As one of the most widely used mineral processing methods, flotation plays an important role in mineral separation and recovery. The complexity of the flotation process determines that there are many issues and influencing factors involved in its research field, covering all aspects from ore characteristics to process control. This article will explore these influencing factors in depth and analyze their specific impact on the flotation process and separation effect, in order to provide a scientific basis for improving flotation efficiency and mineral resource utilization.
Use the table of contents below to navigate through the guide:
01Objective factors affecting the flotation process
Objective factors are usually determined by external conditions and are difficult to change through human means, but they have a significant impact on the flotation effect.
Ore characteristics
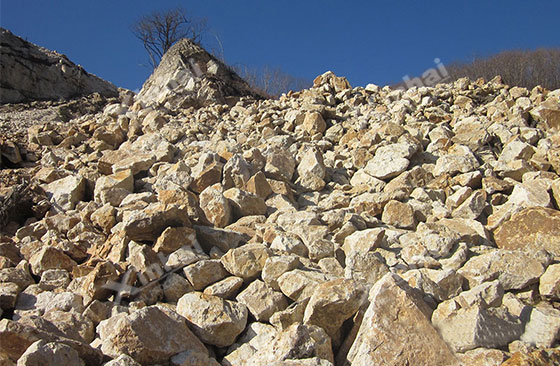
The particle size distribution of the ore, the crystal structure of the mineral, the chemical properties of the mineral surface, etc. will affect the adsorption of the flotation reagent and the flotation behavior of the mineral. In addition, the content and type of harmful impurities in the ore will also have an adverse effect on the flotation effect. For example, sulfur-containing minerals are easily oxidized to form sulfuric acid during the flotation process, which not only affects the pH value of the ore pulp, but may also form highly inhibitory sulfate ions, resulting in a decrease in the flotation effect.
Water composition
The composition of water in the ore pulp includes dissolved salts, suspended solid particles, organic matter and other components that affect the effect of flotation reagents. Calcium and magnesium ions in the water will react with the flotation reagents to form insoluble precipitates, reduce the effective concentration of the reagents, and thus affect the flotation effect. In addition, organic matter in the water, such as humus and algae, will also affect the adsorption efficiency of the reagents by competing with the adsorption on the mineral surface. During the flotation process, the dosage and type of reagents need to be adjusted according to the specific conditions of the water quality to ensure the stability of the flotation effect.
Ambient temperature
The influence of temperature on the flotation process is mainly reflected in two aspects: on the one hand, temperature affects the viscosity and fluidity of the slurry, which in turn affects the dispersion of mineral particles and the diffusion rate of flotation reagents. When the temperature rises, the viscosity of the slurry will decrease, which is conducive to the dispersion of mineral particles and the diffusion of reagents, thereby improving the flotation efficiency. On the other hand, temperature will also affect the chemical reaction rate of flotation reagents and the chemical properties of the mineral surface. For example, some flotation reagents react slowly at low temperatures, and the reaction rate needs to be accelerated by increasing the temperature to achieve the desired flotation effect.
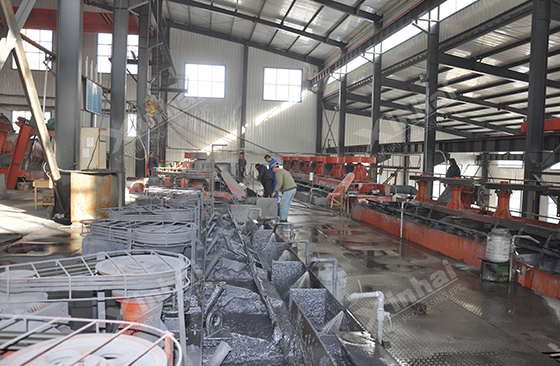
02Operating factors affecting the flotation process
The operating factors in the flotation process also have a significant impact on the separation effect. Operating factors are key variables that can be adjusted and controlled to optimize the flotation process.
Grinding fineness
Grinding fineness directly affects the size and specific surface area of mineral particles, which in turn affects the adsorption of flotation agents and the flotation behavior of minerals. Generally speaking, the finer the grinding fineness, the larger the specific surface area of mineral particles, which is conducive to the adsorption of flotation agents and improves the floatability of minerals. However, too fine grinding fineness will lead to excessive dispersion of mineral particles, increase the viscosity of the slurry, and be unfavorable to the formation of flotation foam and the separation of mineral particles. Therefore, it is necessary to select the appropriate grinding fineness according to the specific characteristics of the ore and the flotation requirements to achieve the best flotation effect.
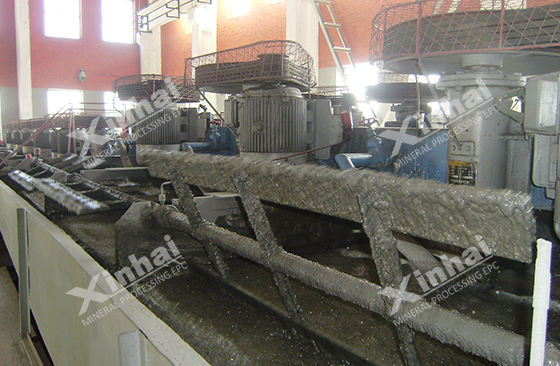
Pulp concentration
Pulp concentration refers to the mass of solid minerals contained in a unit volume of pulp. If the pulp concentration is too high, it will lead to increased collision and agglomeration between mineral particles, which is not conducive to the formation and stability of flotation foam, thus affecting the flotation effect. If the pulp concentration is too low, it will reduce the processing capacity of the flotation equipment and increase the consumption of flotation reagents. Therefore, it is necessary to reasonably control the pulp concentration according to the characteristics of the ore and the performance of the flotation equipment to ensure the smooth progress of the flotation process.
pH value of ore pulp
The pH value of ore pulp not only affects the dissociation and equilibrium state of flotation reagents, but also affects the potential and chemical properties of the mineral surface. The reactivity of different types of minerals to flotation reagents varies under different pH conditions. For example, sulfide minerals are easier to float under acidic conditions, while oxidized minerals float better under alkaline conditions. Therefore, during the flotation process, the pH value of the ore pulp needs to be adjusted according to the type of mineral and the characteristics of the flotation reagent to optimize the flotation effect.
Reagent system
The reagent system includes the type, dosage, order and time of addition of reagents. The type and dosage of reagents directly affect the effect of flotation reagents. For example, the type and dosage of collectors determine the floatability of minerals, the type and dosage of frothers determine the nature and stability of foams, and the type and dosage of regulators determine the pH value of pulp and the chemical properties of mineral surfaces. Therefore, in the flotation process, it is necessary to select the appropriate type and dosage of reagents according to the specific characteristics of the minerals, and reasonably arrange the order and time of adding reagents to achieve the best flotation effect.
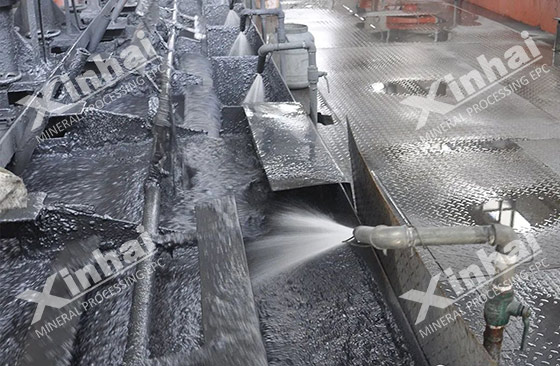
Slurry mixing time and intensity
Slurry mixing time refers to the pretreatment time of the slurry before flotation, and slurry mixing intensity refers to the stirring intensity of the slurry during the slurry mixing process. The selection of slurry mixing time and intensity directly affects the dispersion of mineral particles and the adsorption of flotation reagents. For example, appropriate slurry mixing time and intensity are conducive to the uniform distribution of flotation reagents and the full dispersion of mineral particles, thereby improving the flotation effect; while too long slurry mixing time and too strong slurry mixing intensity will lead to excessive dispersion of mineral particles and excessive consumption of reagents, which is not conducive to flotation. Therefore, it is necessary to select appropriate slurry mixing time and intensity according to the specific characteristics of the ore and the requirements of the flotation process to optimize the flotation process.
Stirring intensity and aeration volume of flotation machine
Stirring intensity and aeration volume directly affect the formation and stability of flotation foam. If the stirring intensity is too high, the collision and agglomeration of mineral particles will increase, which is not conducive to the formation and stability of flotation foam; if the stirring intensity is too low, the mineral particles will be insufficiently dispersed, reducing the flotation efficiency. Similarly, if the aeration volume is too high, the flotation foam will be too rough, which is not conducive to the attachment and separation of mineral particles; if the aeration volume is too low, the flotation foam will be insufficient, affecting the flotation efficiency. Therefore, it is necessary to reasonably control the stirring intensity and aeration volume according to the specific characteristics of the ore and the performance of the flotation equipment to ensure the smooth progress of the flotation process.
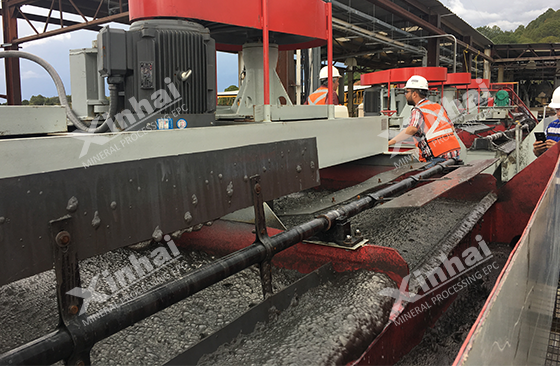
Flotation time
Flotation time is another important operating parameter that affects the flotation process. Flotation time refers to the processing time of the slurry in the flotation machine. If the flotation time is too short, the flotation of mineral particles will be insufficient, affecting the flotation effect; if the flotation time is too long, it will lead to excessive consumption of flotation reagents and re-sedimentation of mineral particles, which is not conducive to flotation. Therefore, it is necessary to select the appropriate flotation time according to the specific characteristics of the ore and the flotation process requirements to optimize the flotation process.
To sum up, flotation is a complex mineral separation method, and its separation effect is affected by many factors. Changes in these factors will have a significant impact on the flotation process and separation effect. Therefore, during the flotation process, it is necessary to scientifically and reasonably control various operating parameters according to the specific characteristics of the ore and the requirements of the flotation process to optimize the flotation effect and improve the utilization rate and economic benefits of mineral resources.