As a very precious resource, the beneficiation process of gold mineral is very difficult. There are many kinds of gold ore beneficiation methods used by the concentrator. Generally, the gold ore is sent to the crusher for crushing, and then sent to the ball mill for further processing. After grinding, gravity separation, cyanidation, flotation, etc. are carried out to further obtain gold ore concentrate. This article mainly introduces gold ore flotation technology, flotation equipment, flotation reagents and influencing factors during flotation.
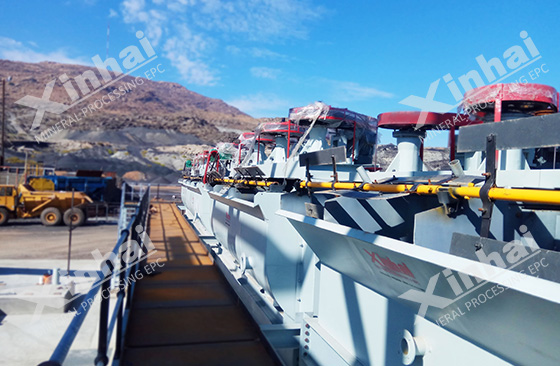
Use the table of contents below to navigate through the guide:
01Gold mineral flotation technology
The flotation technology of gold ore is carried out by utilizing the hydrophobicity of the surface of mineral particles. Hydrophobic means lipophilic and gas-friendly, and hydrophobic mineral particles will gather in liquid, gas or water-oil mixed cleansing. After a series of processes, the gold ore particles can be floated on the surface of the ore liquid of the flotation machine by affinity with air bubbles or flotation agents, and recovered as foam products.
02Gold mineral flotation equipment
The equipment in the flotation process mainly adopts flotation machines. The working principle of the flotation machine is: after the pulp is stirred and inflated, the gold ore particles will adhere to the air bubbles under the action of the flotation agent, and the ore particles will rise with the bubbles to form a mineralized foam layer on the surface of the pulp, and then Scraped by the scraper of the flotation machine or overflowed by itself. Different types of flotation machines can be selected for different stirring and aeration methods. At present, the types of flotation machines commonly used in mineral processing plants are: mechanical agitation flotation machines, inflatable mechanical agitation flotation machines and inflatable flotation machines. In actual production, the appropriate type and combination of flotation machines should be selected according to different situations.
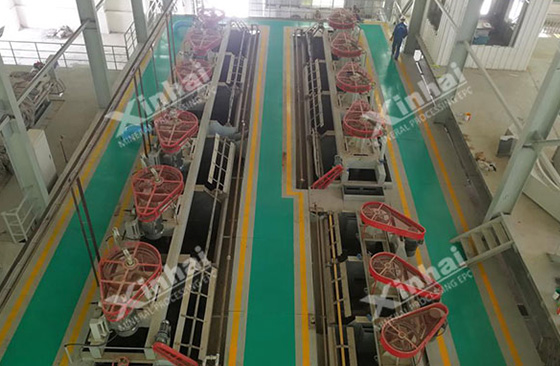
03Gold mineral flotation agent
There are about 50 kinds of reagents for gold ore flotation. Their main function is to selectively adsorb with mineral particles during the flotation process and change the hydrophobicity of the target mineral surface. Gold ore particles with strong hydrophobicity It will stick to the air bubbles and float out together with the air bubbles. According to the functional classification, the flotation agents of gold mines can be divided into three categories: collectors, foaming agents and regulators.
1. Gold ore flotation collector
There are two groups in the collector, one is a polar affinity group, and the other is a non-polar hydrophobic group. The former will selectively adsorb on the surface of gold ore minerals, while the latter has the effect of increasing the hydrophobicity of the mineral surface. Common gold ore flotation collectors are xanthate and black medicine.
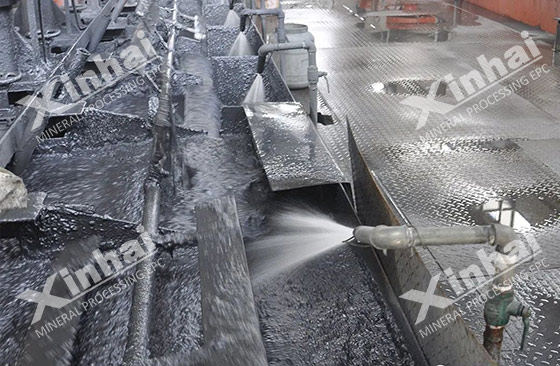
2. Gold ore flotation foaming agent
The effect of the foaming agent is mainly concentrated on the gas-liquid interface, which can reduce the tension of the interface, accelerate the dispersion speed of air in the pulp, and form tiny bubbles. At the same time, it can also prevent mergers between bubbles, increase the separation interface, and improve the stability of bubbles. The commonly used gold ore flotation foaming agent is No. 2 oil.
3. Gold ore flotation regulator
Regulators have a greater influence on the gold ore flotation process. Regulators can be divided into activators, inhibitors, pH regulators, dispersants and flocculants according to their functions.
The activator is mainly to promote the interaction between the collector and the mineral surface. The commonly used activators mainly include: alkali metal salts, such as copper sulfate.
The main function of the inhibitor is to inhibit the flotation of some gangue minerals and further improve the grade of the concentrate.
The role of the pH regulator is to eliminate harmful ions in the pulp, such as sodium carbonate, by adjusting the pH of the pulp.
The role of dispersing and flocculant is to change the particle size of the ore group of minerals.
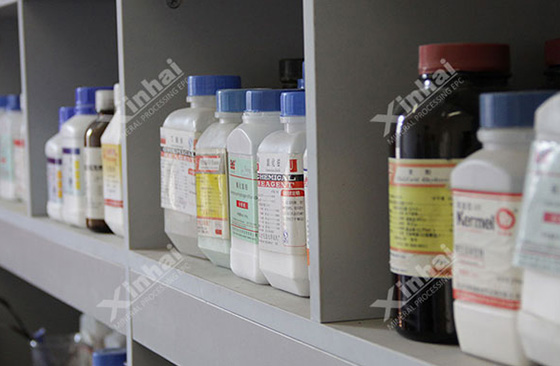
In actual production, there are many types of gold ore flotation reagents used, but the flotation process is not only affected by the type of flotation reagents, but also the dosage, addition method and order of the reagents will affect the flotation results.
04Influencing factors of gold ore flotation
In the gold ore flotation process, there are many influencing factors, the more important ones are as follows: grinding fineness, pulp concentration, reagent system, flotation time, aeration and stirring.
1. Grinding fineness
During flotation, the size of the mineral particles selected into the flotation machine is strictly required. If the ore particles are too thick, although the monomer dissociation has been completed, due to the large particle size and increased weight, they are attached to the air bubbles, and it is difficult for the air bubbles to lift them up, or they will be separated from the surface of the air bubbles during the stirring process after being brought up. If the ore particles are too fine, the grinding cost will increase, and it is easy to produce slime. The specific surface area of the slime increases, the surface activity is enhanced, and a large amount of flotation reagents and other mineral particles are adsorbed, thereby deteriorating the flotation process, reducing the concentrate grade and recovery rate, and increasing chemical consumption.
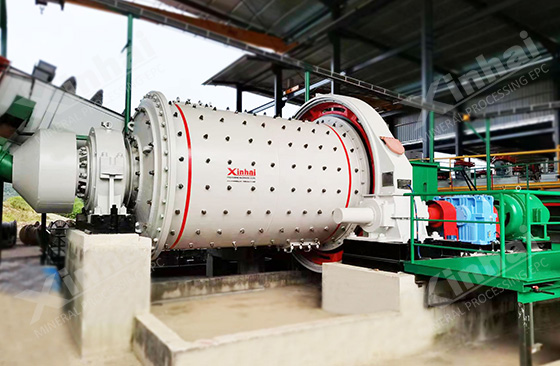
2. Pulp concentration
Slurry concentration affects the concentrate recovery and quality of the flotation process. When the pulp concentration is too low, the concentrate recovery rate is low, but the concentrate quality is high. On the contrary, if the pulp concentration is too high, the concentrate recovery rate will be high, but the concentrate quality will be reduced. Generally, thicker pulp is used for flotation of coarse-grained materials with larger specific gravity. Thinner pulp is used for flotation with small specific gravity or fine-grained minerals and mixed materials. During roughing and sweeping, thicker pulp is also used. During the beneficiation operation and flotation separation of difficult-to-separate mixed concentrates, a thinner pulp is generally selected to ensure high-quality qualified concentrates.
3. Pharmaceutical system
The type, dosage, sequence, place and method of adding medicines all belong to the medicine system.
The flotation agent is the main factor to adjust the floatability of minerals. How much its dosage directly affects the recovery efficiency of concentrate ore. If the dosage is insufficient, the adjustment effect cannot be achieved. The target mineral is difficult to recover. When the dosage is too high, the quality of the concentrate will be reduced. , causing drug waste. Therefore, in the flotation process, the addition of reagents should be appropriate and selective.
Choose the place and method of dosing according to the action characteristics of the drug. The way of drug addition is mainly divided into one-time addition and segmented addition. Adding in stages has the advantages of preventing drug overdose and failure, improving drug efficacy, and saving dosage.
There are two order of drug addition: one is flotation raw ore: regulator→inhibitor→collector→foaming agent; the other is flotation inhibiting mineral: activator→collector→foaming agent.
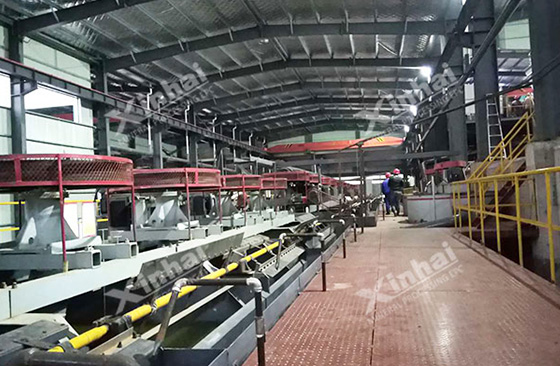
4. Flotation time
The recovery rate of useful minerals generally increases with the prolongation of flotation time, but the concentrate grade will decrease. The flotation time can be shortened if the minerals to be flotation have good buoyancy, low raw ore grade, high dissociation degree of mineral monomers, and fast medicament action. When flotation ore with high mud content, the flotation time will also be extended.
5. Aerate and Stir
The amount of air in the flotation machine and the amount of foaming agent will affect the amount of foam generated during the flotation process. The amount of aeration is mainly determined by the type of flotation machine and the flotation process. The smaller the bubbles, the better the dispersion, and the larger the total surface area of the cheongsam, the more conducive to flotation. But it should be noted that the small bubbles will slow down their rising speed, which is not good for flotation. At the same time, adding an excessive amount of foaming agent will reduce the air intake of the flotation machine. Therefore, attention should be paid to the amount of foaming agent while adjusting the amount of inflation.
The purpose of slurry stirring is to ensure that the ore particles are suspended and evenly dispersed in the slurry, and the stirring can also make the air evenly dispersed in the slurry. Stirring can promote the dissolution of air in the high-pressure area of the flotation machine, and the precipitation of microbubbles in the low-pressure area. Increasing the stirring of the pulp can increase the collision probability of the target ore particles and air bubbles.
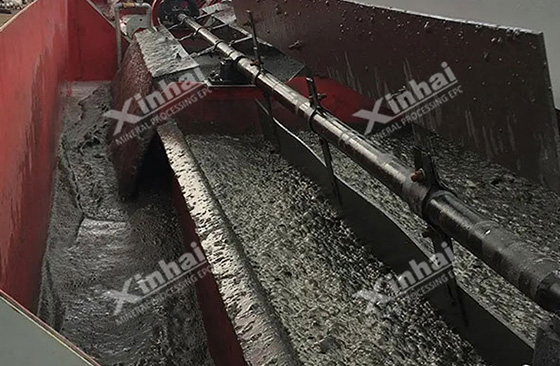
The above content is a brief introduction of gold mineral flotation technology, flotation equipment, flotation reagents and flotation influencing factors. In the flotation process, there are other influencing factors. In order to achieve the ideal gold ore flotation effect, Xinhai Mining recommends that the beneficiation test of gold ore should be carried out first to determine the characteristics of the ore itself, and to formulate a suitable ore beneficiation according to the characteristics of the ore. Xinhai Mining can provide accurate beneficiation tests and customized complete gold ore beneficiation process. Xinhai gold ore beneficiation process equipment can help you realize the efficient operation of the beneficiation plant. Welcome to consult.