Vibrating screen is an important equipment for mine production. It is mainly responsible for screening, impurity screening and other work, promoting the improvement of production efficiency and quality, and improving the continuous operation capacity of the mine. However, in the actual operation of the vibrating screen, there will be some problems, which will affect the screening quality and the efficiency of the ore dressing plant. From the following, you will learn about several types of faults and solutions that are prone to occur during the use of vibrating screens.
Use the table of contents below to navigate through the guide:
01Bearing failure of vibrating screen exciter
The exciter bearing is a key part of the exciter system and has a direct impact on the operating efficiency and operating quality of the vibrating screen.
If the exciter fails, it will inevitably lead to the unreasonable operating efficiency of the vibrating screen. Under normal condition, the exciter will overheat when the vibrating screen is working, which will affect the machine efficiency. The main causes of exciter overheating are the low matching degree of the exciter bearing model and the exciter, insufficient thermal expansion space of the bearing, poor bearing lubrication or the entry of external dust.
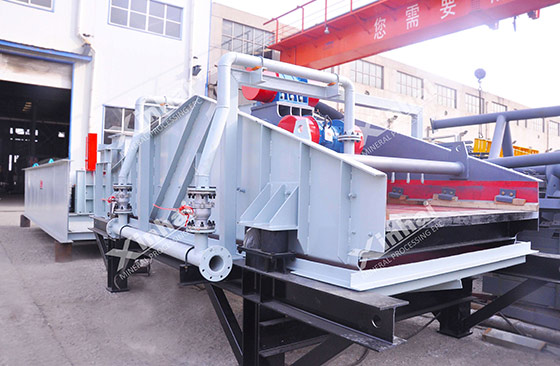
Solution:
According to the actual situation of the exciter bearing fault, it is necessary to reasonably carry out the fault treatment of the exciter shaft, so that the bearing can meet the actual needs of the selection plant, such as:
It is necessary to improve the matching of the bearing, and select the accurate type of bearing according to the specific situation of the vibrating screen. At the same time, you need to ensure sufficient clearance of the bearing as much as possible, reduce the heat generated during the use of the bearing, and improve the functionality of the bearing.
The scientific control of the expansion space of the exciter bearing promotes sufficient space inside the bearing.
Reasonably expand the lubricating oil dripping of the bearing to control the sealing performance of the bearing. Use the appropriate type of lubricant to reduce bearing friction. Avoid the entry of external raw materials or dust, ensure the functionality of the bearing, and improve the screening quality of the vibrating screen.
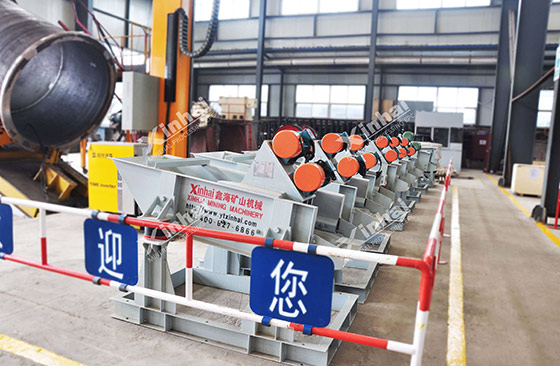
02Structural failure of the vibrating screen
The beam and frame of the vibrating screen are important structural parts of the vibrating screen, which have a direct impact on the stability and reliability of the vibrating screen. However, in the actual use process, it will be affected by factors such as corrosion, impact and friction of materials, etc., which will affect the strength and rigidity of structural parts, resulting in the appearance of cracks. When the cracks accumulate to a certain extent, it will cause the beam and frame of the vibrating screen to break. This may result in insufficient secondary eccentricity of the exciter, which will seriously affect the screening efficiency and quality of the dressing plant.
Solution:
If the structural parts fail, it is necessary to select the materials of the beams and frames reasonably, so that they can conform to the basic conditions of the vibrating screen and play the functions of management and pipe frame. The cracks of the structural parts are riveted or welded by the plywood. If they are broken, they need to be replaced in time.
In addition, in order to ensure the stability and safety of the structural parts, when the screen plate is replaced, it is necessary to apply a tightness to avoid loosening.
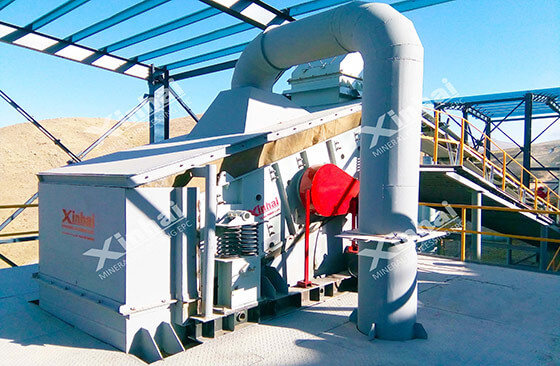
03Poor start of vibrating screen
In actual use, the vibrating screen may fail to start. The main factors that cause the vibrating screen to fail to start are motor damage or circuit component failure. In addition, the maintenance effect of the vibrating screen is not ideal. A large amount of raw material accumulation inside the vibrating screen may also cause the vibrating screen to fail to start.
In addition, if the internal components of the vibrating screen are aged and damaged during actual use, it may also cause noise in the vibrating screen. This will seriously affect the functionality and safety of the vibrating screen and restrict the benefits of the ore processing plant.
Solution:
Enable optimization and noise control. In view of the situation that the vibrating screen cannot be started, it is necessary to strengthen the inspection and inspection of the motor and circuit components. The maintenance personnel shall take appropriate testing and inspection methods to clarify the basic conditions of circuit components and motors, so that they can always be in a
stable operating state. In view of the accumulation of raw materials, maintenance personnel need to carry out cleaning work regularly to improve the operating efficiency and operating quality of the vibrating screen in the dressing plant.
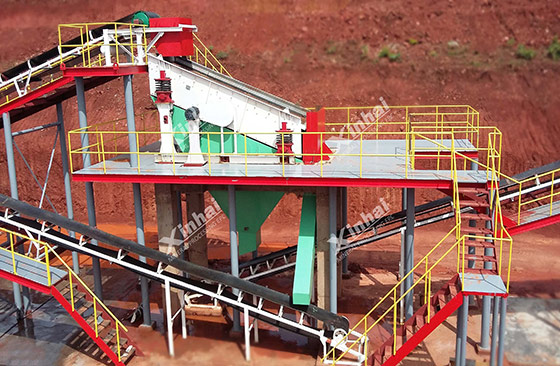
04Noisy of vibrating screen
In the actual application process of the vibrating screen, there will be noise. The generation of noise will lead to greater noise pollution in the processing plant and affect the normal work of relevant staff. Moreover, it is also an important manifestation of equipment failure. There are many reasons for noise failure of vibrating screen. If the vibrating screen is not properly maintained, resulting in damage to the vibrating screen, it may cause noise in the vibrating screen and affect the normal operation of the vibrating screen.
Solution:
In view of the noise situation, the maintenance personnel need to regularly maintain the equipment, so that the internal equipment can always be in a stable operation state, avoid the occurrence of damage, and realize the treatment of the vibrating screen. In addition, in the actual improvement of the vibrating screen in the dressing plant, it is necessary to formulate a perfect maintenance system, improve the efficiency of maintenance management, and regularly carry out the inspection and inspection of the equipment.
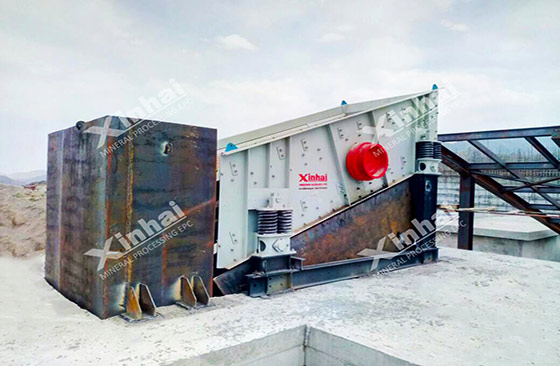
05Imperfect screening effect of vibrating screen
In the application process of vibrating screen, it needs to have good screening ability and screening effect. However, in the actual application process, the screen surface angle of the vibrating screen will affect the vibrating screen. Under normal circumstances, the inclination angle is within 16°≤α≤20°, which can guarantee the effect of the vibrating screen. However, the vibrating screen is affected by external factors, which affects the direction of movement of the eccentric block, which leads to the occurrence of failures, so that the screen box of the vibrating screen cannot perform a complete linear motion, which leads to an unsatisfactory screening effect.
Solution:
In view of the basic situation of the vibrating screen, it is necessary to pay attention to the control of the screening effect, and scientifically manage the screen surface angle of the vibrating screen. If it is found that the angle of the screen surface changes, it needs to be dealt with and suppressed in time to reduce the impact of the screening effect on the dressing plant. For the improvement of the screening effect, the screening effect can be improved by increasing the angle of the screen surface and scientifically adding exciting force. In addition, according to the basic conditions of the feeding trough of the vibrating screen, the feeding trough can be adjusted reasonably, so that the width of the feeding trough can be adapted to the vibrating screen. The material can be evenly distributed to the upper part of the screen surface of the vibrating screen to complete the screening of the material and improve the screening effect of the vibrating screen.
The above are the five types of faults and solutions that are prone to occur during the use of vibrating screens. In view of the failure situation, the vibrating screen operator needs to conduct a specific analysis first, and then take effective improvement measures, so that the vibrating screen can always be in a stable operation state and avoid potential safety hazards.