Tungsten ores can be classified into four categories: brine type, quartz vein type, rock type, and skarn type. These four ores adopt different beneficiation process methods. The brine type tungsten ore adopts chemical beneficiation technology, and the quartz vein type tungsten ore adopts pre-enrichment + gravity separation technology, rock tungsten ore adopts gravity separation + flotation technology, and skarn tungsten ore adopts flotation + chemical beneficiation. Currently, the methods commonly used to recover tungsten minerals include flotation, gravity separation, magnetic separation and combined mineral separation.
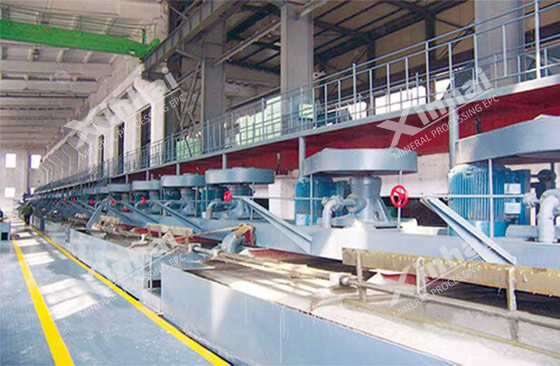
Pre-enrichment can play an important role in improving the grade of the selected ore and the technical and economic indicators of ore dressing, and reducing the grinding energy consumption. It is a very important process in the tungsten ore beneficiation process. Gravity separation technology is used to process coarse and medium-grained tungsten ore, which can effectively separate tungsten minerals and calcium-containing gangue minerals. Magnetic separation technology is mainly used for roughing and concentrating tungsten ore. It can separate wolframite and scheelite and remove magnetic mineral impurities in tungsten ore. Flotation method can be divided into caustic soda method, lime method, shear flocculation method, etc., which is the main method of scheelite separation. The following will introduce you to several scheelite mineral processing methods.
Use the table of contents below to navigate through the guide:
01Scheelite gravity separation technology
The equal ratio of scheelite and its gangue minerals is in the range of 2.08-2.78, making it an ore that is easy to be gravity separated. However, the scheelite ore has a relatively fine embedded particle size and needs to be ground to 0.2mm to complete basic monomer dissociation, which increases the difficulty of gravity separation and recovery. Equipment suitable for the gravity separation of fine-grained materials include spiral chute, fine mud groove shaker, etc. Because the spiral chute has a large processing capacity, a small footprint, and does not require power, it is the preferred equipment for gravity separation and treatment of scheelite in mineral processing plants. The purpose of gravity separation is to discard the tailings, reduce the amount of ore for further flotation, and eliminate calcium-containing gangue minerals to create conditions for selection.
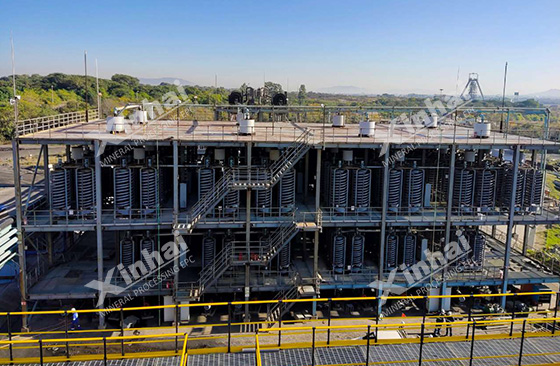
02Scheelite magnetic separation technology
Since wolframite has weak magnetism and scheelite is non-magnetic, magnetic separation technology can be used to separate wolframite and scheelite. Generally, mineral processing plants will choose magnetic separation technology and flotation technology to separate wolframite and scheelite to improve the recovery rate of concentrate. When there are magnetic minerals such as pyrrhotite and magnetite in the ore, magnetic separation technology can be used to separate these impurity minerals to achieve the purpose of pre-desulfurization and pre-enrichment of scheelite.
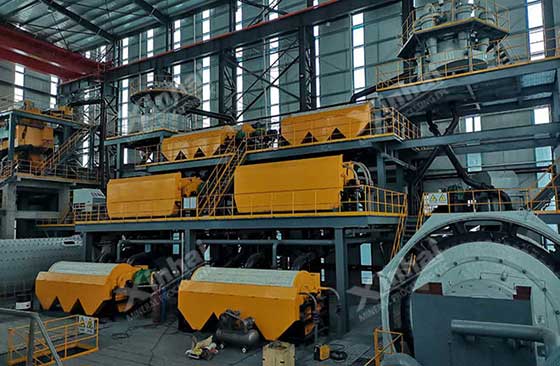
03Scheelite chemical beneficiation technology
Chemical beneficiation technology generally refers to chemical leaching, which is mainly used to process low-grade tungsten concentrates and medium ores, and is especially suitable for processing fine-grained disseminated refractory ores. Commonly used chemical beneficiation methods for scheelite mainly include hydrochloric acid decomposition, caustic soda leaching, soda solution pressure cooking, fluoride salt decomposition, etc. Different chemical methods require different process conditions. In order to achieve appropriate sorting results, actual production conditions need to be controlled.
04Scheelite flotation technology
The crystal grain size of scheelite is fine and its floatability is good, so flotation technology has become one of the main processes for recycling scheelite. The gravity separation, magnetic separation and chemical beneficiation technology of scheelite sometimes require a combined flotation process to achieve satisfactory beneficiation indicators. Tungsten ore flotation equipment has simple configuration, large processing capacity, high product quality and high concentrate recovery rate. However, the deployment of the flotation process should be based on the characteristics of the ore and the selection of appropriate flotation reagents to improve the flotation effect.
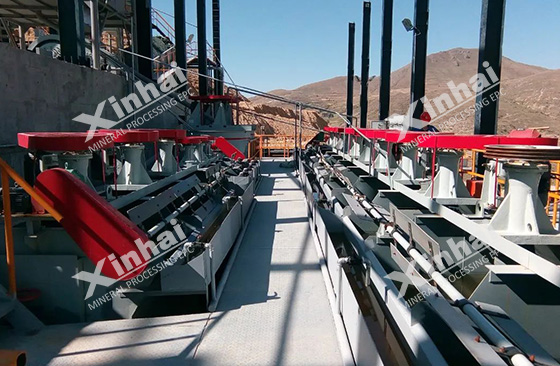
The above content is a brief introduction to several beneficiation process technologies of scheelite. Different technologies are used to process different types of scheelite, and when necessary, other mineral processing technologies need to be combined to improve mineral processing indicators. Xinhai Mining can provide you with overall mineral processing services for wolframite and scheelite according to the characteristics of the ore, helping you achieve high-efficiency recovery and utilization of resources and improving the economic benefits of the overall mineral processing plant.