With the sustained and rapid economic development, the iron and steel industry is also developing rapidly. It has also become a trend to develop poor and miscellaneous iron ore to meet the needs of the industry. Technicians have done a lot of beneficiation research on these ores. The following will introduce two iron ore reverse flotation separation technologies and the reagents used in the process of flotation iron ore.
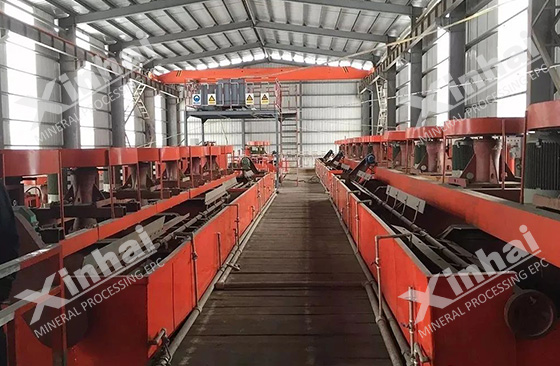
Use the table of contents below to navigate through the guide:
01Iron ore reverse flotation separation technology
Iron ore reverse flotation technology is mainly divided into cationic reverse flotation technology and anion reverse flotation technology.
1. Cationic reverse flotation technology
Most of the collectors used in cationic reverse flotation technology are amine collectors, which are mainly divided into aliphatic amines and aromatic amines. The amine collectors used to treat different minerals are different. For example, the flotation of silicate minerals requires the use of fatty amine collectors. Iron ore reverse flotation using cationic collectors is generally carried out at a pH of 7-10. Because the cationic reverse flotation technology uses a single reagent, that is, an amine collector, its reagent system is simple, and the temperature requirement for flotation is low, so it is more suitable for on-site application. Because iron ore flotation uses a single type of reagent, the flotation process is easier to operate, can be quickly adjusted according to changes, and has strong adaptability to process changes. Combining cation reverse flotation technology with magnetic separation and gravity separation technology can achieve good concentrate recovery rate, realize complementary advantages in process technology, and rationalize process structure.
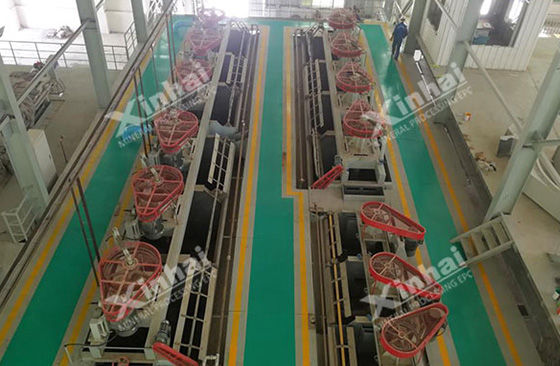
2. Anion reverse flotation technology
The effect of anionic iron ore reverse flotation is realized by the combination of sodium hydroxide, collector, starch and calcium oxide. Among them, the content of sodium hydroxide can affect the function of the collector. Sodium hydroxide has laid a certain foundation for the efficient separation of anion reverse flotation by adjusting the pH value of the pulp, changing the surface potential of the mineral and controlling the state of the drug.
Anion reverse flotation has strong adaptability to ferrous oxide. Unlike other flotation techniques, its main effect is on gangue minerals, so it has little direct impact on the change of ferrous oxide.
Anion reverse flotation technology can also effectively use the physical properties of minerals. The main mineral it collects is quartz. Since the density of quartz is lower than that of iron ore, the effective gravity of quartz in the flotation slurry is much lower than that of iron ore. This improves the collection efficiency of the quartz.
In the reverse flotation process of anion iron ore, the combined use of multiple agents can greatly improve the beneficiation effect. Because there are many types of drugs used, the effects of drugs are highly targeted, and their synergy is strong, which improves the beneficiation index of anion iron ore reverse flotation technology.
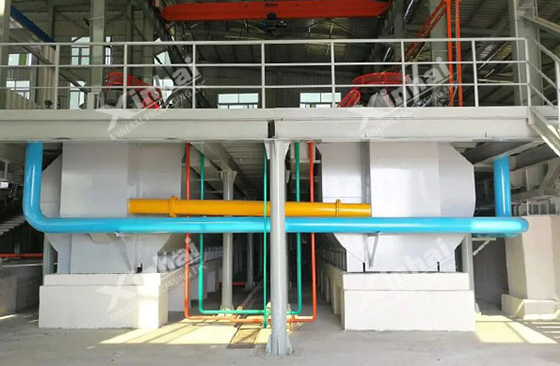
02Iron ore reverse flotation agent
1. Inhibitors
Starch is a commonly used inhibitor in the flotation process of iron oxide ore. Starch can be extracted from plants such as corn, cassava, and potato. Corn starch is widely used in the mining industry. Among the inhibitors extracted from other materials, carboxymethyl cellulose (CMC) has gradually become the main iron oxide ore flotation inhibitor.
2. Foaming agent
The foaming agents used in the iron ore reverse flotation process are mainly amine foaming agents, and there are also synthetic polyethylene glycol foaming agents. It can replace 10% of the total amine consumption and improve the recovery rate of flotation iron.
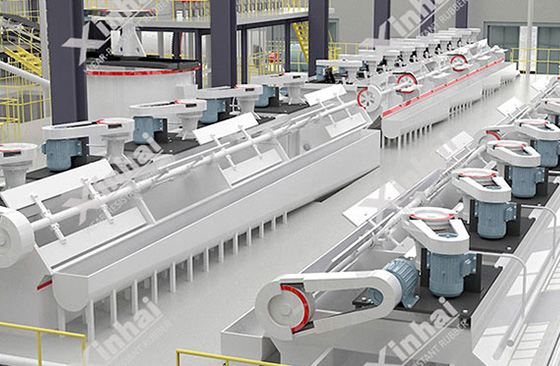
The above is the anion and cation reverse flotation separation technology of iron ore, as well as the inhibitor and foaming agent used in flotation. The specific iron ore beneficiation process should also be customized according to the characteristics of the ore. Xinhai Mining recommends to conduct iron ore beneficiation test analysis in order to customize a suitable beneficiation process. Xinhai Mining can provide turnkey solution for mineral processing plant (EPC+M+O), including ore beneficiation test, customized design of beneficiation process, production and manufacturing of a complete set of iron ore beneficiation equipment, packaging and shipping, installation and commissioning, and the overall operation of the mine in the later stage operations and management.