Tin has a low melting point, good plasticity, corrosion resistance, fatigue resistance and non-toxicity. It is widely used in the development of the national economy and the field of national defense. In the past, tin ore resources were mostly used to make cast iron, alloys and other materials. Now, with the advancement of science and technology, tin has also been widely used in solar cells, lead-acid batteries and other electronic industries.
According to the properties of tin ore, the commonly used methods for its beneficiation are mainly gravity separation and flotation. Let's introduce the gravity separation and flotation methods of tin ore and the tin ore dressing technology.
Use the table of contents below to navigate through the guide:
01Tin ore gravity separation method
Due to the high specific gravity of tin ore, gravity separation is often used for separation. However, due to the brittleness of cassiterite, it often suffers from over-wear during the grinding stage. At this time, if the fine tin is subjected to gravity separation alone, it is impossible to obtain an ideal tin concentrate. Flotation separation is often used to complete the separation operation. Common gravity separation methods include shaking table, chute and jigging gravity separation.

Shaking table gravity separation: It relies on the asymmetric reciprocating motion of the bed surface and the flushing effect of the lateral water flow to make the minerals of different specific gravities stratified on the bed surface and move in different directions, thereby achieving separation. The shaking table has high sorting accuracy and can effectively separate fine-grained cassiterite. It is suitable for the sorting of various types of tin ores, especially the recovery of fine-grained cassiterite in cassiterite-quartz type ores.
Jigging gravity separation: It uses the pulsating water flow up and down to loosen the bed layer, and the minerals of different specific gravities are stratified according to their specific gravity in the vertical direction, with heavy minerals at the bottom of the bed layer and light minerals at the top of the bed layer, and then discharged separately through the ore discharge device. Jigging gravity separation has a large processing capacity and high efficiency. It is mostly suitable for processing coarse and medium-sized tin ores, especially the recovery of coarse and medium-sized tin of cassiterite-sulfide type and cassiterite-skarn type.
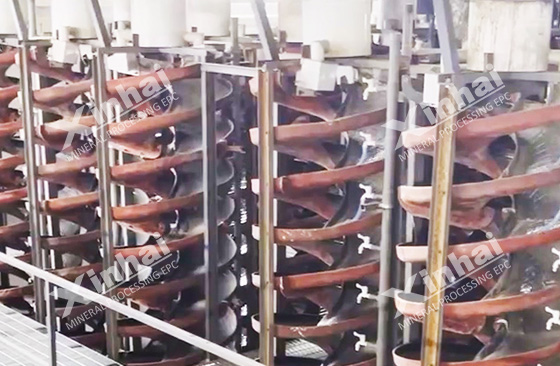
Spiral chute gravity separation: When the slurry flows in the spiral chute, the combined effects of centrifugal force, gravity and friction separate the minerals of different specific gravities into layers at different positions of the spiral chute, with heavy minerals close to the inner edge of the chute and light minerals close to the outer edge of the chute, thus achieving separation. Chute gravity separation is mostly suitable for the recovery of fine-grained tin ore, and has a good recovery effect on cassiterite-quartz type, cassiterite-sulfide type and other minerals.
02Tin ore flotation method
With the continuous mining over the years, the easy-to-select tin resources are decreasing day by day, and the development of fine-grained and difficult-to-select tin ores is imminent. This type of difficult-to-select tin ore is mainly based on flotation. At present, the common tin ore flotation methods mainly include selective flocculation flotation, carrier flotation and shear-flocculation flotation.
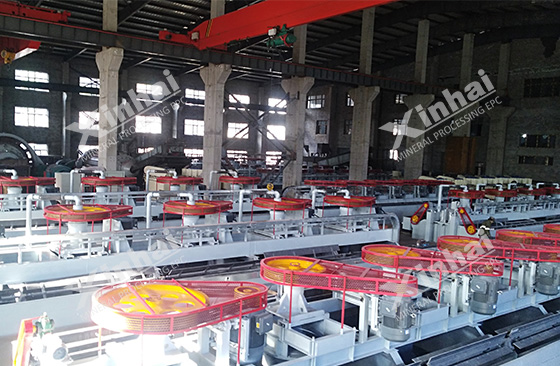
Selective flocculation flotation: in the high-speed stirring slurry, add appropriate adjusters (pH adjusters and gangue mineral dispersants) to adjust the slurry so that various minerals are in a dispersed state, and then add selective flocculants to make the target minerals flocculate into agglomerates and the gangue minerals are in a dispersed state. According to the properties of the ore, various collectors or inhibitors are added to separate the flocculated target minerals from the gangue minerals by flotation.
Carrier flotation: It uses minerals of general flotation particle size as carriers to make fine particles float on the carrier. The carrier can be the same or different minerals. For tin ore, minerals with larger specific gravity and better floatability are usually selected as carriers, such as coarse-grained cassiterite, pyrite, etc. During the flotation process, appropriate collectors and frothers are added to make the carrier minerals and fine-grained tin ore float together to achieve tin ore recovery.
Shear-flocculation flotation: It is a flotation method that uses the shear force generated by the strong stirring of the slurry and the hydrophobic bonding force generated by the collector adsorbed on the surface of the ore particles to form flocs of fine ore particles for separation and recovery.
03Tin ore beneficiation process
The beneficiation process of tin ore is determined according to the properties of the ore. Due to the wide variety of tin ores, the process flows are different. Each tin ore needs its own process plan, for example:
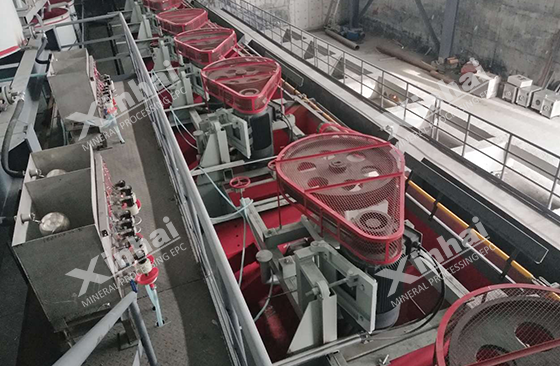
1. In a porphyry tin deposit, the ore contains a small amount of valuable elements such as tungsten, molybdenum, bismuth, and copper in addition to tin. Through beneficiation test analysis, the process flow designed for it is: first float sulfide ore, and recover cassiterite from the floating sulfide tailings by gravity separation-fine mud flotation-gravity separation combined process, and obtain tin concentrate with 56.11% tin and 74.20% recovery rate, and recover molybdenum concentrate products with 47.22% molybdenum and 67.65% recovery rate.
2. A polymetallic sulfide tin ore, the original ore contains a large amount of sulfide ores and a considerable amount of iron oxide minerals and iron carbonate minerals. The cassiterite is finely embedded and has a high dispersion rate. Through the analysis of the ore dressing test, a process flow of preferential desulfurization, zinc flotation and tin reselection by flotation tailings was designed. Finally, a tin concentrate with a grade of 54.38% and a recovery rate of 54.28% was obtained; at the same time, a high-grade zinc product was obtained. Both tin and zinc were effectively recovered.
3. The main minerals recovered in a tin-iron ore are iron minerals and tin minerals. The iron minerals are mainly magnetite and mu magnetite, and the tin minerals are mainly cassiterite. Through the ore dressing test of this cassiterite, the designed process flow is: first use weak magnetic separation to select magnetic iron minerals, then grind and select the magnetic coarse concentrate, and the tailings of the two stages of magnetic separation are combined into reselection, and the ore dressing is completed through the magnetic-reselection process.
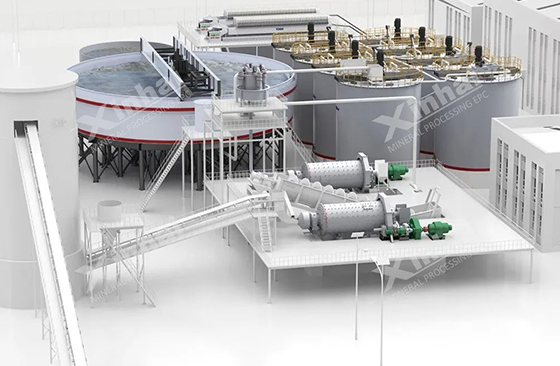
The above is an introduction to the tin ore dressing technology and several tin ore process flows. In actual beneficiation plants, since the properties of each tin ore are different, it is recommended to conduct beneficiation test analysis and design a suitable tin beneficiation process flow through experiments to achieve an ideal tin recovery rate.