Iron is an important mineral resource for sustainable economic development. In some areas, iron ore resources are mainly "poor", "fine" and "miscellaneous". Therefore, iron resources are not enough to meet the needs of economic development. It is urgent to rely on complex and refractory iron ore to increase reserves and increase efficiency and ensure iron and steel production. The industry continues to develop steadily. Let's take a look at what are the refractory iron ore? How to choose?
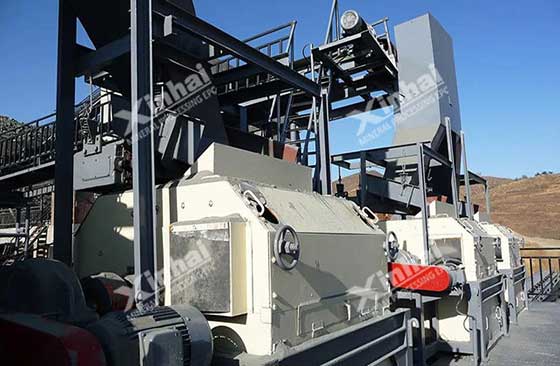
At present, refractory iron ores include siderite, limonite, oolitic hematite, composite iron ore, and high-sulfur and phosphorite.
Use the table of contents below to navigate through the guide:
01Refractory siderite beneficiation method
The grade (theoretical grade) of siderite is low, only 48.02%, and it is often symbiotic with calcium, magnesium and manganese. The available beneficiation methods for this type of iron ore include gravity separation, strong magnetic separation, flotation, roasting and combined beneficiation. However, if the physical beneficiation method (gravity separation, strong magnetic separation, flotation) is adopted, it is difficult for the grade of iron ore concentrate to reach more than 45%. If the roasting method is used, the grade of iron concentrate can be greatly improved, but some useful minerals will be lost during the roasting process. The combined beneficiation method needs to select different combined processes for different types of siderite.
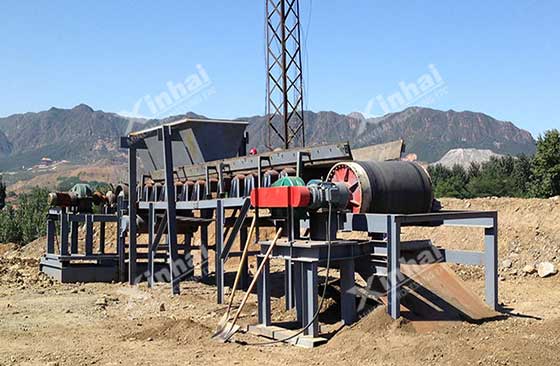
Coarse and single embedded siderite: This ore is suitable for jigging or heavy medium beneficiation, strong magnetic separation, roasting magnetic separation, and combined beneficiation processes.
Siderite with fine embedded particle size: This ore is generally suitable for roasting magnetic separation, strong magnetic separation, flotation or combined maglev beneficiation process.
Multi-associated siderite ore (magnetic-siderite or magnetic-red, brown, mirror iron ore): This kind of ore generally adopts weak magnetic separation and roasting magnetic separation, gravity separation, strong magnetic separation and magnetic levitation series process.
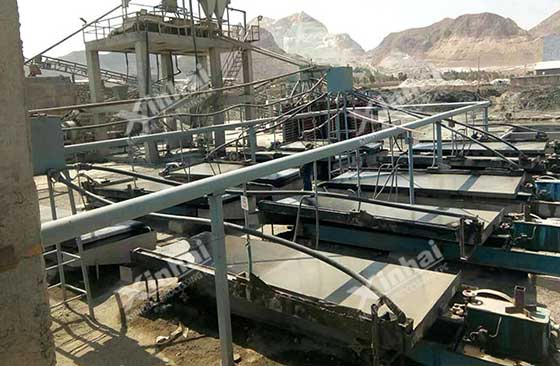
02Refractory limonite beneficiation method
Limonite is rich in crystal water, its iron content is not fixed, and its grade is higher than that of siderite (48%~62.9%). In addition, because limonite is easily sludged during the crushing and grinding process, it is difficult to obtain a high metal recovery rate. Roasting, strong magnetic separation, gravity separation, flotation and their combined beneficiation methods are mostly used in beneficiation methods. Among them, the roasting method is similar to the siderite beneficiation, and the iron concentrate grade is improved during roasting, but the loss is relatively large. However, the iron ore concentrate obtained by single gravity separation, magnetic separation, flotation and other methods is difficult to reach more than 60%. For the combined beneficiation methods, there are gravity separation - strong magnetic separation method, flocculation - strong magnetic separation method and original magnetization roasting - weak magnetic separation method, etc. The specific process should be selected according to the properties of the ore.
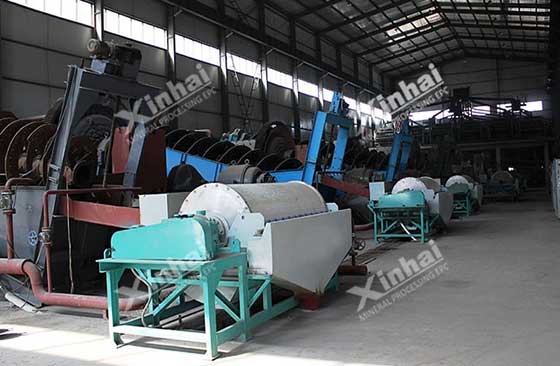
Limonite with single particle size embedded in coarse particles: This ore is suitable for gravity separation - strong magnetic separation method.
Low-grade, fine-grained limonite: This ore is suitable for flocculation-strong magnetic separation or original magnetization roasting-weak magnetic separation.
03Oolitic hematite beneficiation method
Oolitic hematite is embedded with extremely fine particle size and often coexists or wraps with siderite, oolitic chlorite and phosphorus-containing minerals, so it is very difficult to select. Conventional single beneficiation methods and combined methods cannot effectively recover -10μm fine-grained iron minerals. If you want to improve the iron ore concentrate, you need to carry out ultra-fine grinding first. The beneficiation method can adopt the combined process of ultrafine grinding-selective flocculation (agglomeration)-strong magnetic separation or flotation, reduction roasting-ultrafine grinding-selective flocculation (agglomeration)-weak magnetic separation or flotation, etc. Improve iron recovery. But the ultrafine grinding process is more difficult.
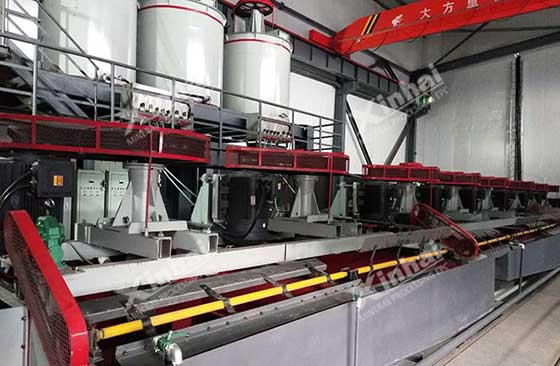
04Compound iron ore beneficiation method
Most of the iron ores in my country contain two or more iron minerals, and the more types, the worse the options. When this type of iron ore coexists with weak magnetic iron minerals such as hematite, mirror iron ore, goethite, siderite and limonite, conventional beneficiation methods can be used to sort this type of iron ore. However, when there are many siderites and limonites in the minerals, the conventional beneficiation method cannot guarantee its concentrate grade and recovery rate, and combined processes such as weak magnetic-strong magnetic-flotation process, magnetization roasting-reverse flotation process are required. and other combined processes to recover iron ore concentrate.
When iron ore symbiotic fluorite, carbonate, silicate and other minerals, the weak magnetic-strong magnetic-reverse flotation method is mostly used.
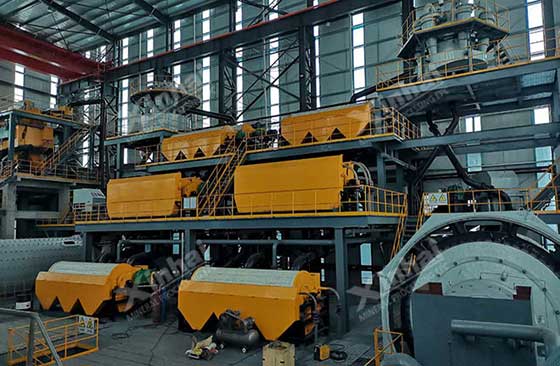
05Beneficiation method of high sulfur and phosphate iron ore
Some iron ores contain harmful impurities such as sulfur and phosphorus, especially iron ores rich in pyrrhotite, fine-grained apatite or collophosphate, which are more difficult to beneficiate. At present, the commonly used beneficiation methods for high-sulfur and phosphate iron ore are mainly combined processes mainly composed of flotation and roasting.
High pyrite: Combined processes such as magnetic separation, reverse flotation, selective flocculation, acid leaching, chlorination roasting and acid leaching are often used.
High-phosphorus iron ore: Combined processes such as flotation, selective flocculation, and roasting are often used.
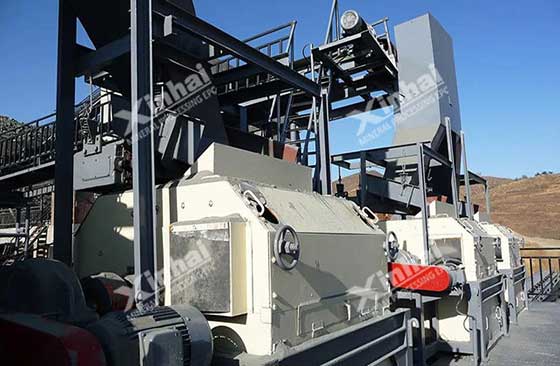
The above are the five common types of refractory iron ore beneficiation methods (ore dressing process). Although this type of iron ore is difficult to select, the value of comprehensive recovery is considerable by choosing suitable beneficiation process methods and suitable beneficiation equipment. To this end, Xinhai suggested that the beneficiation test should be carried out on the refractory iron ore first, and through the test analysis, a suitable beneficiation process plan and matching beneficiation equipment should be customized to obtain an ideal return on investment.