In some wolframite deposits, there will be a small amount of scheelite. The existence of these scheelites will not affect the overall mineral beneficiation process, but it is necessary to add the separation operation of wolframite and scheelite ores in the beneficiation section. If the content of wolframite in the ore is equivalent to that of scheelite, it is necessary to consider the mineral properties of wolframite and scheelite to select a beneficiation process, which includes the selection of grinding particle size, selection of separation methods and equipment, etc.
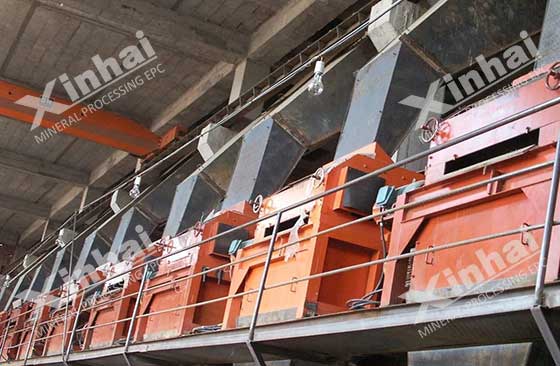
Wolframite and scheelite ores are both tungstates, but their cations are different, resulting in different floatability. The scheelite is easy to float, and the fatty acid collector can capture the scheelite, but the flotation performance of the wolframite is far worse than that of the scheelite. The tungsten minerals in symbiotic tungsten ores are finely dispersed, and the composition of the gangue minerals is also relatively complex. Therefore, a relatively complex beneficiation process is required. The mineral beneficiation process of black and white tungsten ore is mainly divided into two types: medium and fine grain embedded type and fine grain embedded type. The following will introduce the separation methods of black and white tungsten ore paragenetic ores based on these two ores.
Use the table of contents below to navigate through the guide:
01Beneficiation process for medium and fine grain embedded symbiotic tungsten
1. Single gravity separation process
The cost of gravity separation process is relatively low and causes less environmental pollution. When the specific gravity difference between the recovered minerals and the gangue minerals is large, the gravity separation process can be used. As mentioned above, there is a large density difference between black and white tungsten ore and other gangue minerals. Gravity separation is generally used to separate it from the gangue minerals. It is especially suitable for wolframite and scheelite with coarser particle sizes. Ore, gravity separation efficiency is higher.
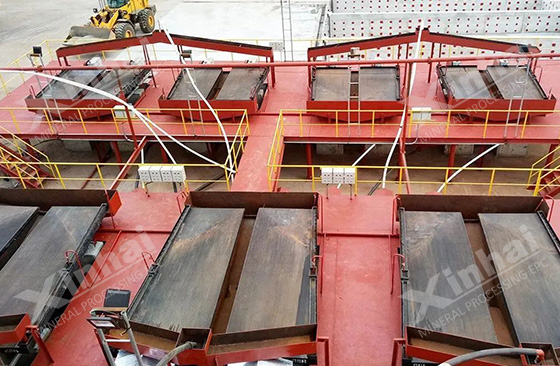
The single gravity separation process is mainly used to process wolframite and scheelite, which are mainly medium and coarse-grained tungsten ores, and the raw ore contains less sulfide ore. If the sulfide mineral content is too much, the gravity separation effect will be seriously affected. For tungsten ore containing sulfide ore, the beneficiation process can be carried out by flotation of sulfide ore, and the flotation tailings are classified and then entered into a shaking table for sorting to obtain a mixed concentrate of scheelite and wolframite. In the tungsten ore gravity separation process, equipment such as spiral concentrator, spiral chute and high-frequency vibrating screen are mainly used. Among them, the spiral concentrator and spiral chute are mainly used for rough separation. When wolframite ore is classified using hydraulic classification, the sorting efficiency is relatively low. Using a high-frequency vibrating fine screen as the classification equipment can effectively improve the classification effect.
2. Coarse particle gravity separation-fine particle flotation process
If the tungsten minerals in the ore are unevenly distributed in thickness, gravity separation can be used to recover most of the tungsten metal, but the recovery effect of fine-grained tungsten metal is poor. The lower limit of particle size that can generally be recovered by gravity separation technology is 0.037mm. Materials smaller than this particle size are difficult to recover. To address this problem, flotation can be used to make up for the shortcomings of gravity separation. The flotation process can effectively recover fine-grained tungsten metal in the ore. Therefore, the process of coarse-grained gravity separation and fine-grained flotation can be used for tungsten ore with uneven thickness. The gravity separation equipment used in this process includes spiral concentrator, spiral chute and shaking table, and the classification equipment uses hydrocyclone and high-frequency vibrating fine screen.
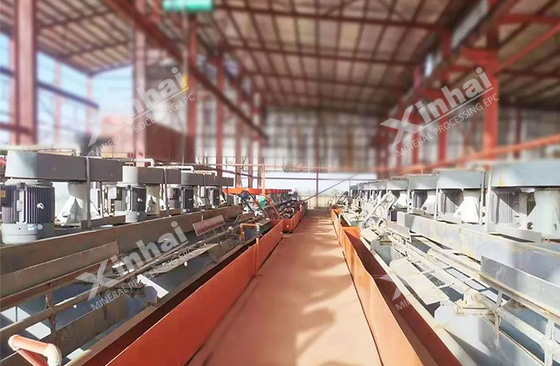
3. Combined process of gravity, flotation, magnetic and electric separation
If the mixed ore of wolframite and scheelite has complex components, and the tungsten minerals in the ore are mainly distributed in medium and fine grains, and mainly fine grains, the rough separation process can use the gravity separation method to select the black and white tungsten minerals into the coarse separation process. In concentrate. When selecting, you can grade them first. The coarse-grained minerals obtained after classification are subjected to a combined beneficiation process of flotation-magnetic separation-electric separation to obtain black tungsten concentrate and scheelite concentrate. Fine-grained minerals use a combined process of scheelite flotation-magnetic separation-gravity separation to separate scheelite and wolframite.
02Fine-grained symbiotic tungsten ore separation
The particle size of wolframite and scheelite in the fine-grained black and white tungsten ore paragenetic ore is generally above 2mm. When processing this kind of ore, the flotation process or the gravity separation-flotation combined process should be used.
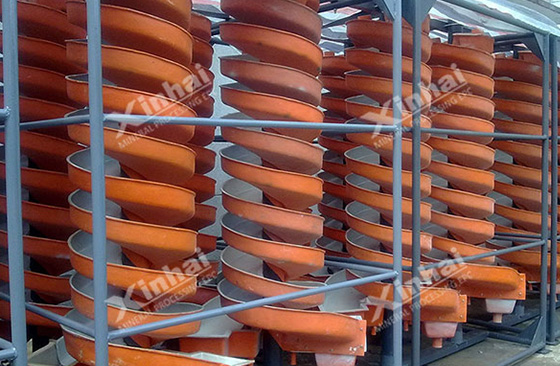
1. Gravity-flotation process
The raw tungsten ore is grinded and then enters the gravity separation operation. After separation, the tungsten coarse concentrate is obtained. The coarse concentrate is regrinded and desulfurized, and then scheelite flotation is performed to obtain scheelite concentrate. After magnetic separation, the scheelite flotation tailings enter the shaking table for gravity separation to obtain wolframite concentrate. The tailings from the first stage of gravity separation enter sulfide ore flotation after grinding, and the flotation tailings enter scheelite roughing. The scheelite coarse concentrate undergoes heated flotation to produce scheelite concentrate, and the heated flotation tailings undergo shaking table gravity separation to obtain wolframite concentrate.
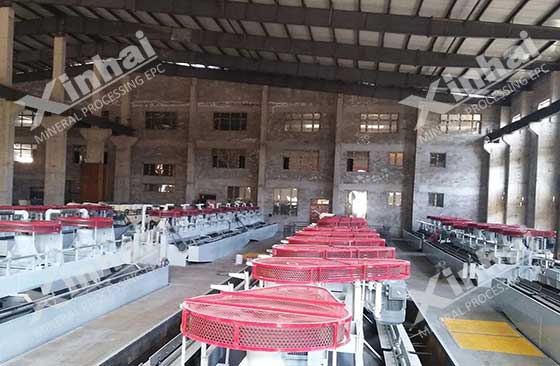
2. Mixed flotation process
It is relatively simple to recover tungsten minerals from a single scheelite or wolframite, but it is more difficult to recover the symbiotic ores of wolframite and scheelite, especially the sharply embedded ores. It is difficult to effectively recover fine-grained tungsten ore using gravity separation and magnetic separation processes, so the mixed flotation process of symbiotic tungsten ores can be used for recovery. Before mixed flotation, the ore needs to undergo a grinding process to separate most of the useful minerals from the gangue minerals.
The above content is the beneficiation process of mixed ores of medium and fine grained symbiotic tungsten ores. Since the components in paragenetic ores are relatively complex, it is necessary to study the ore characteristics and embedded distribution characteristics to formulate the mineral processing process, otherwise the mineral processing effect and concentrate recovery rate will be reduced.