In the mineral processing industry and metallurgical industry, screening is an indispensable operation link. Whether it is crushing, grinding, or sorting, dehydration and washing, the efficient operation of screening operations will directly affect the output and cost of the mineral processing system. Through screening operations, particle size classification can be achieved, the subsequent mineral processing process can be optimized, the mineral processing efficiency can be improved, and unnecessary energy consumption and wear costs can be reduced. Therefore, the reasonable selection of screening equipment and the optimal design of screening technology are the key to ensuring the efficient operation of the mineral processing production line. The following will introduce you to the types, characteristics and applications of screening equipment in production, and help you understand screening equipment and screening operations.
Use the table of contents below to navigate through the guide:
01Common types of mineral processing screening equipment
Based on the structure and working characteristics of the screening equipment, screening equipment can be divided into the following types:
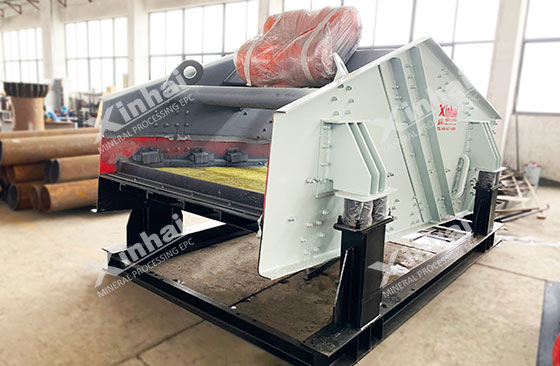
1. Fixed screen: types include fixed grid screen, fixed bar screen, cantilever bar screen and arc screen. This type of fixed screen has the characteristics of simple structure and low cost, and is suitable for primary screening of large ores, but the screening efficiency is low.
2. Cylindrical screen: types include cylindrical screen, conical screen and pyramidal screen. Cylindrical screen is suitable for ores with high moisture content, and can effectively remove soil and impurities in the ore, so it can be used in the ore washing process of mines.
3. Parallel shaking screen: This screening equipment has the characteristics of high screening accuracy, but the processing volume is small, and it is often used for fine screening operations.
4. Vibrating screen: Common vibrating screens include eccentric vibrating screen, self-centering vibrating screen, linear vibrating screen, etc. Vibrating screen has high screening efficiency and high productivity, is suitable for screening of medium and fine particles, and is not prone to blockage during operation. Vibrating screen has the advantages of simple structure, easy operation and adjustment. It is often used in mineral classification, dehydration and desludging operations. It is suitable for medium and fine particle screening in large and medium-sized ore dressing plants.
02Classification and characteristics of mining vibrating screens
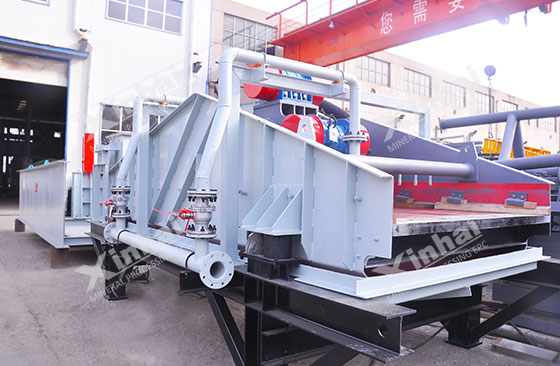
Vibrating screens can be divided into three categories: eccentric vibrating screens, self-centering vibrating screens and linear vibrating screens.
Eccentric vibrating screens: Due to the large vibration amplitude and low screening efficiency, it is prone to clogging, so it is less used in mineral processing.
Self-centering vibrating screens: It overcomes the shortcomings of eccentric vibrating screens and inertial vibrating screens, so it is widely used in mineral processing plants.
Linear vibrating screens: It has high adaptability and screening efficiency, so it can be used for screening materials of different particle sizes.
Advantages of vibrating screens:
- High screening efficiency: When the equipment is running, the screen surface moves strongly, the speed at which the material passes through the screen holes is accelerated, and the production efficiency and screening efficiency are high.
- Wide range of applications: Vibrating screens can be used for screening fine particles, medium and coarse particles, and can also be used for dehydration and desludging operations.
- Not easy to block holes: For viscous and relatively wet ores, vibrating screens are not easy to block holes, and have higher working stability.
- Simple structure and easy operation: The screening equipment has a simple structure, is easy to maintain and adjust, and has stronger adaptability.
- Low energy consumption: The screening power consumption per ton of material is low, and the economy is high.
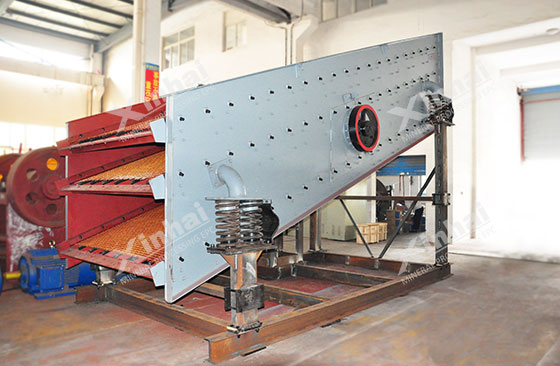
Features of self-centering vibrating screen
- Good stratification effect of materials on the screen: the materials can be fully loosened and stratified under the action of vibration, and the screening efficiency is improved.
- Adjustable amplitude: The amplitude of the self-centering vibrating screen is adjusted by counterweight, which can adapt to different production requirements.
- Scope of application: Suitable for screening of medium and fine particles, not suitable for screening of coarse materials.
03Factors affecting screening operations
The factors affecting screening operations mainly include the following three categories:
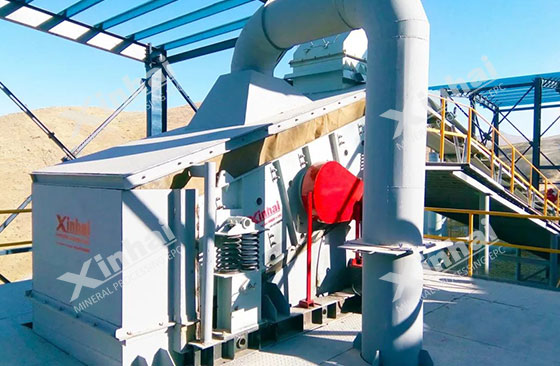
1. Physical properties of the material entering the screen
The physical properties of the material entering the screen affect the screening efficiency mainly in terms of particle size composition, humidity, mud content and ore mud shape. The more uniform the particle size distribution, the higher the screening efficiency. High-humidity materials tend to adhere to the screen surface, resulting in pore blockage. When the mud content is too high, fine-grained minerals tend to adhere to large particles, thereby affecting the screening effect. Flake or needle-shaped mineral particles have poor screening permeability, which increases the difficulty of screening.
2. Screen surface motion characteristics and structural parameters
Screen surface motion characteristics and structural parameters directly affect screening efficiency and production capacity. Changes in amplitude and frequency will affect the screening effect of materials; the length, width and effective area of the screen surface determine the screening production capacity; and the shape (such as square holes, round holes) and size of the screen holes are directly related to the screening accuracy and classification effect.
3. Operating conditions
Operating conditions have an important influence on the screening effect, mainly reflected in productivity and uniformity of ore feeding. The level of productivity will change the load of the screening equipment, thereby affecting the screening efficiency; and uniform ore feeding will help the uniform distribution of materials, improve screening efficiency and production capacity.
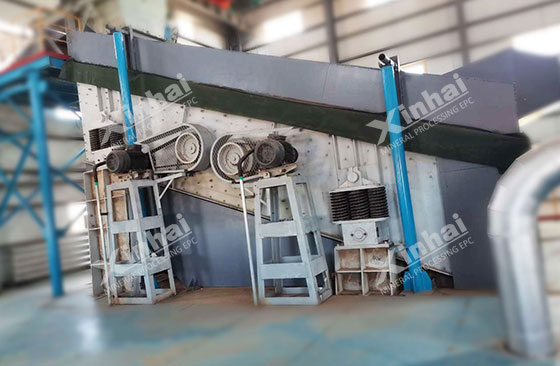
The above is a simple explanation of screening equipment and screening influencing factors. The selection and use of screening equipment will directly affect production efficiency and product quality. By selecting reasonable screening equipment and optimizing the screening process, the screening efficiency can be greatly improved and the production cost can be reduced. In actual production, the selection of appropriate screening equipment needs to be based on the properties of the ore and production requirements, and the production efficiency and ore feeding uniformity should be adjusted during the screening process to ensure efficient and stable operation of the screening operation.