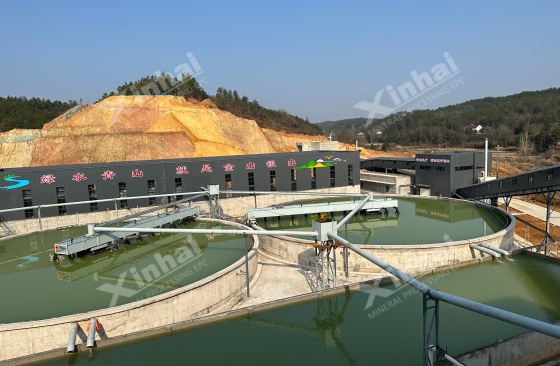
Conclusion
Quartz mining and processing still present several challenges. How can higher
purity be achieved? How can quartz processing become more environmentally
friendly? How can intelligent automation and other advanced technologies be
better integrated into quartz processing? These are critical issues worth
exploring and key directions for future advancements.
04Xinhai Mining: A Leading Quartz Mining Company
Xinhai Mining is a Chinese company with extensive experience in mining
contracting and construction. We provide customers with comprehensive services,
including process design, engineering construction, and tailings management for
mining and mineral processing projects.
Our international business spans over 100 countries and regions across Asia,
Africa, and South America, where we have successfully completed numerous mining
construction projects. In the field of quartz sand mining and processing, Xinhai
has undertaken dozens of projects worldwide.
With extensive industry expertise, a well-established service process,
top-tier equipment quality, and the integration of intelligent automation, we
maintain a strong competitive edge in the market. If you have business inquiries
related to quartz mining, feel free to contact us.