Metal tin is one of the earliest metals discovered and used in human history. It has three allotropes: gray tin, white tin and brittle tin. Tin has the advantages of low melting point, non-toxicity, corrosion resistance, ability to form alloys with various metals, and good ductility. It is widely used in industry. Cassiterite is the only mineral with economic value for extracting metallic tin. Gravity and flotation are often used in mineral processing to sort cassiterite. Of course, with the development of technology, some new technologies have emerged. The following will mainly introduce tin stone mineral processing technology to you.
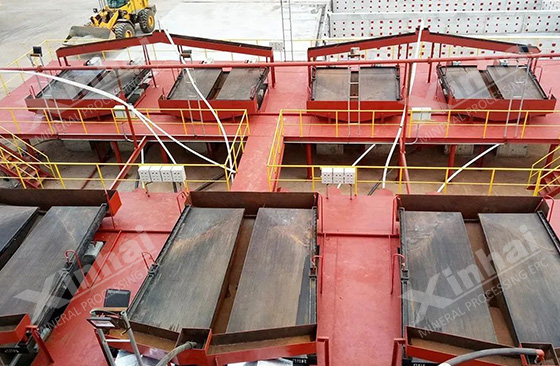
Use the table of contents below to navigate through the guide:
01Cassiterite gravity separation technology
Since the density of cassiterite is higher than that of gangue minerals, gravity separation is generally used as the main method for processing cassiterite. Gravity separation has the advantages of low cost and low pollution. Equipment commonly used for cassiterite gravity separation mainly includes shakers, spiral chutes, jigs, heavy media mineral processing equipment, etc. The shaking table is the main equipment of the tin dressing plant. It can be used to process some fine-grained cassiterite. The shaking table has a high enrichment ratio and can be used to extract high-grade concentrate or discard the final tailings. Spiral classifiers are widely used in tin concentrators because of their simple structure, large processing capacity, no need for power, simple and convenient operation and maintenance, etc. When gravity separation is used to process fine mud with a particle size less than 43μm, it is necessary to set up classification processing operations before the gravity separation operation. Commonly used classification equipment include high-frequency vibrating screens, probability screens, hydraulic classifiers, hydrocyclones, etc., mainly for Prevent cassiterite from being over-crushed.
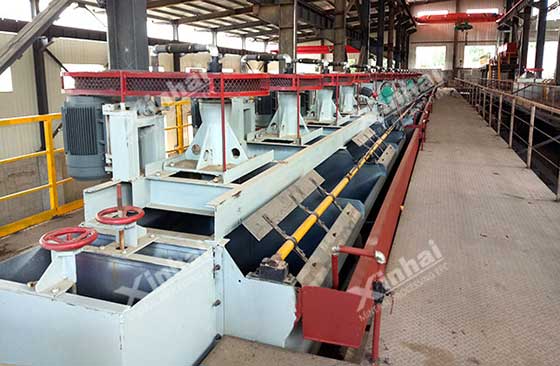
02Cassiterite flotation separation technology
The flotation method is used to recover cassiterite by utilizing the different chemical properties of the mineral surface for sorting. During the flotation process, collectors and gangue mineral inhibitors need to be added. These agents will cause changes in the mineral surface and increase the flotability difference between the target mineral and the gangue minerals. Therefore, it is said that flotation agents are important in flotation process.
In the cassiterite flotation process, commonly used collector types include fatty acids, alkyl sulfosuccinamates, arsenic acid and alkyl hydroxamic acid.
The types of inhibitors commonly used in the cassiterite flotation process are mainly divided into two categories: organic inhibitors and inorganic inhibitors. Inorganic inhibitors include sodium carboxymethylcellulose, naphthol sulfonic acid, oxalic acid, citric acid, lactic acid, etc. Inorganic inhibitors include sodium hydroxide, sodium carbonate, ammonium chloride, copper chloride, sodium sulfide, sodium hexametaphosphate, etc.
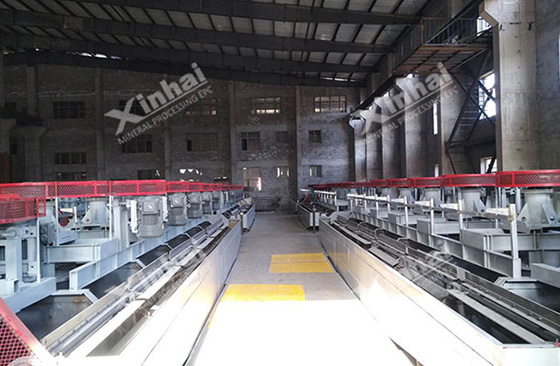
03New technology for cassiterite flotation
The new technology of cassiterite flotation is mainly used to process fine-grained tin ore, mainly including selective flocculation flotation, shear-flocculation flotation, dissolved air flotation, etc.
1. Selective flocculation process: This process mainly relies on the bridging effect of high molecular polymers to flocculate fine particles and then sort them. The key to this technology is to select the appropriate flocculant to adjust the physical and chemical properties of the slurry so that the agent is specific to the mineral surface. Commonly used polymer flocculants mainly include starch, tannin, dextrin, carboxymethyl cellulose, sodium humate, etc.
2. Shear flocculation and flotation process: The process needs to combine the effects of two forces, namely the hydrophobic bonding force generated by the adsorption of the collector on the surface of the ore particles and the shear force generated by the strong stirring of the slurry. These two forces can make the fine mineral particles form flocs and carry out the flotation method of separation and recovery. The main purpose of this process is to increase the particle size of the target mineral to facilitate flotation recovery, in which strong stirring and the use of long hydrocarbon chain collectors are important conditions.
3. Dissolved air flotation process: Use air supersaturated water to generate microbubble clouds. The size of these microbubbles is smaller than those produced by conventional dispersed air systems. This process can be used to process fine mud minerals, and it can effectively separate cassiterite and quartz.

The above content is a basic summary of cassiterite ore beneficiation methods. With the gradual reduction of high-grade easy-to-separate ores, improving the beneficiation efficiency of difficult-to-separate ores has gradually attracted attention. Among them, the recovery of fine-grained cassiterite is a difficult problem. When beneficiating minerals, the beneficiation process needs to be formulated according to the characteristics of the ore. Xinhai Mining recommends conducting beneficiation tests to determine the characteristics and selectability of tin ore, customizing the beneficiation process and equipment, improving the beneficiation efficiency and indicators, and maximizing utilization of ore resources.