Tin sulfide is an important mineral resource for obtaining tin. It is mainly composed of tin sulfide ores. Common tin sulfide minerals include cassiterite (SnO₂), yellow stannite (Cu₂FeSnS₄), cylindrical tin ore (PbSn₄FeSb₂S₁₄), etc. Its ore composition is relatively complex. In addition to tin-containing minerals, it often contains a variety of metal sulfides, such as pyrite, chalcopyrite, galena, etc., which undoubtedly increases the difficulty of tin ore beneficiation. No matter how to select tin, its principle process basically follows the steps of crushing, grinding, sorting and dehydration. Let's take a look at the sulfide tin ore beneficiation process and the required equipment.
Use the table of contents below to navigate through the guide:
01Tin ore crushing and grinding process
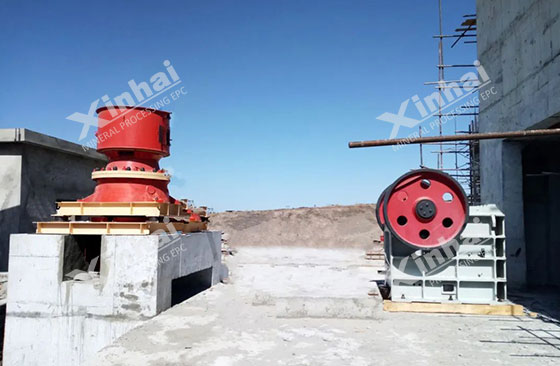
Crushing and grinding is to crush the raw tin ore to a suitable particle size, and then fully dissociate the tin minerals through grinding. The equipment required for this link is usually jaw crusher, cone crusher, ball mill and rod mill.
1. Crushing
A two-stage closed-circuit process is often used. The raw ore after mining is fed into the jaw crusher for coarse crushing to about 100-200mm, and then the cone crusher is used for medium and fine crushing to further reduce the ore particle size to about 10-25mm.
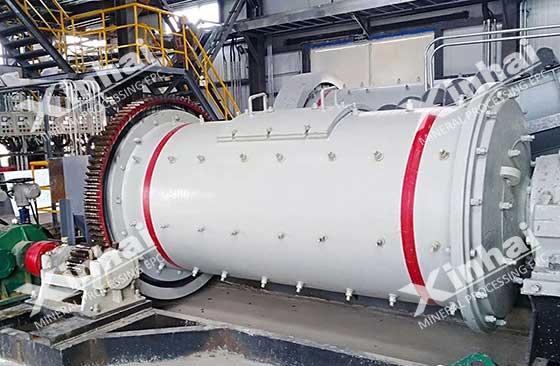
2. Grinding
The crushed ore enters the ball mill or rod mill for grinding, and the grinding fineness is usually controlled at -200 mesh, accounting for about 60%-70%. During the grinding process, the grinding time and the ratio of grinding media should be reasonably adjusted according to the hardness and grindability of the ore to achieve the purpose of fully dissociating the tin minerals.
02Tin ore beneficiation process
The beneficiation process of tin ore depends on the properties of tin ore. According to the different properties of its gangue minerals, the available methods include flotation, gravity separation and magnetic separation. The equipment required for the separation stage is determined according to the process requirements. There are flotation machines (XCF, KYF, JJF, SF, etc.), gravity separation includes jigs, spiral chutes and shaking tables, and magnetic separation includes permanent magnetic separators, dry magnetic separators, magnetic drums and high gradient magnetic separation.
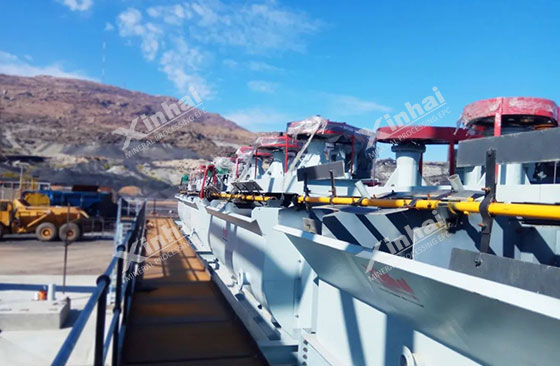
1. Tin ore flotation process
It is to utilize the difference in physical and chemical properties between tin minerals and other minerals, and to add flotation agents to make tin minerals adhere to bubbles and float out, so as to separate them from gangue minerals. There are two types of flotation: preferential flotation and mixed flotation. The former is to add inhibitors to inhibit gangue minerals first, and then add collectors and frothers to float tin minerals to obtain tin concentrates, and the tailings are scavenged to recover the residual tin; the latter is to add collectors and frothers to tin minerals and other minerals with good floatability for flotation to obtain mixed concentrates, and then separate the mixed concentrates to obtain tin concentrates and other mineral concentrates respectively.
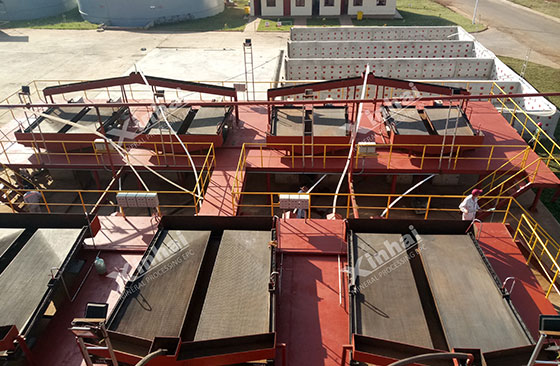
2. Tin ore gravity separation
It is to further improve the grade of coarse-grained tin ore by gravity separation. It is usually carried out after flotation, and the flotation concentrate is subjected to gravity separation to obtain high-grade tin concentrate. There are shaking table separation and jigging separation. The former is to feed the flotation concentrate into the shaking table, and under the vibration of water flow and bed surface, the minerals are separated according to the difference in specific gravity. The heavy minerals (tin minerals) remain on the bed surface, and the light minerals (gangue minerals) are carried away by the water flow; the latter is to use the alternating action of rising and falling water flow to stratify the minerals in the bed according to their specific gravity. Tin minerals with larger specific gravity settle to the bottom, and gangue minerals with smaller specific gravity are washed away by the water flow.
3. Magnetic separation of tin ore
The main purpose is to remove magnetic impurities in the ore, such as magnetite, and improve the grade of tin concentrate. It is usually carried out under weak magnetic field conditions. Magnetic impurities (such as magnetite) are adsorbed by the magnetic field of the magnetic separator and separated from non-magnetic tin minerals.
03Dehydration of tin ore concentrate
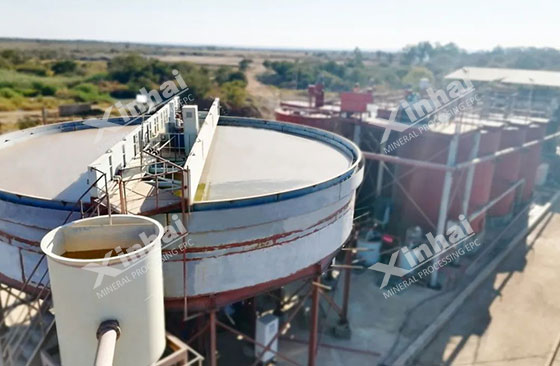
In the process of tin ore concentrate treatment, dehydration is an important link, which plays a vital role in improving the quality of tin concentrate, reducing transportation costs and subsequent smelting processes. The process is mainly to dehydrate the tin concentrate to a certain degree through the combination of various concentration and dehydration equipment, and then store it for smelting. The commonly used equipment in this link is mainly concentrators, presses, etc.
Concentrator: The tin-containing concentrate slurry obtained after flotation, gravity separation or magnetic separation is fed into the concentrator for concentration and dehydration, and the final water content can be as low as 30%.
Filter: The concentrated slurry is then filtered into the filter to obtain tin concentrate with a lower water content, which can reduce the final dehydration rate of the tin concentrate to 20~15%.
The above is an introduction to the beneficiation process of sulfide tin ore. In an actual beneficiation plant, since tin ore beneficiation is a complex system engineering, the selection of the process needs to consider the nature of the ore, the scale of the beneficiation plant and the technical level, etc. It is recommended to conduct beneficiation tests and design a tin ore beneficiation process suitable for you through experimental analysis.