With the continuous increase of the energy cost, the magnetite beneficiation plants according to their own conditions keep looking for key points of energy saving. During the process of crushing, grinding, classifying, thickening, filtering, and materials conveying, how can it ensure that it minimizes the beneficiation cost while reaching the technical specifications of mineral particles at the same time? Here comes the introduction of ways to save energy and increase the mineral particles for magnetite beneficiation plants.
Use the table of contents below to navigate through the guide:
01More crushing and less grinding, ensuring that grinding particles are reasonable
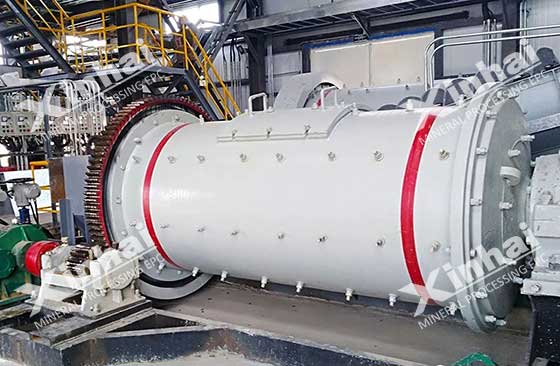
Through the production experience, we can see, that 60% of energy is consumed in the grinding operation during the whole beneficiation process. Among that, 20%-30% is consumed in the crushing process, and 70%-80% is consumed in the grinding process. In the production process, if magnetite beneficiation wants to transform equipment, the key points to achieve energy-saving based on ensuring the crushing ability, are to reasonably adjust the discharge ports of crushers in each process, fully realize the comprehensive ability of the crushing system, and lower the final product particle size in the crushing process, by reducing the pressure of the grinding process and increasing the grinding efficiency and mineral particles to raise the whole capacity of beneficiation plants.
02By experiment and on-site test, decide a reasonable index of dry separation
The pre-selection before ore grinding in magnetite beneficiation is an important breakthrough. In order to maximize the profits of beneficiation plants, according to the market price and ore particles, it should adjust the dry separation index of the ore before grinding whenever necessary. Firstly, it can adjust the height of material distribution boards in the dry separation, ensuring the tailing proportion meanwhile expelling the non-magnetic ore. Secondly, adjusting the distance between the dry separation board and the magnetic roller can ensure the recovery rate of the dry separation concentrate. Besides, by adding material layers and flat feeders, trying to make material layers of dry separation thin and uniform, can guarantee the dry separation effect and improve the particles.
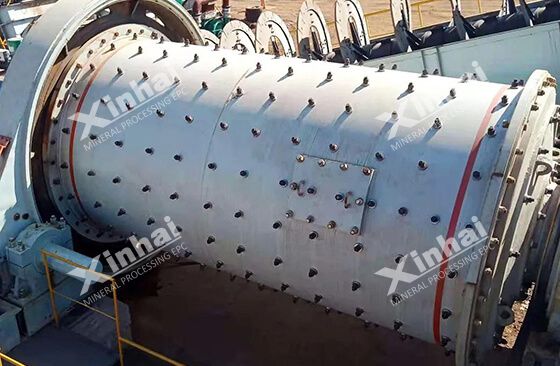
03Improving the grading parameters of the grinding and classifying, and increasing the grinding efficiency
Keep the primary grinding concentration between 75% and 82%, and the secondary grinding concentration between 65%-72%. Meanwhile, a reasonable system of adding balls should be made. According to different material particles, the quantity and sizes of balls, as well as an appropriate time of adding balls, should be made.
04Popularizing new equipment and optimizing the technological process of magnetite beneficiation plants
Xinhai Machine Design& Research Institute undertakes tasks of equipment research &development, design, and improvement. It has made great progress in studying the energy saving. The energy-saving ball mills it produces have widely received a good reputation in practical application.