The design of an iron ore processing plant is a complex process involving multiple considerations. The following are the general steps and key points that should be followed when designing an iron ore concentrator, including resource assessment, process design, equipment selection and configuration, environment and resources, infrastructure construction and other aspects. This article will introduce these contents one by one.
Use the table of contents below to navigate through the guide:
01Resource assessment for iron ore processing plant
Conduct detailed exploration of iron ore resources, that is, evaluate ore grade, reserves, mining conditions, etc. Iron ore resource assessment is a complex process, involving knowledge in geology, economics, finance and other fields. It requires collecting and sorting out relevant geological data of iron ore resources, including exploration reports, geological characteristics of mineral deposits, ore grades, reserve estimation, etc.
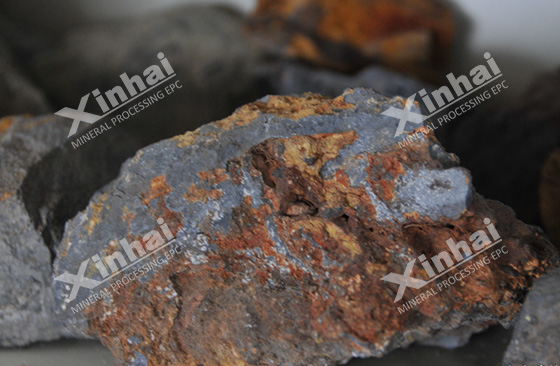
The key parameters required to determine the assessment include resource reserves, average grade, mining cost, mineral processing recovery rate, market price, expected mining life, etc. According to the ore grade, mineral composition, particle size distribution and other information provided in the assessment report, it will directly affect the selection and design of the mineral processing process. For example, high-grade ore may not require complex beneficiation processes, while low-grade ore may require multiple stages of grinding and beneficiation.
02Process design of iron ore processing plant
Beneficiation process flow design means selecting appropriate mineral processing processes based on the properties of iron ore, such as magnetic separation, flotation, gravity separation, etc. Considering the complexity of the ore and the symbiosis of multiple metals, a combination of multiple mineral processing methods may be required. Detailed physical and chemical analysis of ore samples is required, including the hardness, grade, particle size distribution, mineral composition, harmful element content, etc. of the ore, to analyze the selectivity of the ore and determine its appropriate beneficiation method and process flow. Design the process flow including crushing, grinding, classifying, beneficiation, dehydration and other links.
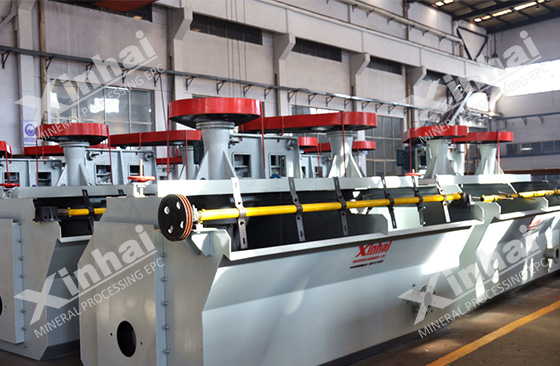
03Equipment selection and configuration of iron ore processing plant
Select appropriate mineral processing equipment according to the process flow, and determine the equipment type, specification, quantity and configuration method of each link.
Crushing equipment: such as jaw crusher, cone crusher, etc., used to break large pieces of ore into smaller particles.
Grinding equipment: such as ball mills, rod mills, etc., are used to further grind the crushed ore to achieve monomer dissociation of the minerals.
Screening equipment: such as vibrating screens, spiral classifiers, etc., used to separate ores of different particle sizes.
Separation equipment: such as magnetic separators,flotation machines, etc., used to separate minerals based on their magnetic or surface properties.
Dehydration equipment: such as thickeners, filters, etc., used to remove moisture from concentrates.
In addition, it is also necessary to consider the large-scale, efficient, and automated equipment to improve production efficiency and reduce costs. It is also necessary to consider the design of the connection methods between equipment, such as belt conveyors, chutes, etc., to ensure smooth flow of materials.
04Environment and resources of iron ore processing plant
Environmental protection facilities, such as wastewater treatment, waste gas treatment, solid waste treatment, etc., should also be considered during the design process of iron ore dressing plants to ensure compliance with environmental protection standards. Develop safety production procedures to ensure safety during the production process.
In addition, there is a need to assess energy needs, optimize energy use, and improve energy efficiency. Resource recovery and recycling systems should be designed to reduce resource waste.
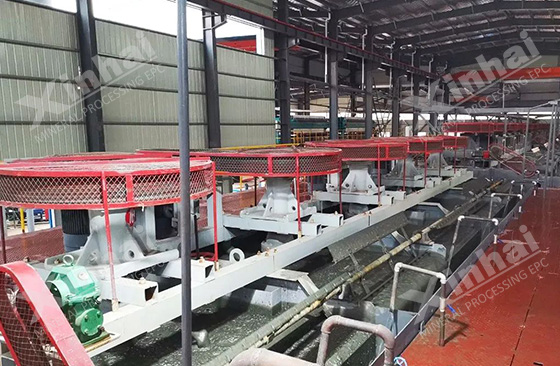
05Infrastructure construction of iron ore processing plant
In addition to designing and planning production facilities for iron ore concentrators, it is also necessary to plan necessary infrastructure, such as factories, warehouses, office areas, employee dormitories, etc., and build supporting facilities such as power supply, water supply, drainage, and communications. These issues are included in the design All need to be taken into consideration based on the specific conditions of the project site.
06Others of iron ore processing plant
In addition to the above content, economic analysis, compliance inspection, project management and implementation, etc. should also be considered when designing and planning the iron ore processing plant.
In terms of economic analysis, a cost-benefit analysis needs to be conducted to ensure the economic feasibility of the project. Assess project risks including market risks, technical risks, environmental risks, etc.
Ensure that the mineral processing plant design complies with national and local laws and regulations. During the design process and after completion, it will be subject to inspection and acceptance by relevant departments.
Develop project management plan, including timeline, budget, human resources, etc. Select appropriate contractors and suppliers for construction and equipment installation.
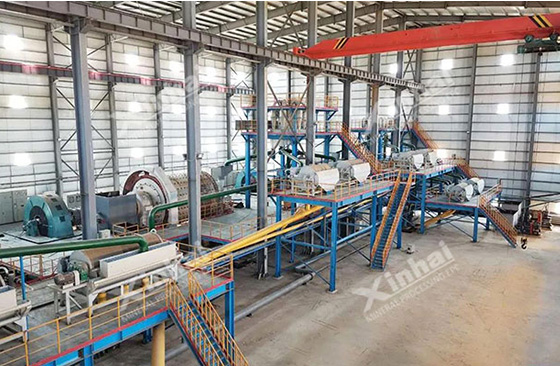
The above is about the design of iron ore processing plant. During the design process of iron ore beneficiation, it is also necessary to consider the specific local conditions and requirements, as well as possible technological progress and market changes. Design work is usually undertaken by professional design institutes or companies. Good concentrator design is critical to subsequent operations, ensuring efficient material handling processes and reducing energy consumption and maintenance costs. Reasonable layout reduces material handling distance and improves automation level, thereby improving production efficiency. In addition, environmentally friendly designs reduce pollution, comply with regulatory requirements, and contribute to the sustainable development of enterprises. Good design also facilitates future expansion and adapts to changes in market demand.
07Xinhai Mining-ferrous metal dressing plant project
1. Xinjiang 3300tpd iron ore dressing plant
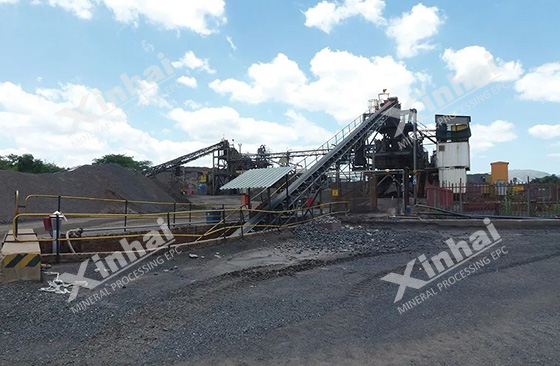
2. South Africa 3000tpd chromite flotation plant
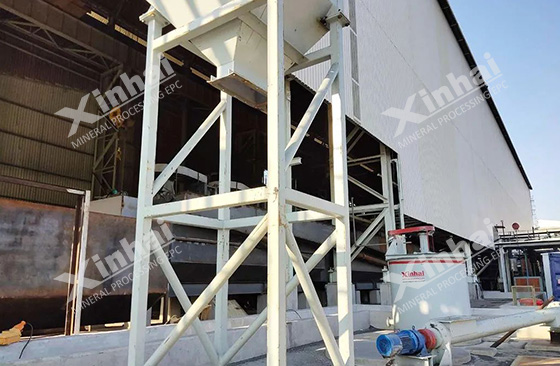
3. Inner Mongolia 2500tpd iron ore dressing plant
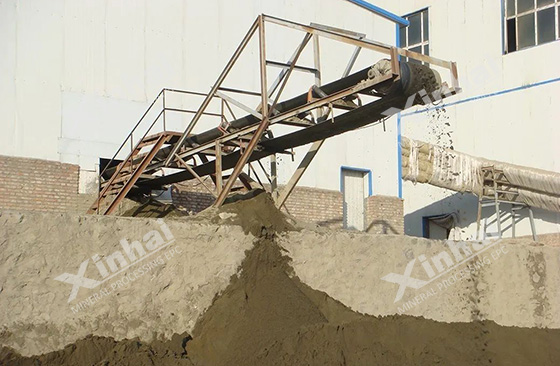
4. Yunnan 2000tpd iron ore dressing plant
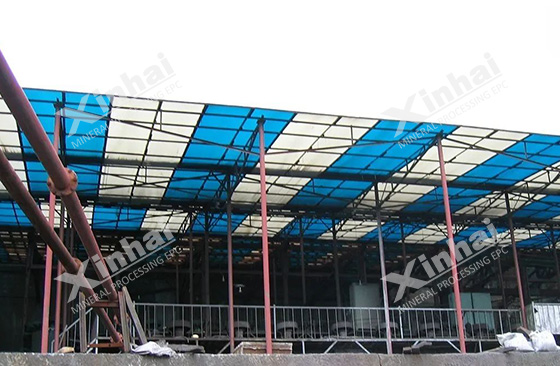
5. Hebei 2000tpd iron ore concentrate desulfurization plant
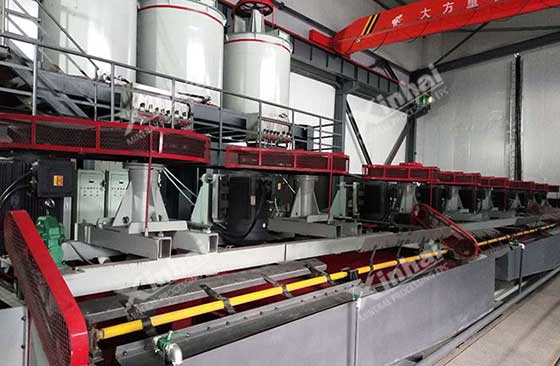
6. Shanxi 1200tpd iron ore dressing plant
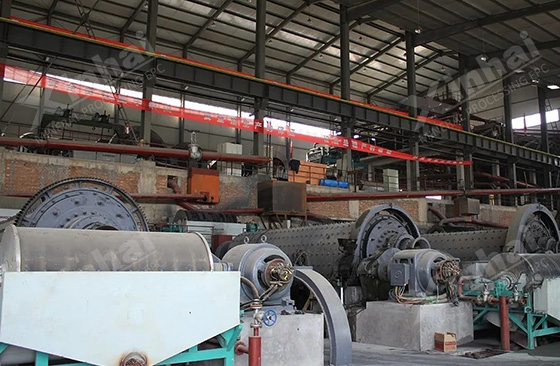