According to the different crushing principle and particle size of size, the types of crusher is divided into many kinds and a variety of new types of crusher have been widely developed, mainly including jaw crusher, cone crusher, impact crusher, hammer crusher, mobile crusher.
Use the table of contents below to navigate through the guide:
A jaw crusher is a type of crusher comprised of two jaw plates. One is a fixed jaw plate that is vertically fixed on the antetheca of the body, and another is a moving jaw plate, forming a crushing cavity with a fixed jaw plate. During the working of this type of crusher, the moving jaw does a periodic motion to the fixed jaw surround the eccentric shaft. When it closes, the materials are crushed by the action of squeezing and impact; on the contrary, the crushed materials are discharged by the gravity from the discharge opening.
The crushing cavity of jaw crushers is deep without dead zone, so the feeding capacity and production of this type of crusher have been greatly increased, featured by large reduction ratio and uniform particle sizes. The jaw crushers have advantages of large production capacity, large ranges of feeding particle sizes, simple and compact structure, reliable operation, easy maintenance and low investments. While it also has disadvantages, such as large noise, large inertia force and small crushing cavity. So, the jaw crusher is mainly used for coarse crushing and intermediate crushing of hard blocky materials.
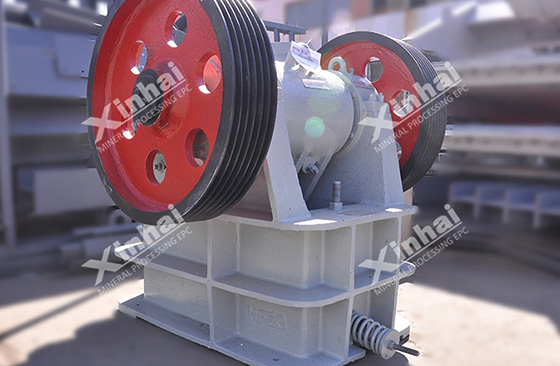
For this type of crusher, the swing route of the cone crusher has important effects on the working performance. When the swing route increases, the feeding compression ratio is increased, the product quality is improved as well as the standard fineness. When the swing route decreases, the quality of crushed products is worsened and the fineness will decrease. Considering the quality, the swing route of this type of crusher shall adopt maximum value. However, the final crushing and compaction should be avoided.
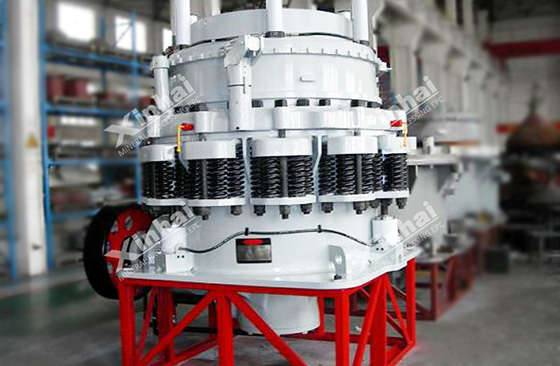
033. Impact Crusher
During the working of this type of crusher, the rotor rotates at high speed driven by the motor. Materials enter the hammer area to be impacted and crushed. Then, they are thrown to the impacting device to take another crushing. After that materials will spring back to the hammer impacting area from impact wrist plate for crushing again. When the materials are crushed to the required size, they will be discharged from the outlet of the hammer crusher. The discharging size and shape of the material can be changed by adjusting the gap between the impact frame and rotator of this type of crusher.
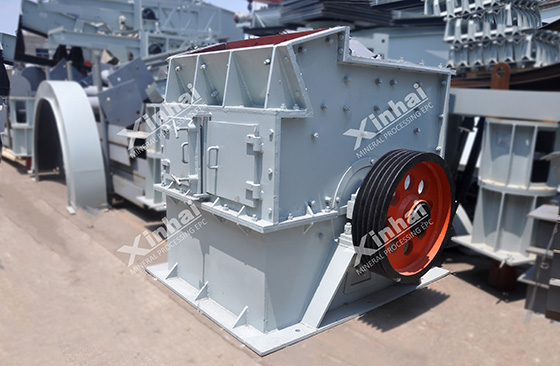
Hammer crushers are available for processing ores into -25mm. Hammer crusher is mainly used in industries such as cement, coal separation, electricity generation, building materials and compound fertilizer, etc.
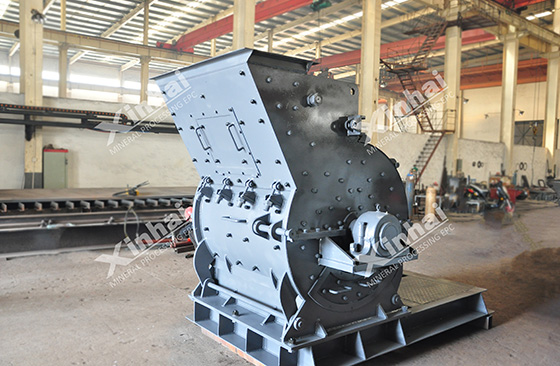
Mobile crusher is a new type of crusher at present, which is featured with stronger mobility and flexibility. The biggest advantage of mobile crusher is that it can move in the production, which brings the convenience to production, and cannot be limited by the region. Therefore, mobile crusher is widely used in large, smelting, building materials, roads, railways, water conservancy and chemical industry.
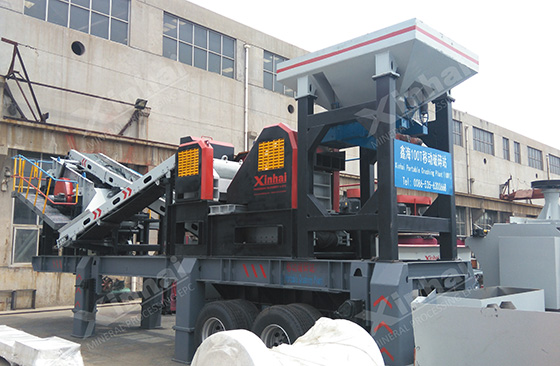
In brief, the model and specification of crusher machines should be in line with the ore characteristics, the scale and location of the mineral processing plant, etc. Generally, the jaw crusher is available for processing the mid-harness ores. The cone crushers are available for mid and fine crushing. Impact crushers can be applied to processing those schistose ores with mid-hardness.
The above are the five types of crushers in the mineral processing, including jaw crusher, cone crusher, impact crusher, hammer crusher and mobile crusher. It is suggested that the types pf crusher shall be selected according to the different mining requirements.