Due to different kinds of mineral and deposit conditions, the mineral product could be row mineral, concentrate or metal. Magnetite beneficiation cost is the whole expenses in magnetite exploitation process and corresponding auxiliary facilities technology process. Unit mineral factory cost or unit mineral selling cost concept is used by mining machinery. They refer to whole allocated product cost or selling cost by processing one-ton row mineral.
In mineral economics evaluation, magnetite beneficiation cost is classified into fixed cost, variable cost, and possibly variable cost, according to the condition whether cost varies from the output. Among those, fixed cost refers that cost does not vary from output within the certain range of output, like equipment depreciation cost, repair cost, management cost, financial cost and so on. Variable cost refers that cost varies with output change, like row material, fuel power, and etc. Possibly variable cost refers that cost changes unsurely with output change, and it should be analyzed specifically according to machinery conditions. For example, according to present wage system, basic salary belongs to fixed cost, but if floating wage, piece wage, and extra rewards are conducted, they belong to variable cost.
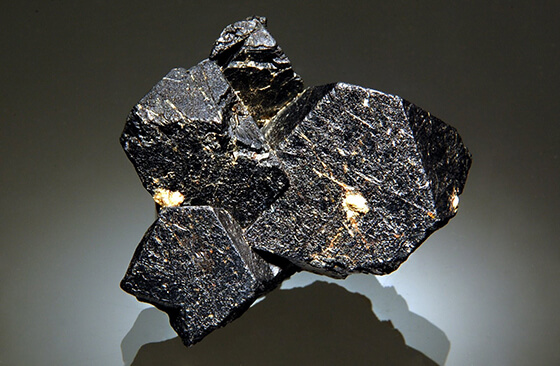
There are two methods of estimation on magnetite product cost, which are unit mineral product cost estimation and partial estimation method. Unite mineral product cost estimation refers that cost is adjusted according to similar mining practical cost selecting corresponding enlargement index. Partial estimation method refers to estimating and accumulating main projects partially, calculating mining costs, beneficiating costs, and then calculating the whole costs. Magnetite beneficiation cost includes raw material cost, supplementary material costs, fuel and power costs, salaries of workers and additional charge, maintenance costs, depreciation costs on fixed assets, manufacturing expense of workshop and company management costs.