In the mining industry, barite (barium sulfate) is widely used in many industries such as oil drilling, chemicals and building materials due to its high specific gravity, low hardness and excellent chemical stability. Barite deposits are mainly divided into four types: sedimentary, volcanic hydrothermal and residual slope accumulation. The choice of beneficiation process depends on the specific type of ore and the properties of the original ore. Common barite processing methods include hand selection, gravity separation, flotation and magnetic separation. Regardless of the method used, the beneficiation process usually includes basic stages such as crushing, screening, grinding, grading and sorting. To ensure efficient extraction of barite concentrate, the selection of barite processing equipment should be determined according to the specific beneficiation process. This article will introduce the beneficiation equipment required for each stage of barite.
Use the table of contents below to navigate through the guide:
01Crushing equipment for barite processing
In the barite processing process, crushing equipment is a key link, responsible for crushing large pieces of barite ore to a suitable particle size to achieve the initial dissociation of gangue minerals. This process is usually achieved by one to three stages of crushing:
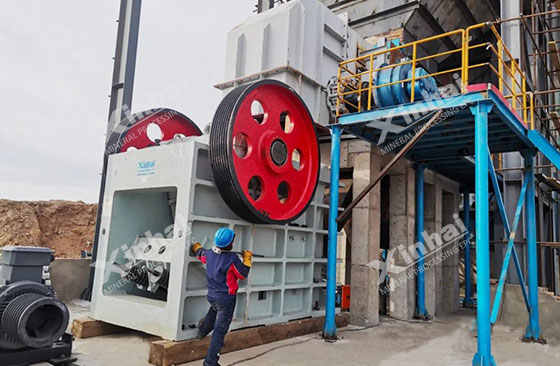
1. Jaw crusher
It has the characteristics of large feed opening and high production efficiency. It is often used for coarse crushing to achieve the initial dissociation of minerals and gangue.
2. Cone crusher
Due to its advantages of large crushing ratio, high efficiency and low energy consumption, it is often used for secondary and fine crushing of barite to ensure the uniformity of product particle size.
02Screening equipment for barite processing
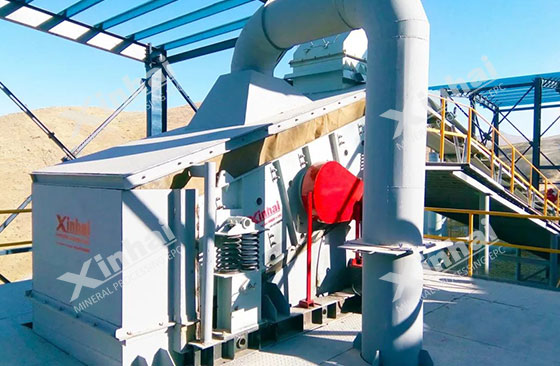
Screening is used to screen the crushed ore to ensure that it meets the particle size requirements of the subsequent sorting stage. Unqualified products are returned to the crusher for re-crushing. Commonly used screening equipment are:
1. Circular vibrating screen
It features a reliable structure, strong excitation force, and high screening efficiency, making it suitable for the screening of coarse-grained barite.
2. Linear vibrating screen
Linear vibrating screen offers stable performance, low energy consumption, and is ideal for the screening of fine-grained barite.
03Grinding Equipment for barite processing
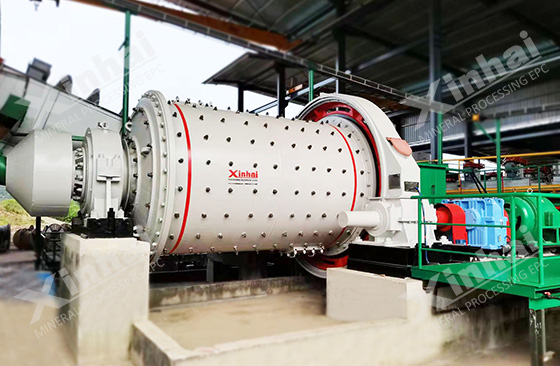
The grinding stage follows crushing and screening, and its purpose is to grind the ore to a selectable particle size and achieve the monomer dissociation of barite minerals and gangue. The grinding process usually adopts one or two stages of grinding. By reasonably matching the grid type and overflow type ball mills, combined with the classification equipment, the particle size distribution of the grinding product is ensured to be uniform and the separation efficiency is improved. Commonly used equipment is the ball mill:
1. Grid type ball mill
It is suitable for the first stage of coarse grinding process, with the characteristics of forced discharge and large production capacity.
2. Overflow type ball mill
It is suitable for fine grinding operations, often used after the first stage of grinding or as a second stage of grinding equipment, with the advantages of automatic overflow of slurry and good grinding fineness.
04Classification Equipment for barite processing
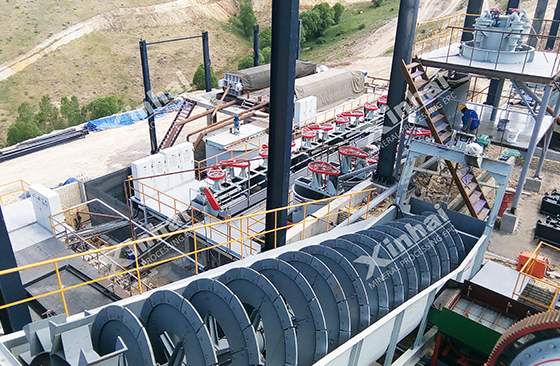
Classification equipment is used to classify the particle size of ore pulp. The ore pulp that meets the particle size standard is ready to enter the beneficiation stage, and the ore pulp that does not meet the specifications is returned to the ball mill for re-grinding. Commonly used classification equipment includes:
1. Spiral classifier
Used in conjunction with the grid-type ball mill, it is specifically responsible for the classification of coarse-grained minerals.
2. Hydrocyclone
Used for the classification of coarse and fine-grained minerals, it is often combined with the ball mill to achieve efficient classification effects.
05Barite Hand Selection Equipment
Hand selection is a simple and direct barite processing method suitable for small-scale mines or high-grade areas. After the ore is crushed, a manual hand selection link is set up during the belt conveyor process. Relying on the color and density differences between barite and associated minerals, the blocky barite is screened out in advance. Its particle size is usually controlled between 30-150mm, and the BaSO₄ content must be higher than 95% (generally not less than 92%). The hand selection method is easy to operate and does not require special mineral processing equipment, but it has low production efficiency, high requirements on the initial grade of the ore, and there is a risk of resource waste.
06Gravity separation equipment for barite processing
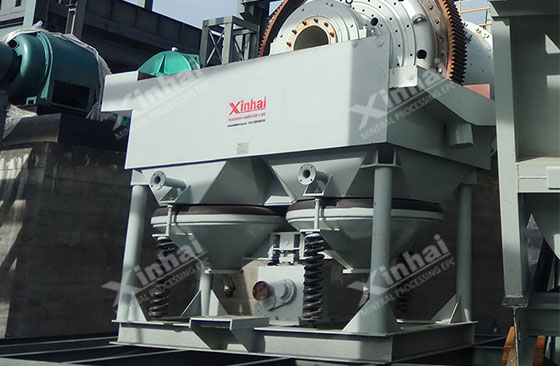
The barite gravity separation method is mainly based on the density difference between barite and associated minerals for separation, and is often used to treat residual barite ore. The gravity separation process includes steps such as washing, screening, crushing, grading and desludging, and then uses jigs, shaking tables and other equipment for separation to obtain high-quality barite concentrate. Commonly used equipment includes:
1. Jigs
It use the vertical alternating water flow generated by the water flow to separate the ore according to the specific gravity to achieve effective separation.
2. Shaking table
It is used to process barite ore with a particle size of less than 2mm, and improve the concentrate grade through the action of the inclined surface and water flow.
3. Spiral chute
It is mainly used to process fine-grained (less than 2mm) and low-mud barite ore, using the centrifugal force generated by the water flow in the spiral trough to separate the barite and gangue minerals according to the specific gravity.
4. Heavy medium cyclone
It is suitable for sorting barite minerals with a particle size range of 0.5~100mm. The gravity separation of minerals is achieved through cyclonic motion and medium density difference, which is suitable for processing high-density barite ores.
07Flotation equipment for barite processing
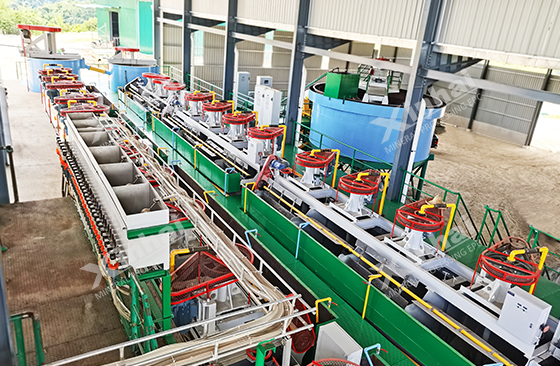
Baryte has good floatability and a specific gravity of 4-4.6. The flotation method is mainly based on the difference in the physical and chemical properties of the surface of barite and associated minerals for sorting. It is often used to treat sedimentary barite ores and hydrothermal barite ores associated with sulfide ores, fluorite, etc. Common equipment includes:
1. Mechanical stirring flotation machine
The impeller stirs the slurry to disperse the air into bubbles. It has strong adaptability and can handle various complex ore types. Commonly used models are SF type and JJF type, which are mainly used for roughing and scavenging operations.
2. Aerated stirring flotation machine
Equipped with a blower device, it requires external air supply to provide more uniform bubbles, increase the collision and adhesion probability of bubbles and mineral particles, and improve flotation efficiency. Commonly used models are XCF type and KYF type, which can be used in combination to complete roughing, scavenging and concentrating operations.
3. Mixing tank
There are high-efficiency mixing tank and reagent mixing tank. The high-efficiency mixing tank is used to fully mix the slurry and reagent, while the reagent mixing tank is used to prepare various reagents.
08Magnetic separation equipment for barite processing
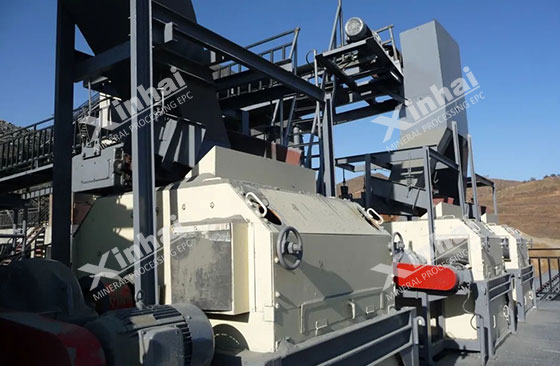
In the barite beneficiation process, magnetic separation is usually used as an auxiliary process, suitable for removing impurities such as iron oxides. Commonly used equipment are:
1. Dry high-intensity magnetic separator
It is suitable for fine-grained and relatively dry barite materials.
2. Wet drum magnetic separator
The magnetic impurities are collected simply and efficiently through the dynamic action of the material and the drum surface.
3. High-gradient magnetic separator
By generating a high magnetic field gradient and using the internal magnetic conductive medium to enhance the separation effect, it has a strong capture ability for weakly magnetic minerals.
In the barite processing plant, the selection and application of equipment should be determined according to the specific properties of the barite ore. It is recommended to first conduct a beneficiation test analysis to understand the ore characteristics and processing requirements, design a suitable beneficiation process flow according to the test results, and equip the corresponding equipment. The specific application of these equipment needs to be adjusted according to the actual beneficiation process to improve the beneficiation index and overall efficiency of the beneficiation plant.