Quartz sand is one of the important raw materials in industry and is widely used in glass, ceramics, metallurgy and other industries. The production of high-purity quartz sand places strict requirements on its beneficiation process. This paper will systematically explore the key factors affecting the quartz sand beneficiation process from the aspects of process mineralogy research, grinding fineness, desludging, magnetic separation, flotation test research and acid leaching test research, and propose optimization strategies.
Use the table of contents below to navigate through the guide:
01Research on process mineralogy of quartz sand
Process mineralogy research is the basis of mineral processing technology design. Through the study of the mineral composition and impurity occurrence state of the original ore, the embedding characteristics, shape, size, relationship with gangue minerals and spatial distribution of the main minerals, the distribution, size and type of fluid inclusions in quartz particles, it can provide an important basis for the formulation of subsequent mineral processing technology.
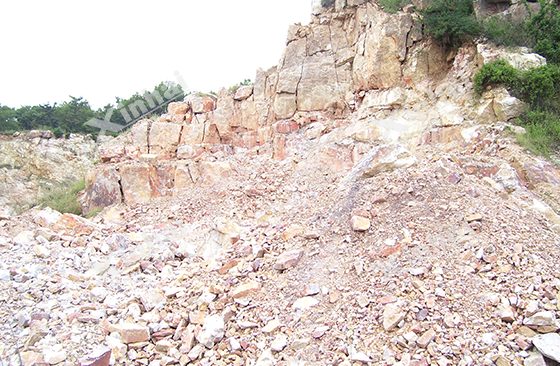
Mineral composition and impurity occurrence state of the original ore
First of all, the mineral composition and impurity occurrence state of the original ore are the key to determining the mineral processing method and process flow. The chemical and physical properties of different minerals vary greatly, and it is necessary to select a suitable mineral processing method according to the specific situation. For example, common impurity minerals in quartz sand include iron minerals, feldspar, mica, etc. These minerals need to be removed by different methods in different mineral processing links.
Mineral embedding characteristics, shape, size and spatial distribution
Secondly, the embedding characteristics, shape, size and relationship with gangue minerals and spatial distribution of the main minerals directly affect the grinding and beneficiation effects. The size and shape of the quartz particles in quartz sand and their symbiotic relationship with impurity minerals determine the difficulty of grinding and the choice of grinding fineness. For example, if the quartz particles are large and closely symbiotic with impurity minerals, finer grinding is required to achieve the dissociation effect.
Characteristics of fluid inclusions in quartz particles
Finally, the distribution, size and type of fluid inclusions in quartz particles affect the selection of beneficiation technology. The presence of inclusions may affect the purity of quartz sand, so in the beneficiation process, it is necessary to consider how to remove or reduce the impact of these inclusions on the quality of the final product.
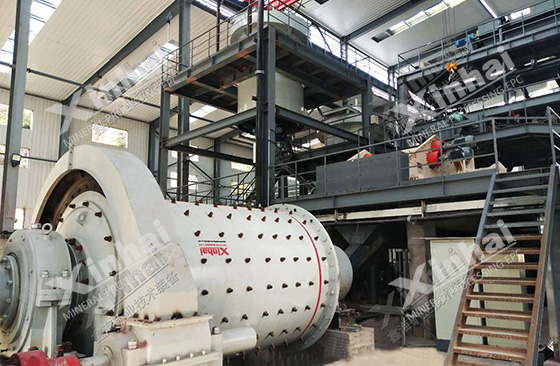
02Quartz sand grinding fineness
Grinding fineness is a key link in the mineral processing process and directly affects the subsequent mineral processing effect. According to the characteristics of the original ore and the requirements of the concentrate, it is very important to determine the reasonable grinding method and grinding fineness.
Choice of grinding method: Different grinding methods such as ball milling and rod milling have different effects on grinding fineness and mineral dissociation. It is necessary to select appropriate grinding equipment and methods according to the physical properties of the main minerals and impurity minerals in quartz sand.
Determination of grinding fineness: The selection of grinding fineness should be aimed at achieving full dissociation of minerals, while avoiding waste of resources and unnecessary energy consumption caused by excessive grinding. Usually, the optimal grinding fineness is determined by combining laboratory grinding tests and mineral processing tests.
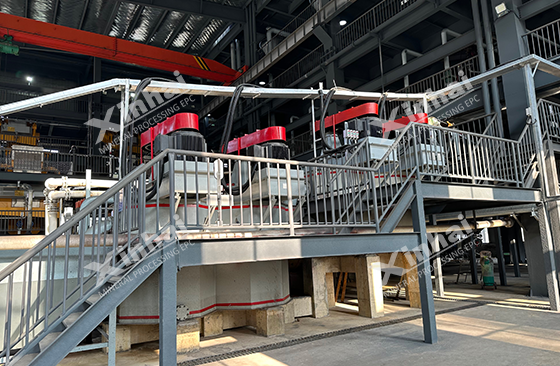
03Quartz sand desludging process
Desludging is an important part of the mineral processing process. Through sedimentation and classification desludging, the appropriate desludging particle size lower limit can be determined, which can effectively remove fine mud in the slurry and improve the quality of the concentrate.
The selection of desludging particle size directly affects the desludging effect and the overall efficiency of the mineral processing process. It is necessary to determine the optimal desludging particle size lower limit through experimental research to improve the desludging efficiency while ensuring the quality of the concentrate.
04Quartz sand magnetic separation
Magnetic separation is an effective method to remove iron impurities from quartz sand. Exploring the effects of different magnetic field intensities, slurry flow rates, and magnetic media on the iron removal effect can provide a basis for the optimization of the magnetic separation process.
The influence of magnetic field intensity: Magnetic field intensity is a key parameter in the magnetic separation process, and different magnetic field intensities have different effects on the removal of iron impurities. Through experimental research, the optimal magnetic field intensity can be determined to achieve the best iron removal effect.
Selection of slurry flow rate and magnetic medium: Appropriate slurry flow rate can improve the efficiency of magnetic separation, while different types of magnetic media can affect the accuracy and effect of magnetic separation.
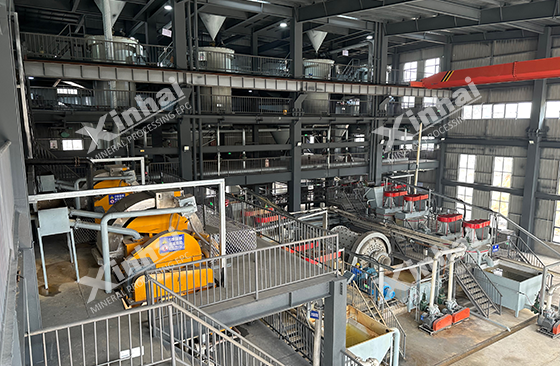
05Quartz sand flotation process
Flotation is one of the commonly used methods in quartz sand beneficiation. By adjusting the type and dosage of collectors and depressants, the quality of the concentrate can be effectively improved.
Selection and dosage of collectors: Through experimental research on different anion and cation collector combinations and their ratios, the best collector solution can be found to improve the purity of flotation concentrate.
Dosage of depressants: The right amount of depressants can inhibit the flotation of impurity minerals and improve the purity of quartz sand. Through experimental research, the best dosage of depressants can be determined.
06Quartz sand acid leaching process
Acid leaching is one of the effective methods to improve the purity of quartz sand. Exploring the effects of acid types, mixed acid combinations, acid leaching temperature, acid leaching time, and fluorine-free acid leaching on the quality of concentrate can provide a basis for the optimization of the acid leaching process.
Acid types and mixed acid combinations: Different acid types and mixed acid combinations have different dissolution effects on impurity minerals in quartz sand. Through experimental research, the best acid type and mixed acid combination can be determined to achieve the best acid leaching effect.
Acid leaching temperature and time: Acid leaching temperature and time are important factors affecting the acid leaching effect. Appropriate acid leaching temperature and time can increase the dissolution rate and dissolution amount of impurity minerals, thereby improving the purity of the concentrate.
The effect of fluorine-free acid leaching: Fluoride and non-fluoride acid have different effects on quartz sand during the acid leaching process. Through experimental research, it can be determined whether fluoride needs to be added and the concentration of addition to optimize the acid leaching effect.
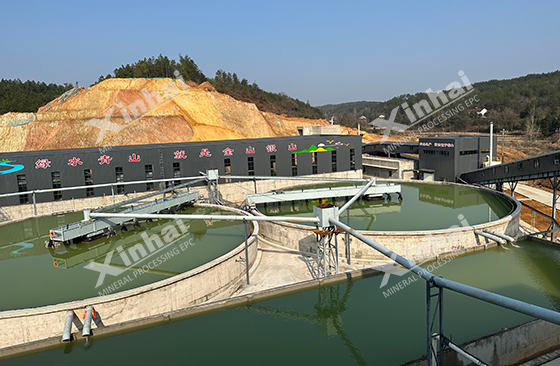
The optimization of quartz sand beneficiation technology is a complex process that requires comprehensive consideration of multiple factors such as process mineralogy research, grinding fineness, desludging, magnetic separation, flotation and acid leaching. Through systematic experimental research and process optimization, the purity of quartz sand can be improved to meet the needs of industrial production.