With the privation of mineral resource, the intelligence and enlargement of mineral processing equipment, and the development of mineral processing equipment, there are higher requirements of the efficiency, reliability, stable process parameters, and product qualities in processing plant. Therefore, the mineral processing automatic control system is promoted, which is steadily becoming the essential technology of modern mineral processing. At present, the mineral processing automatic control technology becomes the essential and effective way realizing mineral processing plant normal production and the improvement of mineral processing plant efficiency.
To meet the demands of modern mineral processing plant production, Xinhai Mining focus on the design and engineering of mineral processing for over ten years, which has accumulated rich experience in industry automatic control area. It has comprehensive mineral processing automatic control system applications for many processing plants. It not only guarantees the mineral processing quality and production index, increases the production efficiency, but also reduces labor cost and energy consumption, and optimizes the operation period.
Use the table of contents below to navigate through the guide:
011. Mineral processing plant complete flow comprehensive automation
According to the production of mineral processing, online measuring instrument, controller, computer technology and automatic control method are applied for measuring, simulating, controlling and managing producing equipment and processing flow. Using optimized deployed labor to increase the product efficiency and product quality for the whole flow, reducing the production costs and increase the competitiveness of enterprise.
(1) Crushing automatic control
The process sequence control of crushing process. Crushing equipment workshop realizes the electrical interlock protection, equipment start and stop according to the order, the concentration and local start and stop, and interlock protection control.
The procedure control of crushing process and index measurement. Controlling the fundamental large equipment or equipment influencing producing process. Guaranteeing the high-efficiency operation of equipment.
The safety monitoring of crushing process. Detect and alarm the main parameters that affect production and participate in system linkage.
Reduce the labor intensity of workers, reduce the failure rate and maintenance of equipment, to achieve the goal of reducing staff and increasing efficiency.
(Crushing automatic control and measuring point)
(Ore bin auto feeding)(2) Grinding and classification automatic control
Improve the grinding mill capacity on the premise of stable grinding fineness. Automatic adjusting the feeding amount, feeding water amount, avoiding grinding mill over full or empty. Automatic control can increase capacity 2%~3% compared with traditional artificial control.
According to the process requirements and the change of ore properties, the grinding concentration of the mill can be stabilized, so that the grading production process is stable and the process index is stable.
A cyclone feed concentration and pressure detection and control loop and a feed pump tank level detection and control loop are established to ensure the grading effect of the cyclone, so that the slurry overflow particle size meets the technical requirements, and create conditions for the next process to transport high-quality slurry and improve the recovery rate.
Measure the liquid level of slurry pump pool, and adjust slurry pump operation frequency. Avoiding overflow or empty in pump pool.
Through detection, real-time monitoring and start-stop control of the running state of equipment in the whole process (special consideration is given to the start-stop of large equipment such as mill), the failure rate of equipment can be reduced and the operation rate can be improved.
Through the application of automation system, increase the worker qualities and knowledge, reduce the working strength. Therefore they have more time for innovation and thinking for long-term development of enterprise.
(Grinding and classification automatic control and measuring point)
(The control of flotation liquid level)022. Production supporting system
(1) Video monitoring system
Video monitoring system applies the advanced high - definition network infrared digital monitoring system. All video capture images are displayed, stored and controlled in the central computer room. The system can be divided into three parts: front-end HD infrared digital network camera part, transport network part, and terminal video display and storage control section.
(Video monitoring system)(2) Center control room large screen display system
The mineral processing industry large screen system is mainly used for displaying video monitoring screen and DCS process screen. It mainly sets in monitoring room where can concentration monitoring and controlling the whole mineral processing plant.
At present, the big screen splicing wall has functions as single screen display, full screen display, arbitrary segmentation, image capture screen and network capture screen and other functions. The operation is more flexible and changeable.
(Center control room large screen display system)03The application cases of comprehensive mineral processing automatic control system
Case 1. Morocco silver processing project
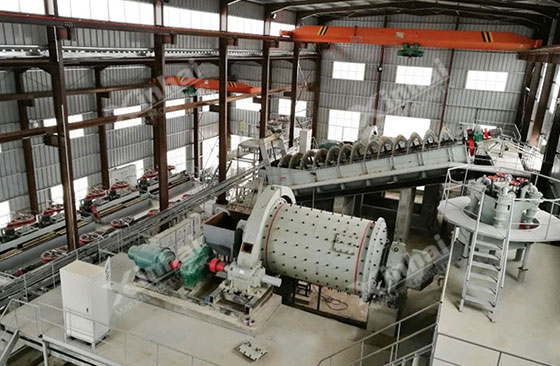
Xinhai Mining provides Morocco silver processing project the comprehensive mineral processing automatic system. The operators can handle the relative index and equipment operation situation in concentration control room. The centralized control room is equipped with 2 people per shift, three shifts per day, unattended on site, and equipped with inspectors to conduct regular inspections on the operation of on-site equipment. At present, this system has operated for two years. Field instruments and control equipment are in good operation, which is highly praised by clients.
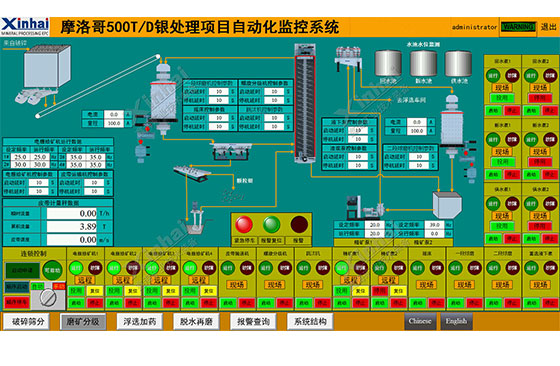
Case 2. Fiji gold processing project
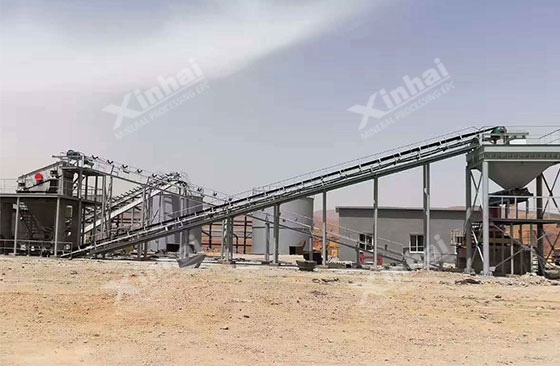
Fiji gold processing project has deal with gold tailings and gold raw ores origin capacity 3000 tons per day. The automatic control system deployed by Xinhai Mining including gold raw ore flotation control system, gold slime flotation automation control system, and roasting cyanidation. The system adopts advanced test instrument, electrical control system and field bus control system. In the design of automatic control system, Xinhai Mining combined advanced control technology, information technology, internet connection technology and computer technology. Thus the advanced mineral processing automatic control system is completed. The implementation of the system make the processing technology stable, increase the recovery rate and grade, and also obviously reduce the system maintenance costs and optimize the operators station, reducing the working strength.
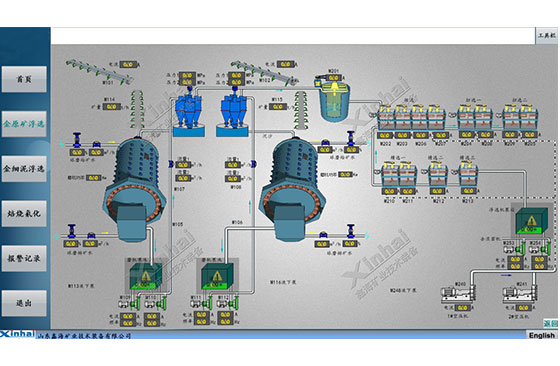
Case 3. Pakistan copper processing project
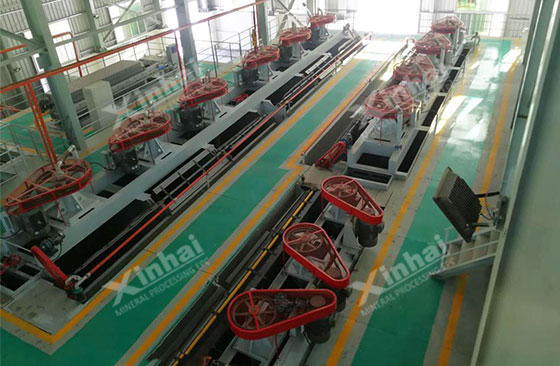
Xinhai Mining provides the Pakistan copper processing project two PLC control system for automatic control system. It mainly completes the crushing process and ball mill concentration control process signal acquisition and control. PC monitoring system has the centralized monitoring and control function operation, realize the dynamic display of the control process (various operation signal of motor current, material level, crushing equipment running status are displayed on the process diagram), the centralized control of equipment on the spot or single control, all kinds of data report, variable trend, operation records, alarm records query, and other functions.
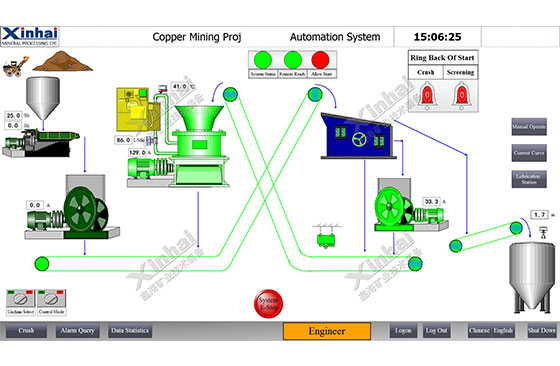
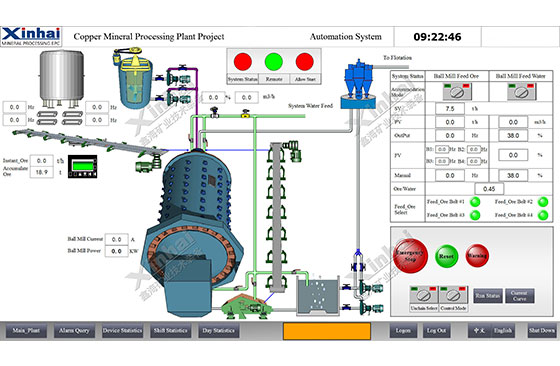