Magnetic separation is realizing the mineral processing according to the magnetic differences between minerals from magnetic and other mechanical force. At present, it is used in the processing of ferrous metal and non-metal, and the fine processing of non-ferrous metal and precious metal.
To be brief, the working principle of magnetic separator is that the magnetic minerals are magnetization under an uneven magnetic field, and absorbed on the magnetic separator cylinder. Then they are taken to the row of ore terminal as magnetic product. While the non-magnetic minerals are less influence from the magnetic field, still in the slurry as the non-magnetic product.
If we want to achieve the ideal magnetic separation effect, we must first know what factors will affect the magnetic separation effect, so that we can pay more attention in the operation process, so as to obtain a good processing index.
Use the table of contents below to navigate through the guide:
01The particle size of feeding minerals
The particle size of feeding minerals is an important influence factor of the magnetic separator effect. For most ores, the particle size of feeding minerals means the degree of monomer separation, which is also the separation degree of magnetic ore and gangue mineral. If the particle size of feeding minerals is small, it means the separation degree is high. It is easy to get satisfying processing index, If the particle size of feeding minerals is coarse, which means the separation degree is low, the magnetic minerals are still combined with part of gangue minerals. This kind of connective directly affects the ore dressing index and makes the concentrate grade lower. Therefore, the ore particle size of the magnetic separator must fully realize monomer separation.
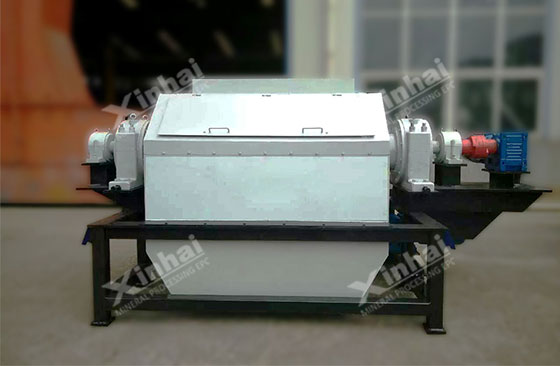
02The concentration of slurry pulp
Here the concentration of slurry pulp is mainly the overflow concentration of classifier. The concentration of pulp is too high, and the concentration of concentrate is too high. In this case, the concentrate particles are easily covered and wrapped by the finer gangue particles, leading to the difficulty in separating the two and seriously affecting the concentrate grade. The pulp concentration is too small, which means the concentration of separation is too low, resulting in an increase in the flow rate, shortening the separation time, and making some fine magnetic particles that could be recovered into the tailings and discarded. The concentration of slurry pulp is less than 35%, about 30%. Of course, the mineral processing plant can decide according to the requirement and situation.
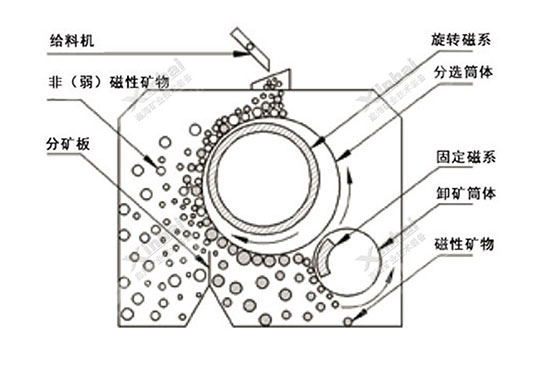
03The rotate speed of magnetic separator
The rotate speed of magnetic separator can largely influence the capacity of magnetic separator, and then impacting the concentration quality. The higher rotate speed is, the larger magnetic separator capacity is. At the same time, the less magnetic ligneous bodies and gangue minerals are difficult to distinguish. Only minerals with large magnetic can be separated. The lower rotate speed is, the smaller the magnetic separator capacity is. By the magnetic induction, ore particles with weak magnetism can also be sorted out, which affects the quality of concentrates.
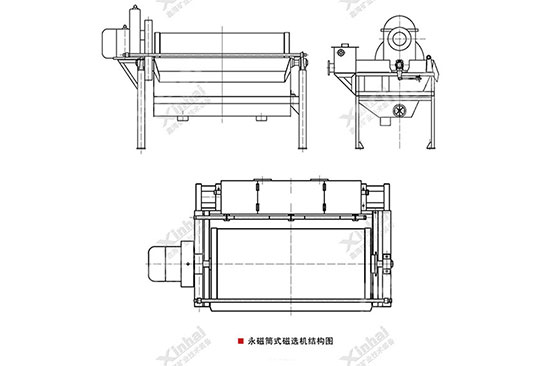
Generally speaking, small diameter magnetic separators with high speed, large diameter magnetic separators with low speed. Taking the permanent magnetic separator as example, the rotate speed of magnetic cylinder is 20r/min when the diameter is 1000mm, while the rotate speed is 30r/min when the diameter is 1200mm.
04The magnetic system angle
Generally speaking, the magnetic deflection indicating device is located on the shaft head near the drive side. The size of magnetic deflection can be adjusted by adjusting the nut. Its influence is most inflected on the quality and recovery rate of concentrates. Taking permanent magnetic separator as an example, the smaller magnetic system angle is, the easier to separate small magnetic minerals. It is helpful in increasing the recovery rate and reducing the grade of tailings at the same time. The larger magnetic system angle is, the easier to separate the large magnetic minerals, which can improve the quality of concentrates.
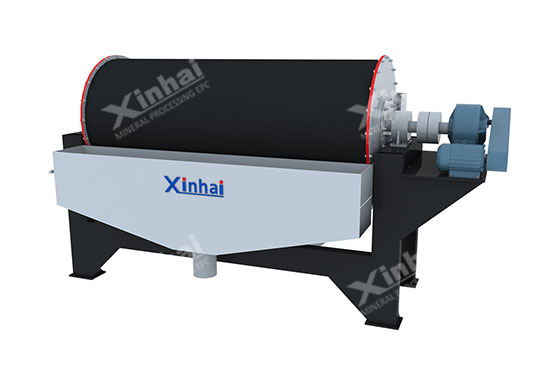
However, the magnetic system angle can not be adjusted at will. It must be adjusted according to the requirements of magnetic separation. Generally, the magnetic system angle is average 15~20°. The magnetic system angle will not change unless large requirement changes.
Therefore, in the production practice, the influence factors of magnetic separator is more than 4 points. Mineral processing experts suggest that before the purchase of magnetic separator equipment, the mine owner should consult professional magnetic separation machine manufacturers and investment costs and other actual conditions, get the ideal magnetic separation parameters, to correctly guide the operation of the magnetic separator, to obtain the ideal separation effect.
Shanxi 1200t/d iron ore processing project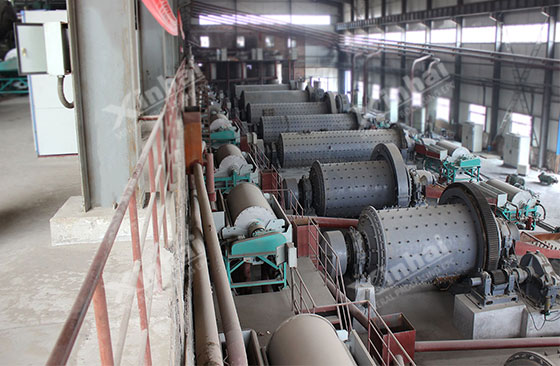
Project introduction:
Shanxi 1200t/d iron ore processing project is a mineral processing EPC+M+O project including mineral processing experiment, mine design, equipment manufacturing and delivery, installation and debugging, worker training, mineral processing management and operation.
Xinhai solution:
1. Crushing and screening stage: particle size of the final product of crushed ore: 12mm. Advanced and reliable equipment selection, less investment; In the design, the crushing and sieving operation is compact and reasonable, which makes the production management very convenient. Fine particle size of crushing products, saving the comprehensive cost of crushing and grinding;
2. Grinding classification stage: the fineness of the first stage grinding products -200 mesh accounts for 67%, and the fineness of the second stage grinding products -325 mesh accounts for 88.47%. The first stage grading equipment adopts the modified spiral classifier, and the second stage grading adopts the fine screen to strictly control the grading granularity.
3. Magnetic separation stage: a rough separation, three times selected magnetic separation process, the slurry is transported by Xinhai mineral wear resistant slurry pump; Tailings conveying stage: iron concentrate is filtered by the permanent magnet filter and transported directly to the tailings yard by the belt, and the tailings flow directly to the tailings ditch outside the dressing plant.
Result:
The project is a new-built mineral processing plant. Xinhai Mining strives to advance and reasonable for equipment selection. The advanced new type energy-saving equipment is selected. The auxiliary facilities are simple to reduce the investment in civil construction. Less investment and more production. Increasing economic efficiency and protect the environment at the same time. The discharge of "three wastes" meets the national standards.