The beneficiation methods and processes of titanium-zirconium ore are affected by factors such as deposit type, ore properties and mineral composition. In particular, titanium primary ore (vein ore) has similar ore properties and a relatively single type of target mineral, so its mineral processing methods show significant commonalities. In contrast, titanium placer and zirconium placer deposits usually exhibit complex symbiotic relationships, involving comprehensive placer deposits of multiple minerals. In this context, an in-depth discussion of the beneficiation process of primary titanium ore is crucial to understanding its unique beneficiation methods and processes. This will provide guidance for more efficient utilization of titanium resources.
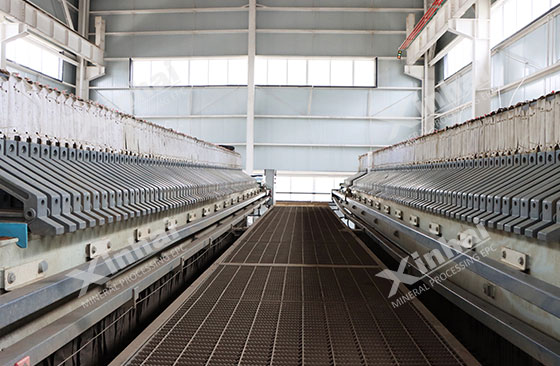
At present, the primary titanium ore used in industry is mainly titanium-containing composite iron ore. In order to effectively utilize these titanium resources, the beneficiation process is usually divided into three stages: pre-selection, iron selection and titanium selection according to the different properties of the ore. In the titanium selection stage, it is further subdivided into two parts: rough selection and fine selection.
Use the table of contents below to navigate through the guide:
01Pre-selection of primary titanium ore
In the pre-selection process of titanium primary ore, after some titanium vein ores are crushed, some coarse-grained ores will have a considerable amount of gangue that has basically dissociated into monomers. At this time, these coarse-grained gangue can be removed through pre-selection operations to improve the processing capacity and selection grade of the beneficiation plant. Pre-selection operations can be carried out in the coarse, medium and fine crushing stages before grinding according to the properties of the ore. Commonly used methods include magnetic separation and gravity separation.
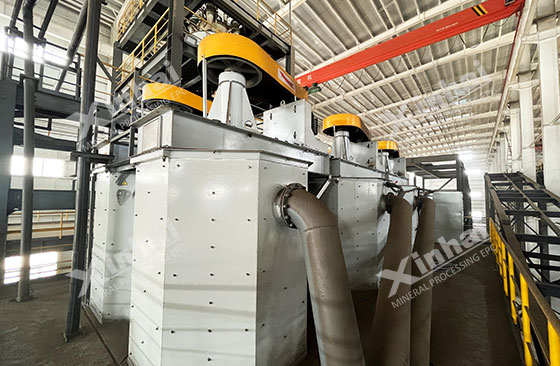
02Iron selection from primary titanium ore
In industry, the main purpose of titanium-containing composite iron ore is to produce iron concentrate for ironmaking; while for ores with high vanadium content, the main purpose is to extract vanadium-iron concentrate for ironmaking and vanadium extraction. The iron selection process usually adopts a simple and effective magnetic separation method. After crushing (or pre-selection) and grinding, the selected ore reaches a suitable monomer dissociation degree, and then a drum or belt weak magnetic field wet magnetic separator is used to separate the iron concentrate or vanadium-iron concentrate. The tailings after magnetic separation can be used as a raw material for comprehensive recovery of titanium.
In some cases, the iron minerals and titanium minerals in the ore are closely embedded, making it difficult to separate independent concentrates by a single beneficiation method. At this time, the use of gravity separation to remove tailings can effectively separate low-density gangue to obtain iron-titanium mixed concentrates. These mixed concentrates can then be directly roasted and smelted to produce high-purity pig iron and titanium slag products. This process not only improves the resource recovery rate, but also reduces environmental impact, providing a new solution for the efficient use of ores.
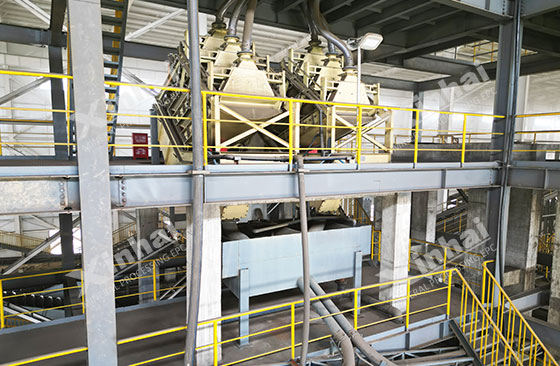
03Titanium beneficiation from primary titanium ore
In the beneficiation process of titanium vein ore, titanium recovery is usually carried out in the magnetic tailings after the extraction of iron ore concentrate. The methods of titanium beneficiation include gravity separation, magnetic separation, electrostatic separation and flotation. These methods are selected according to the different properties of the ore, thus forming a diversified beneficiation process. At present, the titanium beneficiation process commonly used in beneficiation plants mainly includes the following types:
1. Gravity separation-electrostatic separation process
The gravity separation-electrostatic separation process is characterized by using gravity separation for roughing and then electrostatic separation for concentrating. In the gravity separation stage, the main equipment used includes spiral concentrators (such as spiral chutes) and shaking tables. At present, the application of cone concentrators in gravity separation has entered the industrial trial stage, but has not yet been officially put into production. The main goal of gravity separation is to remove low-density gangue to obtain a rough concentrate suitable for electrostatic separation.
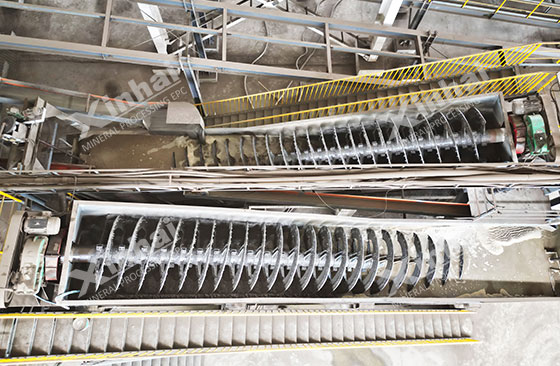
In the electrostatic separation stage, a roller electrostatic separator is used to further enrich the rough concentrate after gravity separation to ensure that the final product meets the concentrate standard. For sulfur-containing ores, flotation is usually used as an auxiliary process between roughing and concentrating to remove sulfide ores.
2. Gravity separation-magnetic separation-flotation process
The main feature of the gravity separation-magnetic separation-flotation process is the classification of the raw ore. For coarse-grained ore, gravity separation is first used for roughing, followed by magnetic separation for fine separation; while fine-grained ore is processed by flotation. A shaking table is usually used in the gravity separation process, and a dry magnetic separator is used for magnetic separation. The feed particle size during flotation is generally -0.074 mm, and sulfuric acid, sodium fluoride, oleic acid, diesel and pine oil are often used as flotation agents. This process effectively improves the recovery rate and product quality of titanium ore.
3. Single flotation process
Single flotation is an effective technology for fine-grained titanium vein ore selection, which has attracted attention due to its simple process and easy operation and management. However, due to the large consumption of reagents, which may lead to increased costs, and the discharge of tailings may also cause environmental protection problems, its application in industry is relatively limited. Commonly used flotation agents for titanium flotation include sulfuric acid, tall oil, diesel and emulsifiers. In order to improve the flotation effect, it is recommended to stir the ore and flotation agent at high concentration for a long time before flotation, which can effectively improve the selection efficiency.
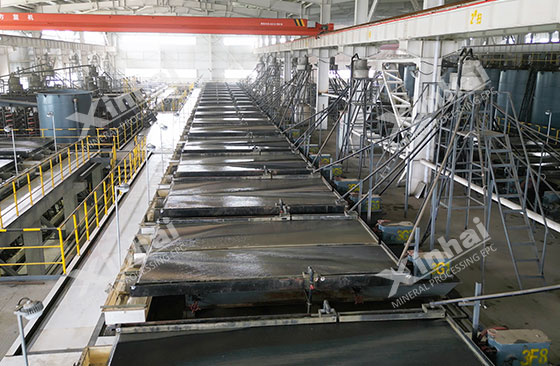
In summary, the beneficiation process of titanium zirconium ore is affected by the type of ore deposit and the properties of the ore. Especially in the beneficiation of titanium primary ore, a clear process flow can effectively improve the recovery efficiency of titanium resources. From pre-selection to iron selection, and then to each stage of titanium selection, each step is crucial. Through the combination of multiple methods such as gravity separation, magnetic separation and flotation, it is possible to formulate a suitable process flow according to the characteristics of different ores to maximize the grade and recovery rate of the concentrate. Although the single flotation method has certain advantages in some cases, its challenges of reagent consumption and environmental impact also remind us that the continuous exploration of more efficient and environmentally friendly beneficiation technologies will be the direction of future development. Only through continuous optimization and innovation can we better utilize titanium resources and promote the sustainable development of related industries.