In recent years, with the rapid development of electric vehicles and portable electronic devices, the demand for lithium batteries has also increased year by year. As an ore rich in lithium, the development and utilization of lepidolite has also received widespread attention. Lepidolite is commonly found in porphyry mines, and one of the commonly used mineral processing methods is flotation technology. Flotation of lepidolite is a complex process. Understanding its flotation technology, equipment and technical difficulties is one of the ways to optimize lepidolite flotation technology. The following will introduce you to the lepidolite flotation process from these three aspects.
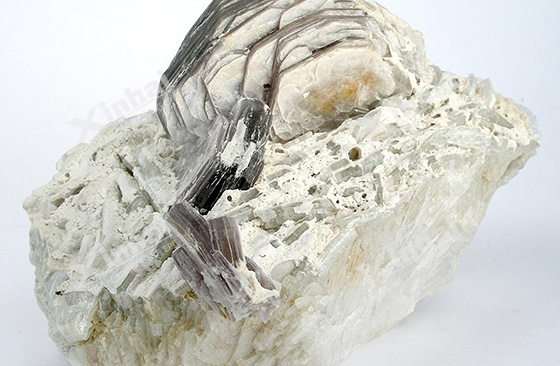
(Lepidolite ore)
Use the table of contents below to navigate through the guide:
01Lepidolite ore flotation technology
Flotation technology plays a very important role in extracting lithium from lepidolite. Before flotation, lepidolite ore will enter the crushing equipment and grinding equipment for crushing and grinding to reduce the particle size and make it suitable for the flotation process. During flotation, the treated ore is mixed with water and certain chemicals, and air is blown or filled into the flotation machine. Since the lepidolite particles are hydrophobic and other minerals are hydrophilic, the lepidolite particles will adhere to the surface of the foam. As the foam floats on the surface of the liquid, it is skimmed off by the scraper. The enriched lepidolite concentrate needs to be further concentrated and dehydrated, and finally sent to the concentrate storage for storage.
Flotation reagents are required during lepidolite ore flotation, usually collectors, frothers and regulators. The main function of the collector is to attach to the surface of lepidolite particles and make them hydrophobic. Foaming agents primarily help create and stabilize foam. The regulator is mainly used to improve the selectivity of chemical substances in the flotation process and ensure the lepidolite flotation effect.
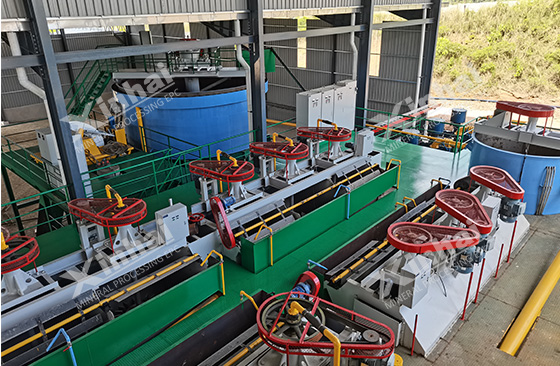
(flotation equipment)
02Lepidolite ore beneficiation equipment
In order to improve lepidolite ore beneficiation efficiency and concentrate recovery rate, it is crucial to select specialized beneficiation equipment. The equipment used for lepidolite mineral processing equipment mainly includes pre-flotation equipment, flotation equipment and flotation post-treatment equipment.
Equipment before flotation: The pretreatment equipment before lepidolite ore mainly includes crushing equipment, screening equipment, grinding equipment and classification equipment.
Crushing equipment mainly includes jaw crusher and cone crusher. Jaw crusher is mainly used for the primary crushing of lepidolite, breaking down large pieces of lepidolite into smaller particles. The diameter of the particles is generally between 150mm-300mm. Spring cone crusher is mainly used for medium and fine crushing of lepidolite. It can reduce the particle diameter of ore to between 20mm-50mm.
Screening equipment mainly includes vibrating screening machines and high-frequency screening machines. Vibrating screens are often used for preliminary screening to separate larger lepidolite ore particles and return them to the crushing system for re-crushing. High-frequency screening machines are mainly used to process finer particles, and finer particle distribution can be obtained through screening.
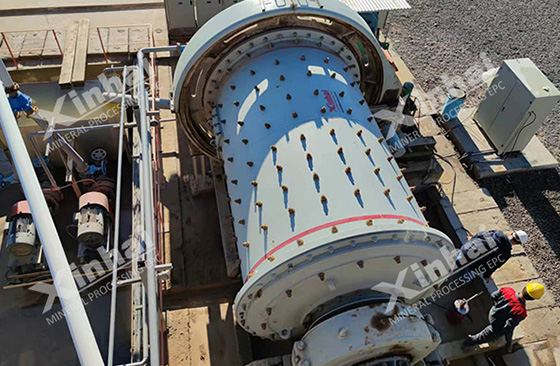
(Grinding equipment)
The grinding equipment mainly uses ball mills and rod mills. Due to different grinding media, these two types of equipment process different ore particle sizes. Generally, rod mills are mainly used for rough grinding and processing of larger ore particles. The selection of appropriate grinding equipment should be based on the characteristics of the ore and process requirements. Properly arranging the grinding process can obtain the required particle size distribution, reduce energy consumption and equipment wear, and improve the overall mineral processing efficiency.
Flotation equipment mainly includes mechanical flotation machines, inflatable flotation machines, rod flotation machines and other types. Mechanical agitation flotation machines are commonly used for lepidolite flotation. Through stirring and aeration, bubbles are generated, and lepidolite particles adhere to these bubbles and rise to the liquid surface for easy collection. Choosing appropriate flotation equipment and flotation reagents can effectively improve the overall flotation efficiency and flotation concentrate quality.
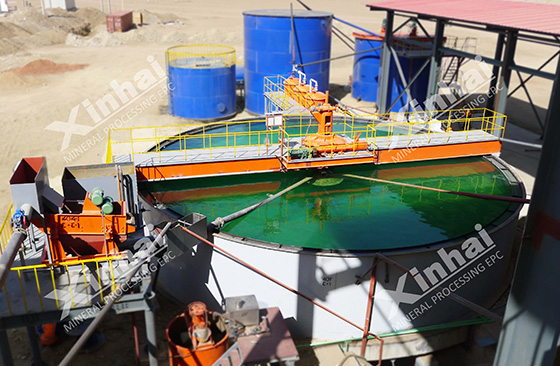
(Thickener)
The processing equipment after flotation mainly includes a thickener and a dehydrator, which are used to concentrate and dehydrate the lepidolite concentrate for flotation to further improve the grade and quality of the concentrate. The main types of thickeners include: high-efficiency thickeners, high-efficiency modified thickeners, peripheral roller drive thickeners, hydraulic center drive high-efficiency thickeners, etc. The main types of dehydration equipment include: high-frequency dehydration screen, disc vacuum filter, ceramic vacuum filter, hydraulic chamber filter press, etc.
03Technical difficulties in lepidolite ore flotation
1. The ore composition is complex: Brown mica ore usually contains a variety of minerals, including other lithium-containing minerals, silicates, feldspars, and sometimes other rare earth elements. Isolating phacovite from these complex mineral assemblages can be difficult.
2. Particle fineness: Brown mica ore may contain a large number of fine particles. Fine particles can be difficult to float and specialized flotation equipment or technology may be required to effectively recover these fine particles.
3. Clay and mud coating: Clay and mud may coat mineral particles, inhibiting their flotation. Brown mica ores may contain clay minerals that interfere with the flotation process, requiring strategies to remove or mitigate their effects.
4. Water usage: The flotation process usually requires large amounts of water. Managing water use can be challenging in areas where water is scarce or restricted by environmental regulations.
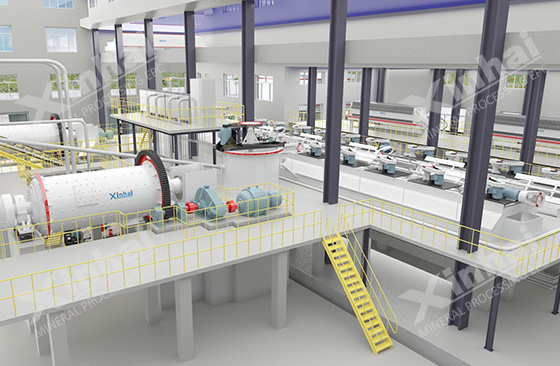
(Ore beneficiation process)
The above is a brief introduction to lepidolite ore flotation technology, mineral processing equipment and technical difficulties. Appropriate mineral processing technology and equipment need to be selected according to the characteristics of the ore, so as to overcome the technical difficulties in the mineral processing process and improve the mineral processing efficiency and concentrate quality. Therefore, it is necessary to conduct ore processing test analysis before mineral processing, which can provide guidance for the process with scientific basis for design and equipment selection.