As an important industrial raw material, quartz sand processing and separation technology has important application value in modern industry. The selection of quartz ore beneficiation technology needs to be based on the differences in physical and chemical properties between quartz and its associated minerals and other mineral impurities, including hardness, magnetism, solubility and floatability. The following will introduce you to the four operations of quartz grinding classification, magnetic separation, pickling and flotation to discuss quartz sand beneficiation technology.
Use the table of contents below to navigate through the guide:
01Quartz sand grinding and grading operation
Since the hardness of quartz in silica resources is relatively high, while the hardness of associated minerals such as feldspar and mica is relatively low. Based on this characteristic, selective grinding can effectively separate quartz and other gangue minerals. During the grinding process, the quartz particles with higher hardness should be kept at a larger particle size, while the minerals with lower hardness are easily ground into fine particles, and then separated through grading operations.
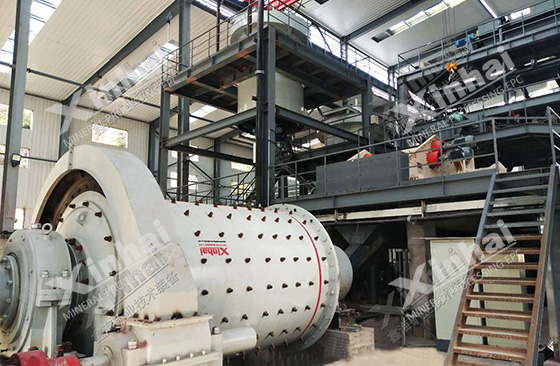
The selective grinding operation of quartz ore can be divided into dry and wet types. Dry grinding can use airflow self-grinding equipment, and wet grinding can use self-grinding, ore washing and ball milling equipment. These two grinding processes have their own advantages. Dry grinding can reduce the use of water resources, while wet grinding has certain advantages in grinding efficiency and product quality.
When feldspar is associated with quartz ore, it should be noted that the hardness of feldspar and quartz is close, and it is difficult to separate these two minerals by selective grinding alone.
02Quartz sand magnetic separation operation
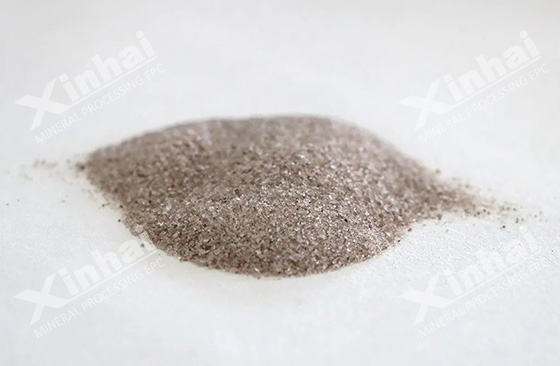
Magnetic separation can be used to remove iron impurities from minerals. During the purification process of quartz, both strong magnetic impurities and weak magnetic impurities can be effectively removed by magnetic separation. Production practice has proven that when the magnetic field intensity is set at 1800~2200 kA/m, the magnetic separation effect is the best. Multiple magnetic separation processes can effectively further reduce the iron impurity content, but when the iron removal rate reaches a certain level, continuing to increase the magnetic field intensity will not have an obvious iron removal effect. Through the magnetic separation process, the purity of quartz can be significantly improved, laying the foundation for subsequent pickling and flotation processes.
03Quartz sand pickling operation
The pickling operation of quartz ore is a key step in purification. It mainly utilizes the characteristic of quartz being insoluble in acid (except hydrofluoric acid) to dissolve impurity minerals in silica through acid. Impurity minerals in silica exist in the form of inclusions or attachments. Pickling can effectively remove these impurities and significantly improve the quality of silica. Commonly used pickling methods include dynamic pickling and static pickling. Commonly used acid types include hydrochloric acid, sulfuric acid, nitric acid and hydrofluoric acid.
The pickling process requires reasonable selection of acid concentration, temperature and pickling time. Increasing the temperature and extending the pickling time can effectively improve the impurity removal rate, but the waste liquid generated during the pickling process needs to be treated to meet standards before being discharged. Acid recovery and comprehensive utilization technologies can be used to reduce environmental pollution.
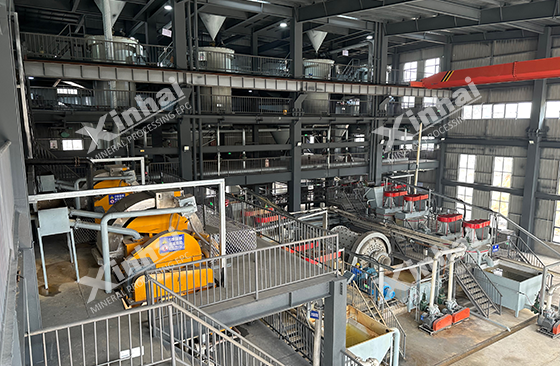
04Quartz sand flotation operation
Flotation is the key process for quartz purification. Quartz flotation can be divided into two methods: foam reproduction and full oil flotation. The flotation process requires reasonable control of particle size, pulp concentration and flotation reagents, all of which will affect the flotation effect of quartz. When the ore particle size is too large, the bubbles cannot be effectively carried, while if the ore is too small, the quality of the flotation product will be affected. The pulp concentration should be reasonably controlled between 35% and 40%, at which time the flotation effect is best. Selecting appropriate collectors, inhibitors and frothers according to the mineral properties of the quartz ore can effectively improve the sorting efficiency and the recovery rate of the target mineral.
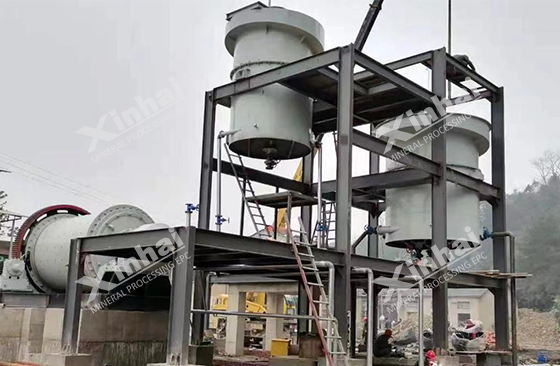
In summary, quartz sand beneficiation technology has important application value in modern industry, and its process flow includes key steps such as grinding and classification, magnetic separation, pickling and flotation. By scientifically and rationally selecting and optimizing these process parameters, impurities can be removed efficiently, the purity and product quality of quartz can be improved, thereby meeting the needs of different industries for high-quality quartz. At the same time, in order to achieve green environmental protection and sustainable development, each process link should focus on resource utilization efficiency and waste treatment, and further promote the progress and innovation of quartz sand beneficiation technology.