Screen machine is a common mineral processing equipment in industrial production. Due to various factors during the working process, the screen machine may be subject to various damages and failures. Here are some common problems and related solutions of the screen machine.
Use the table of contents below to navigate through the guide:
01The material above the Screen Machine Flows Abnormally
There are two possible factors in this situation. One is that the anti-deformation ability of the screen machine box is not enough, that is, the rigidity of the screen box is insufficient, and the connecting bolt may be loosened, or it may be severe to fully loosen, tightening the connecting bolt can solve this problem. The other factor is the problem happens to the horizontal level of the screen box. This problem can be solved from the support base of the support spring or the support spring itself and by replacing the spring or adjusting the size of the support base. If there is no problem with the support base, it may be a horizontal level problem caused by the damage of the screen mesh, and replacing the screen mesh would solve the problem.
If the above problems cannot be solved in time, the beams of the screen machine maybe going to break if the condition is serious. In addition, improper operation or uneven feeding is also the cause of abnormal material flow.
02The Screen Machine Fails to Start Up or the Amplitude is Too Small
In the case of such a problem, first we should check whether the electrical fault has occurred, whether the vibration motor of the screen machine has been damaged, or whether there is component damage or insufficient voltage in the line. If there is no problem with the above aspects, we can start from the machine and check if there is too much material accumulation on the screen machine. If the accumulated material is too much, we should remove them. If there is no problem in the above part, we should check whether the coupling bolt on the vibration exciter is off, whether the lubricating grease is agglomerated or thickened, we can service and clean the vibration exciter, and then make the appropriate adjustment to the position of the eccentric shaft weighting block or the sub eccentric block.
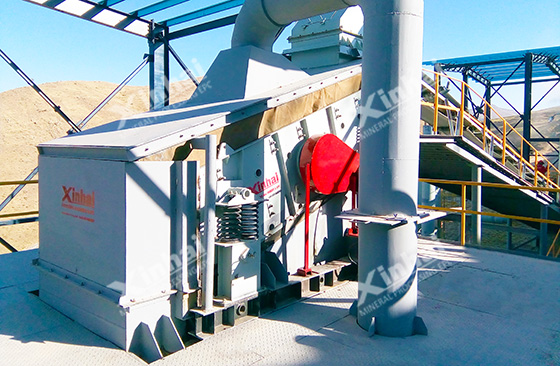
03Screen Machine Bearing Overheats
Under the condition of 4 hours of a trial run, the temperature of the screen machine bearing should be maintained at 35~60 degrees. During the test run, if the temperature is high, there may be three main possible reasons. First, the radial clearance of the bearing is too small, thus the bearing load is increased and the frequency is arising, we should make the bearing have a large clearance and grind some part of the outer ring of the bearing. It is also possible that the bearing gland is over-tightened so that the bearing cannot properly dissipate heat, we should adjust the gasket between the end cap and the bearing housing. It may also be due to the lack of lubricating oil in the bearing or oil contamination, excessive oiling, etc. We should oil and clean the bearing and replace the oil and seal. In addition, it may be a problem of bearing wear or bearing quality.
04Side Plate Cracks, Structural Parts Damage, or Even Beam Breakage of Screen Machine
This kind of situation does not happen suddenly. It is usually caused by too long working time at the critical frequency. There are many kinds of critical frequency conditions, such as high-strength bolts of the side plates loosened, severe spring deformation which causes height difference, eccentric block weight error is too large, etc. The problems above will cause structural parts damage, side plate cracks or even beam breakage. While replacing damaged parts, the above conditions should be overhauled. When repairing the side plates, we should drill holes at both ends of the crack to prevent crack propagation. When repairing the reinforcing plate, we should drill the air holes on the reinforcing plate.
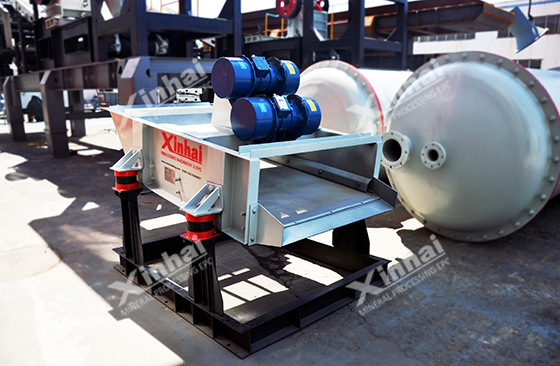
05The Rotation of Screen Machine Turns Slow While the Bearing Heats Up
Most of this happens because there is no maintenance at ordinary times, resulting in the lack of lubricating grease in the bearing. If the grease is newly added, the problem may be caused by the grease quality problem or the addition of too much grease. Inferior grease will cause the bearing to block the sealing jam, so the quality of the grease needs to be guaranteed.
06The Screen Machine Produces Excessive Noise
If the screen machine emits excessive noise during work, the parts of the equipment may be damaged or loose. We should stop the bearings, bolts, beams, springs, etc., and replace or fix the faulty parts in time.
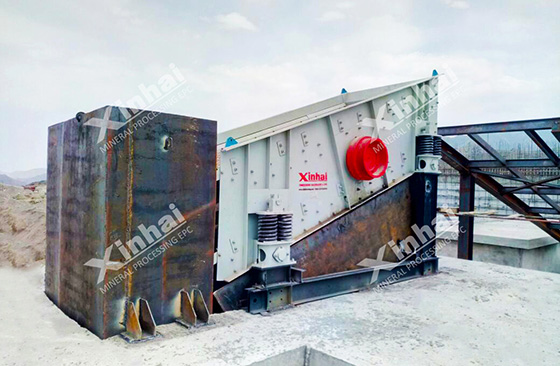
07The Screening Effect of Screen Machine is Not Good
There are many reasons for the poor screening effect of the screen machine. We can analyze the causes one by one.
First, different types of screen machines have different reasons for the poor screening effect. One of the main reasons for the poor screening effect of the circular vibrating screen is that the screen surface angle is insufficient. If the screen surface angle is insufficient, the rear support seat should be raised and the screen surface angle should not be lower than 16°. Otherwise, the material on the screen may not move smoothly or the material may roll upward. For linear vibrating screens and high-frequency vibrating screens, the poor screening effect is mostly related to the direction of movement of the eccentric block and we should adjust it.
In addition, the poor screening efficiency may be caused by the fact that the width of the feed chute is not appropriate, and the actual processing capacity is not consistent with that at the time of design. The screen machine needs to be modified according to requirements to improve the screening efficiency.
The above are some questions and solutions about the screen machine. In actual production, the screen machine operator should regularly maintain and repair the screen machine. When there is a problem, the cause should be identified according to the phenomenon, and the problem should be solved timely to ensure the safe and stable operation of the mineral processing plant.